Introduction
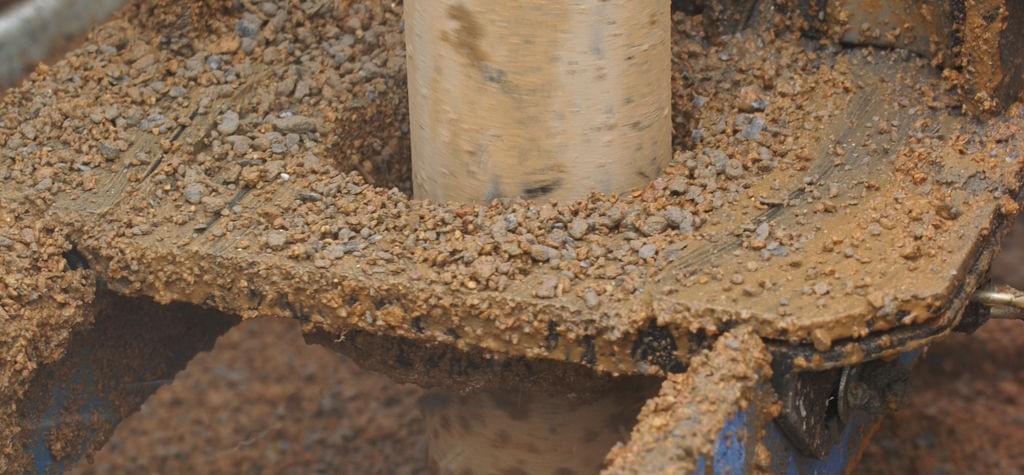
Are you looking to delve into the world of down the hole well drilling? This innovative technique uses a pneumatic drill to penetrate rock formations and create wells for various purposes. With the right equipment and expertise, this method offers efficient and precise results for your drilling needs.
Understanding Down the Hole Well Drilling
Down-the-hole well drilling, also known as DTH drilling, is a rock drill technique that involves driving a drill bit into the ground at the bottom of a hole. This method is widely used in water well drilling, mining, construction, and geothermal projects due to its speed and accuracy in creating boreholes.
Down-the-hole well drilling requires proper equipment to ensure successful and efficient operations. The drill bit, hammer, and compressor must be carefully selected and maintained to achieve the desired results. Without the right equipment, the drilling process can be slow and inaccurate, leading to increased costs and project delays. Therefore, investing in high-quality DTH drilling equipment is essential for achieving optimal performance and productivity.
Importance of Proper Equipment
Well drilling is a complex undertaking, and its success hinges on one crucial factor: proper equipment.
- Matching the Machine to the Terrain: The right drill rig, with the appropriate power and stability, effectively tackles various geological formations.
- Selecting the Right Drill Bit: Choosing the ideal drill hammer bit optimizes drilling speed and precision, while durable button bits guarantee long-lasting performance.
- Ensuring Safety and Efficiency: High-quality equipment minimizes downtime due to malfunctions, keeps workers safe, and allows for a smooth and efficient drilling operation.
Investing in proper equipment is not just an expense; it's an investment in the efficiency, safety, and ultimate success of the entire well drilling project.
Tianhe: Your Trusted Partner in Drilling Solutions
When sourcing top-notch equipment for down the hole well drilling, Tianhe is your go-to partner for quality solutions. With a wide range of products designed for efficiency and durability, Tianhe provides comprehensive support for all your drilling needs. Our products, from drill bits to drilling fluids, are engineered to deliver optimal performance in challenging drilling environments. We understand the importance of reliable equipment in achieving successful drilling operations, so we prioritize quality and innovation in every product we offer.
Selecting the Right Equipment
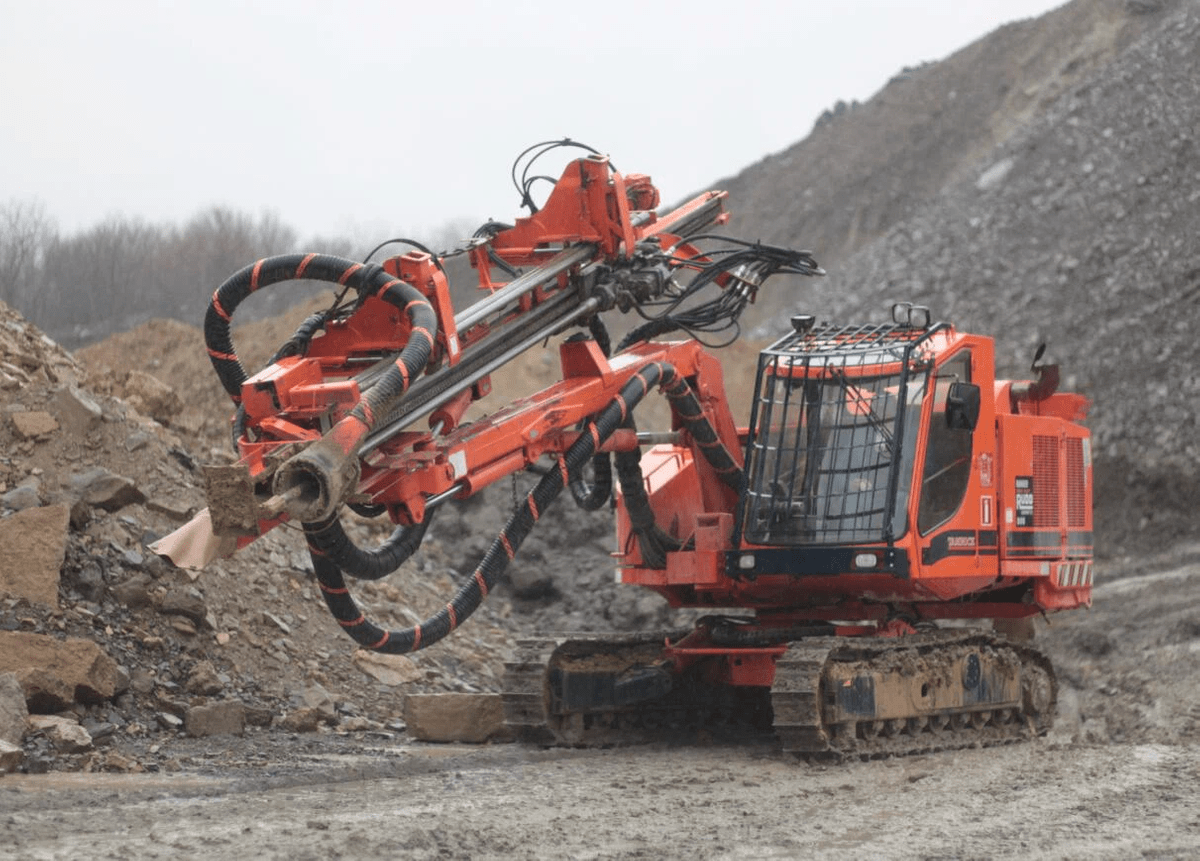
When it comes to down-the-hole well drilling, selecting the right equipment is crucial for a successful operation. One key component in this process is choosing the right DTH hammer. This pneumatic drill tool provides the necessary impact energy to break through rock formations and ensure efficient drilling and well construction.
Choosing the Right DTH Hammer
Selecting the right DTH hammer is essential for achieving optimal drilling performance. Factors such as rock hardness, drilling depth, and air pressure requirements must be considered when choosing a suitable hammer for your well drill project. With Tianhe's wide range of DTH hammers, you can find the perfect match for your specific drilling needs, ensuring maximum efficiency and productivity.
Benefits of Using Button Bits
Button bits are a crucial component for success in down-the-hole well drilling operations. These robust rock drill bits are designed to excel in various formations, offering high penetration rates and extended durability. Their efficient cutting structure and long lifespan translate to significant advantages in cost-effectiveness and performance. Here's a closer look at the benefits of using button bits:
- Faster Penetration Rates: The design of button bits allows them to break through rock formations quickly, saving you time and resources on your drilling project.
- Exceptional Durability: Button bits are crafted with tungsten carbide inserts, renowned for their exceptional resistance to wear and tear. This translates to a longer lifespan for the bit itself, reducing replacement frequency and downtime.
- Versatility Across Formations: Unlike some drill bits that struggle in specific rock types, button bits can effectively handle various formations, offering drilling flexibility for your project.
- Cost-Effective Choice: While requiring an initial investment, button bits' extended lifespan and reduced replacement needs make them a cost-effective solution in the long run.
Button bits are a powerful option for down-the-hole well drilling, delivering speed, durability, and versatility at a competitive cost.
Exploring DTH Drill Bits Options
Exploring different options for DTH drill bits is essential for finding the most suitable tools for your specific well drilling requirements. Whether you need standard or specialized drill bit designs to tackle challenging formations, having diverse options allows you to tailor your equipment selection to achieve optimal results in different geological conditions. Additionally, considering factors such as rock hardness, abrasiveness, and the presence of fractures can help you narrow down the best DTH drill bit options for your project. Furthermore, understanding the different cutting structures and carbide shapes available can also be crucial in selecting the most effective drill bits for your drilling needs.
With Tianhe as your trusted partner in drilling solutions, you can access a comprehensive selection of high-quality DTH hammers, button bits, and drill bit options tailored to your unique project needs. By choosing the right equipment for your down the hole well drilling operations, you can ensure efficiency, precision, and success throughout every project stage.
Site Preparation and Planning
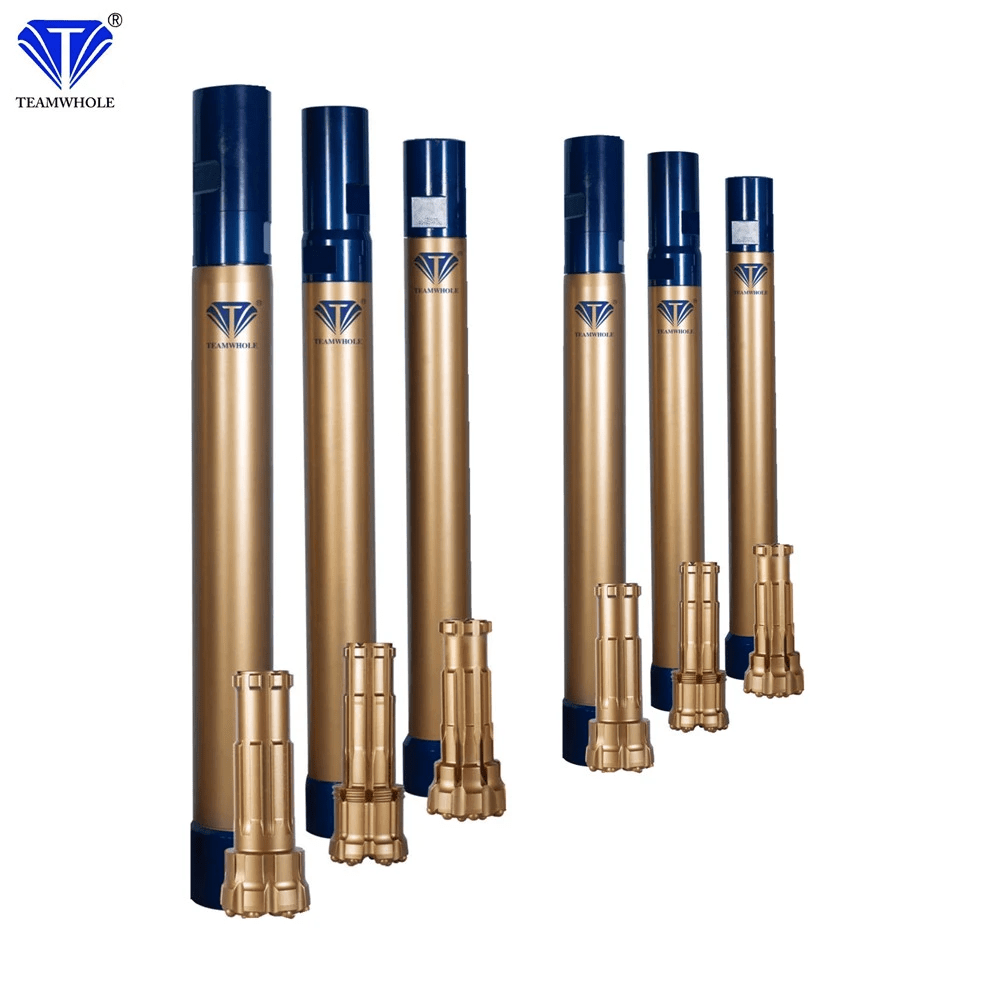
When it comes to down the hole well drilling, proper site preparation and planning are crucial for successful operations. Conducting a geotechnical survey is essential to assess soil and rock conditions, ensuring that the chosen drill equipment is suitable for the specific geological characteristics of the site.
Importance of Geotechnical Survey
A geotechnical survey is an essential first step for any construction project. It investigates the subsurface conditions of a site, providing vital information for safe and economical building practices. Here's how a geotechnical survey benefits your project:
- Understanding Ground Composition: By identifying the types of soil and rock present at the site, engineers can recommend the most effective drilling methods and equipment for foundation construction.
- Assessing Ground Stability: Geotechnical surveys reveal potential hazards like sinkholes, faults, or underground water tables. This allows engineers to design foundations that can withstand these challenges and mitigate risks of structural failure.
- Optimizing Construction Costs: Knowing the ground conditions upfront helps avoid surprises during construction and allows for more accurate cost estimates. This can save time and money in the long run.
A geotechnical survey is a valuable investment laying the foundation for a safe, successful, cost-effective construction project.
Factors to Consider for Site Selection
Selecting a suitable location for your well is crucial for a successful and sustainable water source. Here are some key factors to consider:
- Accessibility: The site should be easily accessible to drilling equipment and vehicles. Consider factors such as road conditions, ground firmness, and potential obstacles.
- Terrain Conditions: The topography of the land plays a role. Ideally, the site should be relatively flat or have a gentle slope to avoid challenges during drilling and well construction.
- Proximity to Water Sources: Look for areas with signs of existing groundwater, such as healthy plant growth in drier areas or low-lying spots where water may naturally collect.
- Environmental Impact: Minimize environmental disruption by choosing a location away from sensitive ecosystems, waterways, or protected areas.
By carefully evaluating these factors, you can select a well drilling site that meets your water needs while respecting the surrounding environment.
Safety Measures for Well Drilling Operations
Safety is paramount in any well drilling project. Implementing comprehensive safety measures, including proper personnel training, regular equipment inspections, and adherence to industry regulations, ensures that all operations are conducted with minimal risk of accidents or environmental harm.
Proper Maintenance and Care
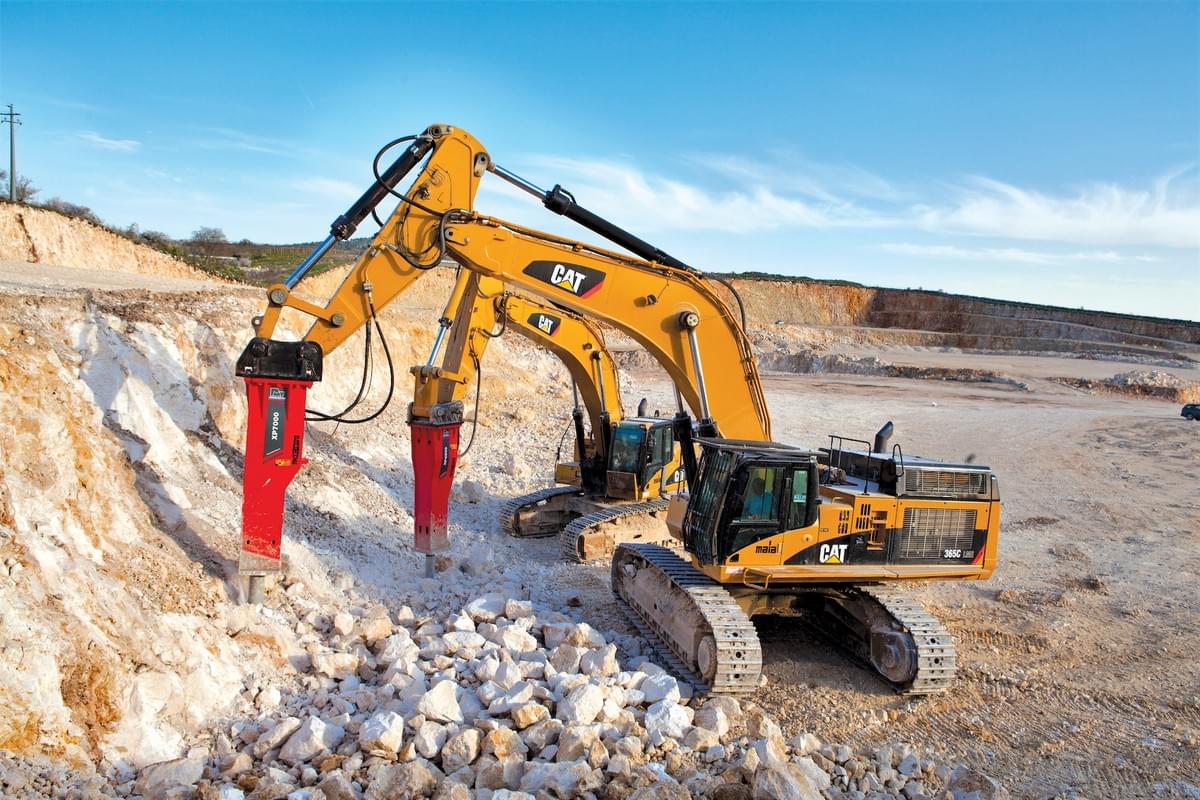
When it comes to down-the-hole well drilling, regular inspections and maintenance are crucial for ensuring the longevity and efficiency of your equipment. By conducting routine checks on your drill bits, drill hammers, and pneumatic drills, you can identify potential issues early on and address them before they escalate. This proactive approach minimizes downtime and prevents costly repairs down the line.
Regular Inspections and Maintenance
To keep your well drilling operations running smoothly, schedule regular inspections of your rock drills, drill hammer bits, and other equipment. Look out for signs of wear and tear, such as dull or chipped drill bits, which can lead to decreased drilling performance and increased fuel consumption. You can promptly replace worn-out components and perform routine maintenance tasks to ensure that your equipment operates at peak efficiency.
Storage and Handling Best Practices
Proper storage and handling of your drilling equipment are equally important in maintaining their functionality. Store drill bits in a dry environment to prevent corrosion, and ensure they are kept away from direct sunlight or extreme temperatures that could compromise their integrity. Additionally, they handle pneumatic drills with care to avoid unnecessary strain on their components, which can lead to premature wear and reduced performance.
Extending the Lifespan of Equipment
Implementing a comprehensive maintenance program for your well drilling equipment can significantly extend its lifespan while maximizing its productivity. Regularly lubricating moving parts, keeping air filters clean, and following manufacturer-recommended service intervals are all effective ways to prolong the life of your rock drills and other machinery. This proactive approach will save you money in the long run and ensure that your drilling operations remain efficient.
In addition to regular maintenance, it's also essential to train your drilling team in effective drilling techniques. Proper drilling techniques can help reduce wear and tear on equipment, leading to a longer lifespan. This includes using the right amount of pressure, maintaining proper speed, and adjusting the drill's angle as needed. By ensuring that your team is well-trained in these techniques, you can further maximize your equipment's productivity while minimizing the need for costly repairs.
Effective Drilling Techniques
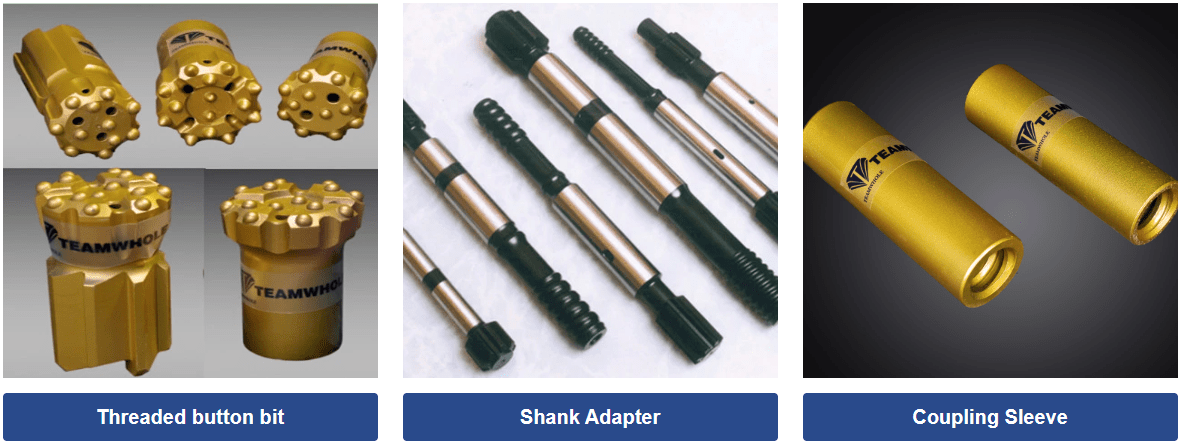
When it comes to down the hole well drilling, understanding depth and pressure considerations is crucial for successful operations. The right balance between drilling depth and pressure ensures efficient penetration into different rock formations, ultimately leading to productive well drilling.
Depth and Pressure Considerations
In down the hole well drilling, achieving the right depth is essential for reaching the desired water or mineral reservoirs. Different geological formations require varying depths, and understanding these variations is key to successful drilling operations. Additionally, maintaining optimal pressure during drilling ensures effective rock penetration without causing damage to the drill bit or compromising the integrity of the well.
Monitoring and Adjusting Drilling Parameters
Monitoring and adjusting drilling parameters in real-time is vital for maintaining efficiency and precision in well drilling operations. By closely monitoring factors such as rotation speed, air pressure, and penetration rate, drill operators can make necessary adjustments to optimize performance and ensure smooth progress throughout the drilling process.
Utilizing Advanced Drilling Technologies
In today's rapidly evolving technological landscape, advanced drilling technologies have revolutionized down the hole well drilling. From pneumatic drills with enhanced power capabilities to sophisticated rock drill designs that offer superior performance in challenging geological conditions, leveraging these advanced tools can significantly improve overall efficiency and productivity in well drilling projects.
By incorporating advanced techniques like real-time monitoring of parameters and modern equipment like pneumatic drills, operators can ensure that their down the hole well drilling projects are executed with precision and efficiency.
Ensuring Successful Results
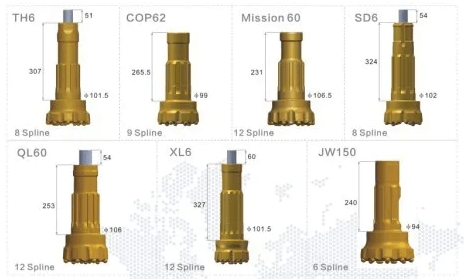
When it comes to down-the-hole well drilling, quality control and assurance are crucial for successful results. Regular inspections of the drill bit, well drilling equipment, and rock drill are essential to maintaining efficiency and precision in drilling operations. By implementing strict quality control measures, you can minimize downtime and maximize productivity on site.
Quality Control and Assurance
Quality control and assurance play vital roles in down-the-hole well drilling operations. They involve rigorous testing of pneumatic drill hammers, drill bits, and other equipment to ensure they meet industry standards. By conducting thorough quality checks at every stage of the drilling process, you can guarantee the reliability and performance of your equipment, ultimately leading to successful well drilling outcomes.
Post-Drilling Evaluation and Analysis
After completing a well drilling project, it's important to conduct a comprehensive post-drilling evaluation and analysis. This involves examining core samples, analyzing geological data, and assessing the drilling operation's overall success. By carefully evaluating the results, you can identify areas for improvement and make necessary adjustments for future projects.
Achieving Efficiency and Precision in Drilling Operations
Efficiency and precision are key factors in achieving successful results in down-the-hole well drilling. Advanced technologies such as real-time monitoring systems can help optimize drilling parameters, ensuring accurate depth control and pressure management. By embracing innovative techniques and tools, you can enhance operational efficiency while maintaining high levels of precision throughout the entire drilling process.
Tianhe: Your Partner for Quality Drilling Solutions
Down the hole well drilling is a complex process that requires careful planning and the right equipment. With the help of Tianhe, you can optimize your drilling efficiency and achieve successful results. By embracing best practices and utilizing quality drilling solutions, you can ensure that your well drilling operations are efficient and precise.
Optimizing Down the Hole Well Drilling Efficiency
To optimize down-the-hole well drilling efficiency, it's crucial to select the right equipment, such as drill bits, rock drills, and pneumatic drills, suitable for your specific drilling needs. Proper maintenance and care of your equipment will also contribute to overall efficiency, ensuring it performs at its best for longer periods.
Tianhe is your trusted partner in providing quality drilling solutions for down the hole well drilling operations. With a wide range of DTH hammer bits and advanced drilling technologies, they offer reliable equipment that meets industry standards and ensures successful results in well drill projects.
Embracing Best Practices for Successful Results
By embracing best practices such as conducting geotechnical surveys, carefully planning site selection, implementing safety measures, monitoring and adjusting drilling parameters, and conducting post-drilling evaluations, you can achieve successful results in your well drilling operations. With Tianhe as your partner, you can rest assured that you have access to the expertise and tools needed to achieve efficient and precise drilling results.