Introduction
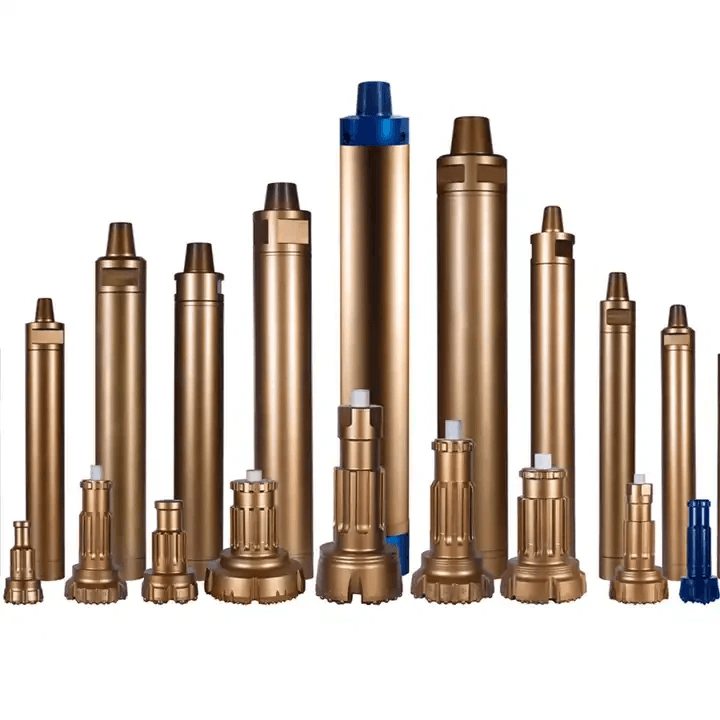
The right drill rig bit can make all the difference when drilling. Understanding the importance of these tools is crucial for successful projects, from exploring different kinds of drill bits to choosing the best one for efficient drilling.
Understanding the Importance of the Right Drill Rig Bit
Selecting the right drill bit is crucial for any drilling project, from construction to oil and gas exploration. Here's a breakdown of key factors to consider:
- Material: Drill bits come in various materials, each suited to specific applications. Steel is standard for general-purpose drilling, while tungsten carbide offers enhanced durability for more rigid materials. Diamond provides the ultimate strength for the most complex substances.
- Design: Different bit designs cater to various needs. Twist drill bits are versatile for general drilling, while spade bits excel at creating large holes in wood. Specialty bits like brad point bits ensure clean cuts in wood, and masonry bits tackle concrete and brick.
- Size and Compatibility: Choose a drill bit with the appropriate diameter to match your desired hole size. Ensure your drilling equipment is compatible with shank types like SDS or standard hex shanks.
Understanding these factors and selecting the right drill bit for the job can help you achieve optimal drilling performance, efficiency, and accuracy.
Exploring the Range of Drill Bit Options
The world of drills and drill bits offers a wide array of options. From long drill bits to specialized designs, countless variations are available to cater to different drilling needs and rock formations.
The variety of drill bit options available can be overwhelming, but understanding the specific needs of your drilling project is critical to choosing the best drill bit for efficient drilling. For example, a diamond-tipped drill bit may be the most effective choice if you are working with rugged rock formations. On the other hand, if you are drilling through softer materials, a carbide-tipped drill bit might be more suitable. By considering the specific requirements of your project, you can narrow down the options and select the most efficient drill bit for the job.
Choosing the Best Drill Bit for Efficient Drilling
Selecting the ideal kind of drill bits ensures efficiency in drilling operations. By carefully considering factors such as material composition, head face design, and carbide shape options, you can find a bit that maximizes performance while minimizing downtime.
Once you have considered the material composition, head face design, and carbide shape options, it's important to also consider the drill bit's coating. Coatings such as titanium nitride or black oxide can enhance the bit's durability and performance, especially when drilling into hard materials like metal or concrete. Choosing a bit with the right coating can significantly extend its lifespan and reduce the frequency of bit changes during drilling operations.
Teamwhole DTH Bit Range
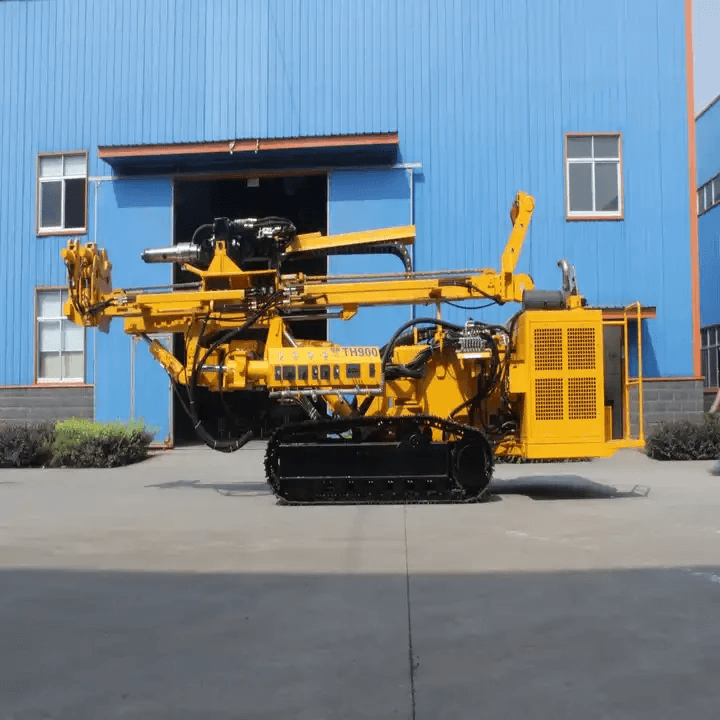
Teamwhole offers diverse DTH bit sizes to cater to various drilling needs. Whether it's small-scale projects or large-scale industrial drilling, drill bits are available in different sizes to ensure compatibility with varying rigs of drill and rock formations.
Diverse Range of DTH Bit Sizes
The Teamwhole DTH bit range includes sizes 3, 4, 5, 6, and custom sizes to fit specific project requirements. This extensive range ensures that there's always a suitable drill bit for any drilling task, from exploration and mining to construction and water well drilling.
In addition to offering a diverse range of DTH bit sizes, Teamwhole ensures that each drill bit is made from high-quality alloy steel. This material is known for its durability and strength, making the drill bits suitable for even the most demanding drilling tasks. With this level of quality, customers can have confidence in the performance and longevity of their DTH drill bits, regardless of the size or type needed for their project.
High-Quality Alloy Steel Material
All Teamwhole DTH bits are manufactured using high-quality alloy steel, ensuring durability and longevity even in the most challenging drilling conditions. This premium material provides exceptional strength, resistance to wear, and the ability to withstand high-impact forces during drilling operations.
In addition to its exceptional strength and resistance to wear, the high-quality alloy steel used in Teamwhole DTH bits also offers excellent heat dissipation properties. This advanced heat treatment ensures extreme protection against overheating during prolonged drilling operations, reducing the risk of premature wear and tear. As a result, our DTH bits can maintain their high performance and reliability even in the most demanding drilling conditions.
Advanced Heat-Treatment for Extreme Protection
To further enhance the durability and performance of their DTH bits, Teamwhole employs advanced heat-treatment processes that harden the steel, providing extreme protection against abrasion and extending the lifespan of the drill bits. This ensures that the drill bits maintain their cutting effectiveness over prolonged periods of use.
In addition to the advanced heat-treatment processes, Teamwhole also utilizes state-of-the-art design and engineering techniques to optimize the performance of their DTH bits. By carefully crafting the geometry and composition of the drill bits, they can maximize drilling efficiency and minimize wear and tear. This attention to detail sets Teamwhole apart, ensuring their products deliver exceptional results in even the most challenging drilling conditions.
Variety of Bit Head Face Designs
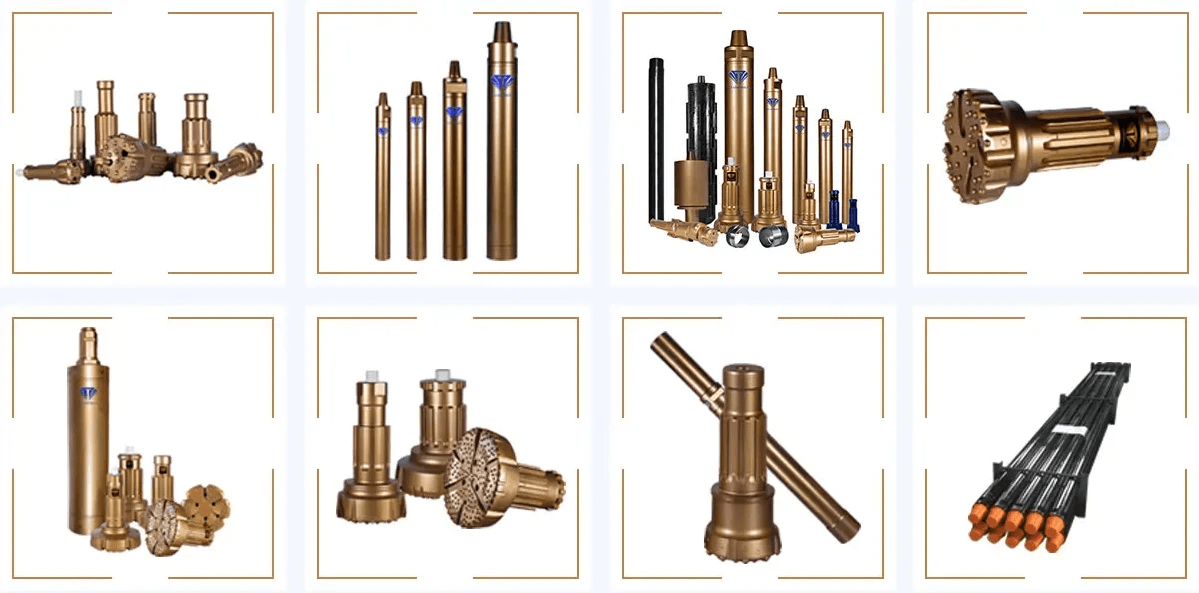
When it comes to drills and bits, the variety of bit head face designs is crucial for achieving optimal drilling performance. From flat to concave, convex, and drop-center options, each design has a unique impact on drilling performance. Flat designs are ideal for soft rock formations, while convex designs are best suited for hard and abrasive formations. Matching the design to the specific rock formations ensures efficient drilling and maximum productivity.
Flat, Concave, Convex, and Drop Center Options
The drill bits come in diverse head-face designs, including flat, concave, convex, and drop center options. Each design serves a specific purpose in addressing different rock formations and drilling challenges. The flat design provides stability in softer formations, while the concave design enhances cutting action in more complex formations. The convex design offers excellent penetration in abrasive rock types, and the drop center option is effective for straighter holes.
Impact on Drilling Performance
The design of a drill bit's head-face plays a critical role in drilling performance. Selecting the right head-face for the job can significantly improve efficiency and save costs. Here's a breakdown of how different head-face designs impact drilling:
- Flat Face: Ideal for soft rock formations where crushing is the primary function.
- Concave Face: Offers reasonable penetration rates in medium-hard rock by creating a concentrated cutting force.
- Convex Face: Best suited for self-cleaning in soft to medium-hard formations with sticky clays.
- Cruciform Face: Designed to break through rigid rock formations by creating a chiseling effect.
By understanding these different designs and their applications, you can make informed decisions when selecting the most suitable drill bit for your project, ultimately improving drilling performance and reducing costs.
Matching Design to Rock Formations
Matching the head face design to specific rock formations is essential for achieving optimal results during drilling operations. Different formations require cutting actions and penetration capabilities only provided by particular bit designs. Considering factors such as hardness, abrasiveness, and structure of the rock formations makes it possible to select a drill bit with a head-face design that matches the project's requirements.
Carbide Shape Options
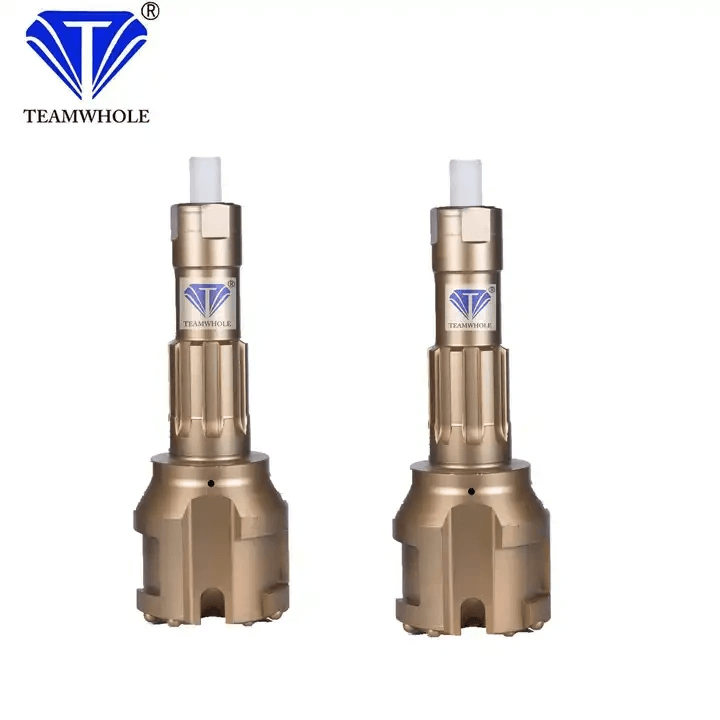
When it comes to drill and bits, the carbide shape plays a crucial role in determining the durability and performance of the drill rig bit. Spherical carbide shapes are ideal for softer rock formations, providing excellent impact resistance and wear characteristics. On the other hand, ballistic carbide shapes are designed for more complex rock challenges, offering superior penetration rates and extended bit life.
Spherical and Ballistic Carbide Shapes
Spherical carbide shapes feature a rounded design that distributes impact evenly, reducing stress on individual carbides and enhancing overall durability. These shapes are perfect for drill bits for projects involving less abrasive rock formations, providing consistent performance and longevity.
Spherical carbide shapes are also known for their ability to maintain a sharp cutting edge for a more extended period, resulting in reduced downtime for bit maintenance and sharpening. This means that drill projects can be completed more efficiently, saving time and money. Additionally, the rounded design of spherical carbide shapes allows smoother drilling operations, minimizing vibration and reducing the risk of bit damage.
Impact on Bit Durability
The choice between spherical and ballistic carbide shapes significantly impacts the overall durability of long bits for drill applications. The right shape ensures that the bit can withstand the harsh conditions of drilling operations, minimizing wear and tear while maximizing efficiency. Spherical carbide shapes are ideal for softer rock formations, providing better impact resistance and reducing the risk of breakage. On the other hand, ballistic carbide shapes are better suited for harder rock challenges, offering improved penetration rates and overall performance in demanding drilling environments.
Tackling Different Rock Challenges
Different rock formations present unique challenges, requiring specific carbide shapes to tackle them effectively. Whether it's limestone, granite, or sandstone, selecting the appropriate shape based on the rock's hardness is crucial for achieving optimal drilling results.
Advantages of Long Drill Bits
When tackling drilling projects, long drill bits can be a game-changer. Here's how their extended length offers several advantages:
- Deeper Drilling: Long drill bits can reach depths that standard bits simply can't. This is crucial for drilling through thick beams, concrete slabs, or deep wall cavities.
- Difficult Access: For tight spaces or oddly angled areas, a long drill bit offers access that a shorter bit wouldn't. This eliminates the need to disassemble obstacles or contort yourself into awkward positions.
- Reduced Repositioning: Since they can drill further in one go, long drill bits save time and effort by minimizing the need to reposition yourself or the material you're drilling into constantly.
Long drill bits are valuable additions to any toolbox. They offer extended reach for deeper drilling and improved access in challenging situations.
Benefits of Using Longer Bits
Using longer drill bits increases flexibility and maneuverability when navigating complex drilling environments. This increases precision and control, resulting in more accurate and efficient drilling. Longer bits also minimize the risk of deviation or deflection, ensuring straighter boreholes and higher-quality results.
Using longer drill bits also reduces the need for frequent bit changes, saving time and increasing productivity. This is especially beneficial in large-scale drilling operations where efficiency is key. Additionally, longer bits allow for deeper drilling without constantly repositioning the drill, making them ideal for projects that require drilling at various depths. The versatility of longer bits makes them a valuable tool for professional contractors and DIY enthusiasts.
Applications for Long Bits
Long drill bits are well-suited for various applications, including mining, construction, geotechnical exploration, and water well drilling. Their extended reach makes them particularly useful in deep-hole drilling projects where standard-length bits may not be sufficient to reach the desired depth. They are also commonly used to access deep reservoirs in oil and gas exploration.
Efficiency in Deep Drilling Projects
When it comes to deep drilling projects, long bits offer unmatched efficiency by enabling continuous penetration into the earth's subsurface without the need for frequent bit changes or repositioning of the drill rig. This results in significant time savings and increased productivity, making long drill bits essential for tackling challenging drilling tasks.
Customizing Bit Selection
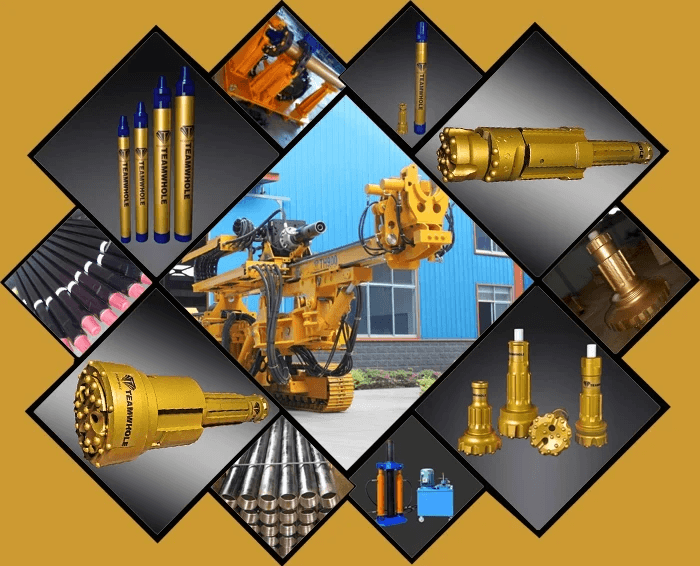
When choosing the right drill rig bit, tailoring the options to specific projects is crucial for achieving optimal results. Different projects call for various kinds of drill bits, and considering factors such as rock formations and drilling depth is essential in selecting the most suitable bit for the job.
Tailoring Bit Options to Specific Projects
Drilling projects vary significantly regarding geological conditions, rock hardness, and depth. Therefore, it's essential to carefully assess each project's specific requirements and select drill bits best suited for the task at hand. Tailoring bit options to particular projects can ensure efficient drilling operations and high-quality results.
Consulting with Experts for Recommendations
Choosing the right drill rig bit is crucial for a successful drilling project. Consulting with experts in the field can provide invaluable guidance. Here's what they can offer:
- Informed Recommendations: Experts know deeply about rock formations, drilling techniques, and equipment capabilities. They can analyze your project's specifics and recommend the optimal drill bit for the job.
- Maximized Efficiency: In addition to recommendations, experts can share insights into the latest drilling technology. This knowledge can help you streamline your operations and achieve better results.
- Precision and Productivity: Their expertise can ensure your drilling project is completed with the highest precision and productivity.
By consulting with drilling and bit experts, you can leverage their experience to make informed decisions and achieve optimal performance in your project.
Maximizing Efficiency and Results
You can maximize efficiency and achieve superior drilling results by customizing bit selection based on project requirements and seeking advice from industry experts. The right combination of long bits for drill applications and other kinds of drill bits tailored to specific projects can lead to enhanced productivity and cost-effectiveness in drilling operations. Additionally, utilizing advanced technologies such as diamond-coated or polycrystalline diamond compact (PDC) bits can improve drilling performance, providing a longer lifespan and increased durability in challenging drilling conditions. Moreover, investing in high-quality bits from reputable manufacturers can ensure reliability and consistency in achieving optimal results, reducing the risk of downtime and costly equipment maintenance.
Achieve Efficiency and Quality Results
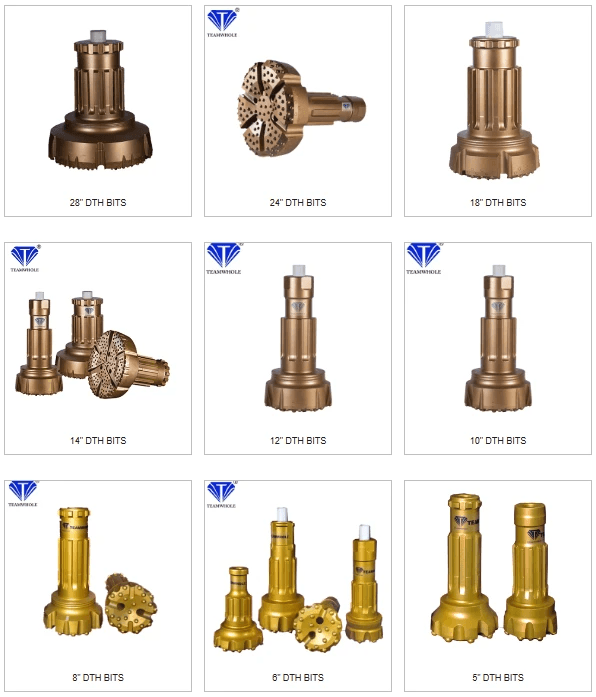
When selecting the ideal drill bit for your project, it's crucial to consider the specific requirements of your drilling operation. With a diverse range of drills and bits available, it's important to weigh the pros and cons of each type to ensure maximum efficiency and results.
Selecting the Ideal Drill Bit for Your Project
Choosing the right drill rig bit is essential for achieving optimal drilling performance. By understanding the various kinds of drill bits available and their suitability for different rock formations, you can make an informed decision that aligns with your project's requirements.
Optimizing Performance with the Right Drill Bit
Optimizing performance with the correct drill and drill bits involves considering factors such as carbide shape options, bit head face designs, and long bits for the drill. You can enhance overall performance and productivity by selecting a high-quality, durable bit that matches your specific drilling needs.
Ultimately, by carefully selecting long drill bits tailored to your project's demands, you can achieve both efficiency and quality results. Customizing bit selection based on rock formations and consulting with experts will lead to successful drilling operations with minimal downtime.