Introduction
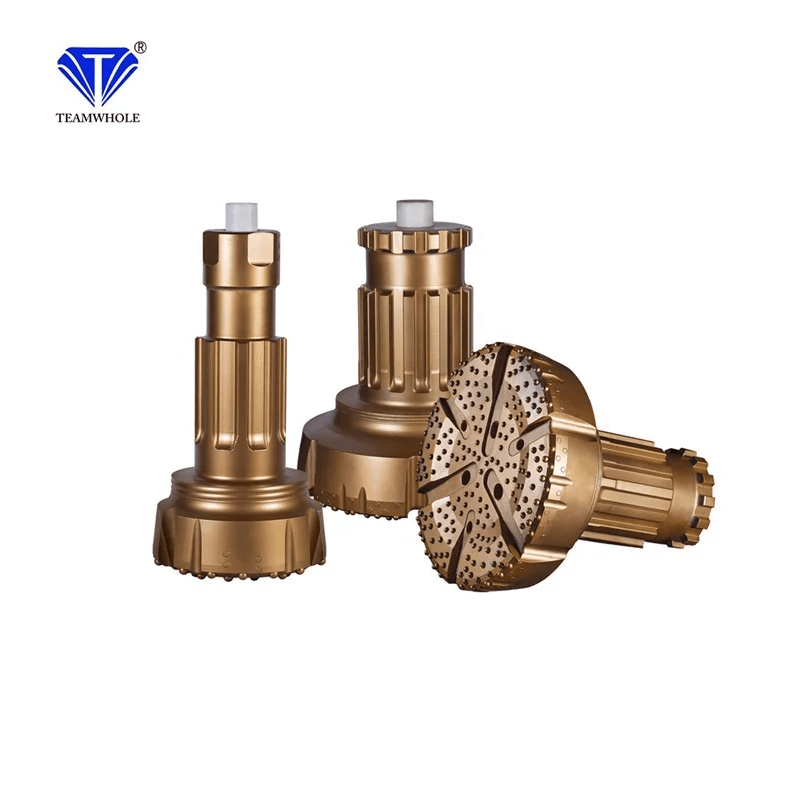
When drilling through rock, choosing the right drill bit is crucial for a successful project. Understanding different types of drill bits is essential with various rock formations and hardness levels. Exploring the best drill bits for rock can help ensure efficiency and safety in your drilling operations.
Different Types of Drill Bits
Choosing the right drill bit is essential for efficient and successful rock drilling. Here are some of the common types of drill bits used for rock formations:
- PDC (Polycrystalline Diamond Compact) Bits: PDC bits are a popular choice in oil and gas drilling due to their exceptional durability and ability to handle tough rock formations.
- Tricone Drill Bits: Versatile and suitable for various rock types, tricone bits are a reliable option for various drilling projects.
- Diamond Drill Bits: Diamond drill bits can cut through extremely hard materials, making them ideal for tasks involving dense rock formations.
By understanding the unique features and applications of each type of drill bit, you can select the most appropriate tool for your specific rock drilling needs.
Exploring the Best Drill Bits for Rock
Selecting the best drill bit for rock involves considering hardness, abrasiveness, and overall durability. PDC drill bits are known for their efficiency in rock drilling, while tricone and diamond options offer versatility and strength in handling challenging rock formations.
When drilling through rock, the right drill bit can make all the difference. PDC drill bits are particularly effective in hard rock formations, thanks to their ability to maintain sharpness and withstand high levels of abrasion. On the other hand, tricone and diamond options offer versatility, making them suitable for a wide range of rock types and formations. By understanding the specific characteristics of the rock you'll be drilling into, you can choose a drill bit that will deliver optimal performance and durability.
Importance of Choosing the Right Drill Bit
Selecting the proper drill bit is crucial for successful rock drilling. Using the wrong one can lead to:
- Inefficiency: Difficulty drilling the desired depth or size hole.
- Increased wear and tear: Damaging the drill bit and potentially the drilling equipment.
- Safety hazards: Broken or dull bits can cause the drill to malfunction and injure users.
Therefore, understanding different drill bit types is essential. Let's explore the various options and how they cater to specific drilling needs in rock formations.
What is a Drill Bit?
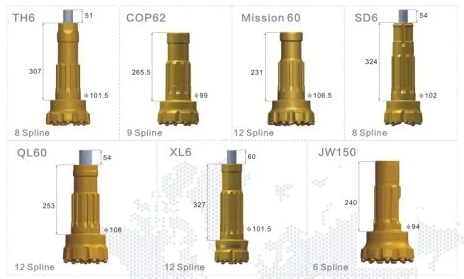
Drill bits are cutting tools that create cylindrical holes in various materials, including rock. Their primary function is to remove material as the bit rotates, allowing for the insertion of screws, bolts, or other fasteners. These bits are available in various sizes and shapes to accommodate different drilling needs.
Definition and Function of a Drill Bit
A drill bit is a tool attachment that fits into the chuck of a drill and is used for drilling holes in various materials. When it comes to rock drilling, the drill bit's primary function is to crush or chip away at the rock surface as it rotates, creating an opening for further excavation or exploration.
A drill bit is a tool attachment that fits into the chuck of a drill and is used for drilling holes in various materials. When it comes to rock drilling, the drill bit's primary function is to crush or chip away at the rock surface as it rotates, creating an opening for further excavation or exploration. The design and materials used in constructing a drill bit are crucial to its performance and durability. Common materials used in drill bit construction include high-speed steel, cobalt steel, carbide, and diamond-tipped bits.
Common Materials Used in Drill Bit Construction
Drill bits are typically made from high-speed steel (HSS), cobalt steel, or carbide. Due to their hardness and resistance to wear, carbide-tipped drill bits are commonly used for rock drilling applications. These bits are designed to withstand the tough conditions when drilling through hard rock formations.
Drill bits made from high-speed steel (HSS) are known for their ability to withstand high temperatures during drilling, making them suitable for various materials, including wood, plastic, and soft metals. On the other hand, cobalt steel drill bits are ideal for drilling through tough materials such as stainless steel and cast iron due to their higher heat resistance and hardness. Carbide drill bits, on the other hand, are best suited for applications involving hard rock formations due to their exceptional hardness and resistance to wear.
Factors to Consider When Selecting a Drill Bit
Selecting the right drill bit is crucial for efficient and successful rock drilling. Here are several key factors to consider:
- Material: The type of rock you're drilling into is paramount. Different rocks have varying degrees of hardness and require specific drill bit materials, like tungsten carbide for tough granite or high-speed steel for softer sandstone.
- Hole Size: The desired diameter of your hole dictates the drill bit size. Ensure the bit's diameter matches your needs for clean and accurate drilling.
- Drill Type: Different drill types, like rotary hammers or core drills, require compatible bit shanks and designs. Choosing a bit that fits your specific drill ensures proper function and safety.
- Drilling Depth: Deeper drilling depths often necessitate more robust and durable drill bits. Consider factors like increased pressure and potential heat generation when selecting a bit for deep drilling projects.
- Environmental Conditions: The environment where you'll be drilling can significantly impact the drill bit's performance and lifespan. Factors like extreme temperatures, moisture, or corrosive substances can necessitate special bit coatings or materials for optimal performance and longevity.
By carefully considering these factors, you can choose the most appropriate drill bit for your specific rock drilling project, ensuring efficient, safe, and successful operation.
Rock Drill Bit Types
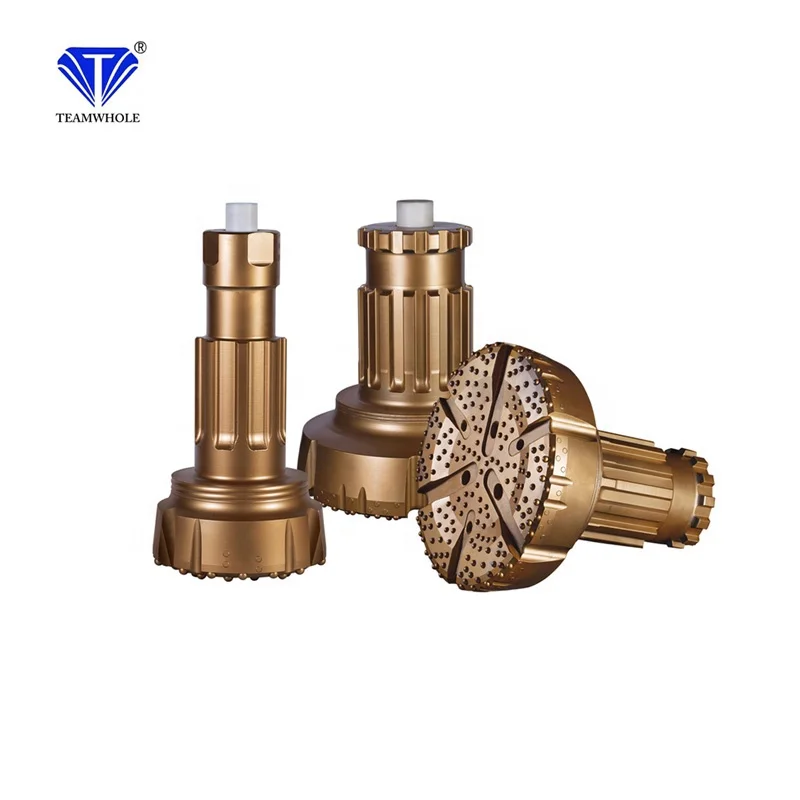
When drilling through rock, choosing the right drill bit is crucial. There are several types of rock drill bits designed for different rock formations and drilling needs.
1. PDC Drill Bits for Efficient Rock Drilling
PDC (Polycrystalline Diamond Compact) drill bits are known for their efficiency in drilling through various rock formations. They feature a diamond-enhanced cutting structure that provides excellent durability and performance, making them ideal for challenging rock drilling projects.
PDC drill bits are also known for their ability to maintain a consistent drilling speed, resulting in faster and more efficient rock penetration. This makes them a top choice for projects where time is of the essence, such as in the oil and gas industry or construction projects with tight deadlines. Additionally, the diamond-enhanced cutting structure of PDC drill bits reduces the need for frequent bit changes, saving operators both time and money.
2. Tricone Drill Bits for Versatile Rock Drilling
Tricone drill bits are popular for their versatility in handling different rocks. The three cone-shaped rollers that rotate independently allow them to effectively drill through soft, medium, and hard formations, making them a reliable choice for various rock drilling applications.
Tricone drill bits are also known for their durability and long lifespan, making them a cost-effective choice for drilling operations. Their ability to handle different types of rocks means that operators don't have to switch out bits, saving time and increasing efficiency constantly. Additionally, tricone drill bits are designed to minimize vibration during drilling, reducing wear and tear on the equipment and ultimately lowering maintenance costs.
3. Diamond Drill Bits for Hard Rock Drilling
Diamond drill bits are designed to tackle hard rock formations precisely and easily. They feature industrial-grade diamonds embedded in the bit's cutting surface, allowing them to maintain sharpness and durability while drilling through tough materials.
Remember that each type of rock drill bit has its advantages and limitations, so it's essential to consider factors such as the hardness of the rock, the desired drilling speed, and the overall project requirements when selecting the most suitable option.
Stay tuned as we delve deeper into the techniques and challenges of drilling into rock formations in the next section!
Drilling Into Rock
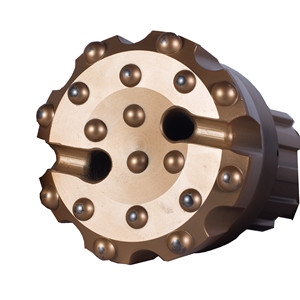
Choosing the right drill bit is crucial for success when drilling into rock. Different rock formations require different drill bits, so factors such as hardness and abrasiveness should be considered. Additionally, the technique used for drilling into rock can greatly impact the efficiency and safety of the process.
Techniques for Successful Rock Drilling
Successful rock drilling relies on effective techniques to create holes in various rock formations efficiently. Here are two common methods used:
- Rotary drilling: This method utilizes a rotating drill bit to create a hole in the rock. Its versatility and ability to penetrate diverse rock types make it popular in mining and construction applications.
- Percussion drilling: This technique employs a hammering motion to break through hard rock surfaces. It's particularly effective for tough rock formations that are difficult to penetrate with other methods.
Rock drilling can be completed safely and efficiently by choosing the right technique and following proper procedures.
Challenges of Drilling Through Different Rock Formations
Drilling through different rock formations presents unique challenges, as each type of rock has its own properties that affect the drilling process. For example, drilling through granite requires a drill bit with strong abrasion resistance, while limestone may require a bit with high-impact strength. Understanding these challenges is essential for selecting the right drill bit.
Tips for Enhancing Efficiency and Safety
Here are some key tips to ensure efficient and safe drilling operations when working with rock:
- Proper Lubrication and Cooling: Utilizing proper lubrication and cooling techniques is crucial to prevent the drill bit from overheating. This can significantly extend the life of the bit and improve drilling efficiency.
- Maintaining Steady Pressure and Speed: Applying consistent pressure and maintaining a steady drilling speed helps minimize unnecessary wear and tear on the equipment, leading to smoother and more efficient operations.
- Regular Inspections and Maintenance: Inspecting and maintaining drill bits are essential for safety and efficiency. This allows for identifying and timely replacing worn-out or damaged bits, preventing potential accidents and ensuring optimal drilling performance.
By following these simple tips, you can significantly enhance the efficiency and safety of your rock drilling operations.
Mining Drill Bit
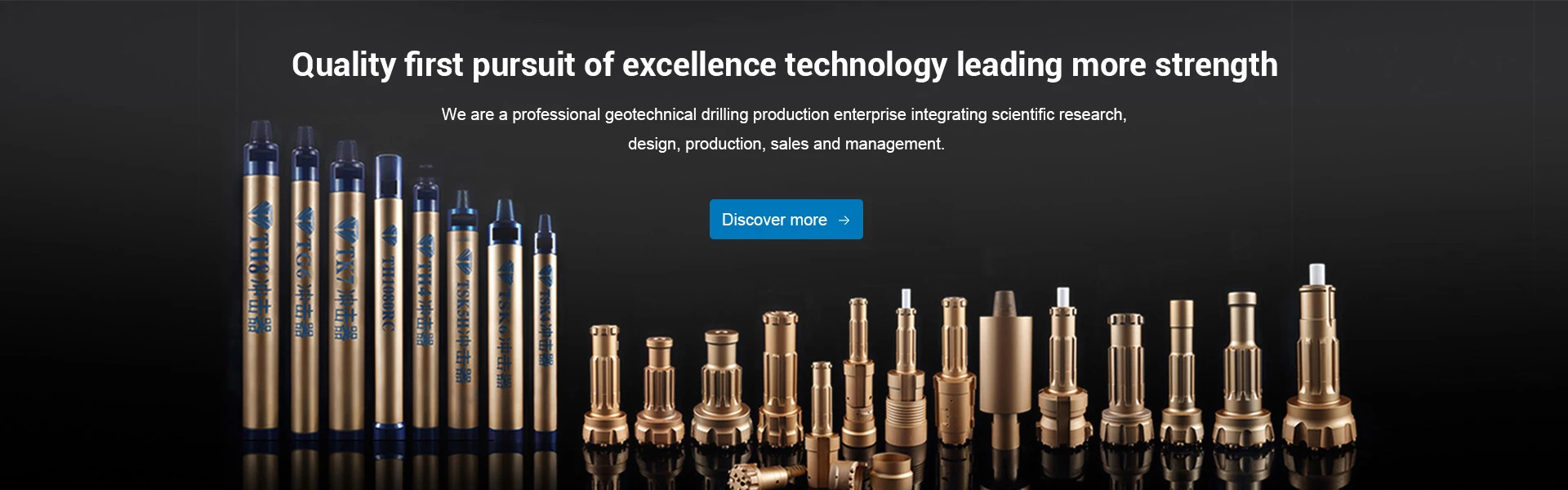
Specialized drill bits are essential for efficient and effective rock drilling in mining applications. These drill bits are designed to withstand the tough conditions of mining operations, offering durability and precision in drilling through various rock formations.
Specialized Drill Bits for Mining Applications
When selecting a drill bit for mining applications, it's important to consider factors such as the rock's hardness, depth, and the desired drilling speed. Diamond-tipped bits are ideal for hard rock formations, offering superior durability and cutting performance. Tricone bits, on the other hand, are versatile and can handle a wide range of rock formations, making them a popular choice for general mining applications. PDC (polycrystalline diamond compact) bits are known for their high penetration rate and long lifespan, making them well-suited for demanding drilling conditions.
Features to Look for in a Drill Bit for Mining
Selecting the appropriate drill bit is vital for efficient and successful mining operations. Here are key factors to consider:
- Durability and Wear Resistance: Mining environments are harsh, demanding tools capable of withstanding constant drilling and pressure. Look for bits made from high-grade steel or tungsten carbide to ensure they can withstand the challenge.
- Cutting Efficiency: Drilling speed and hole quality are crucial. Choose bits with sharp, well-designed cutting edges that can penetrate rock formations effectively and minimize chipping or breaking.
- High Impact Strength and Heat Resistance: Mining often involves hammering through tough materials, generating significant heat. Opt for drill bits with excellent impact resistance and the ability to handle high temperatures without losing performance.
- Corrosion Resistance: Drill bits are exposed to various chemicals and minerals during underground operations. Choose options with superior corrosion resistance to prevent premature wear and tear.
- Design Features: Consider the bit's design for improved stability and reduced vibration. Look for features like tapered bodies or unique flute designs that enhance drilling precision and efficiency.
By carefully considering these factors, you can choose the most suitable drill bits for your mining needs, ensuring smooth operations and maximizing productivity.
Overview of Tianhe's High-Quality Mining Drill Bits
Tianhe offers a range of high-quality mining drill bits designed to provide exceptional performance in challenging mining environments. With advanced engineering and cutting-edge technology, Tianhe's drill bits deliver superior durability and efficiency when drilling through tough rock formations.
Remember that choosing the right drill bit is crucial to successful rock drilling in mining applications. By considering your project's specific requirements and selecting a high-quality drill bit that meets those needs, you can ensure efficient and safe drilling operations while maximizing productivity.
Choosing the Right Drill Bit for Your Rock Drilling Project
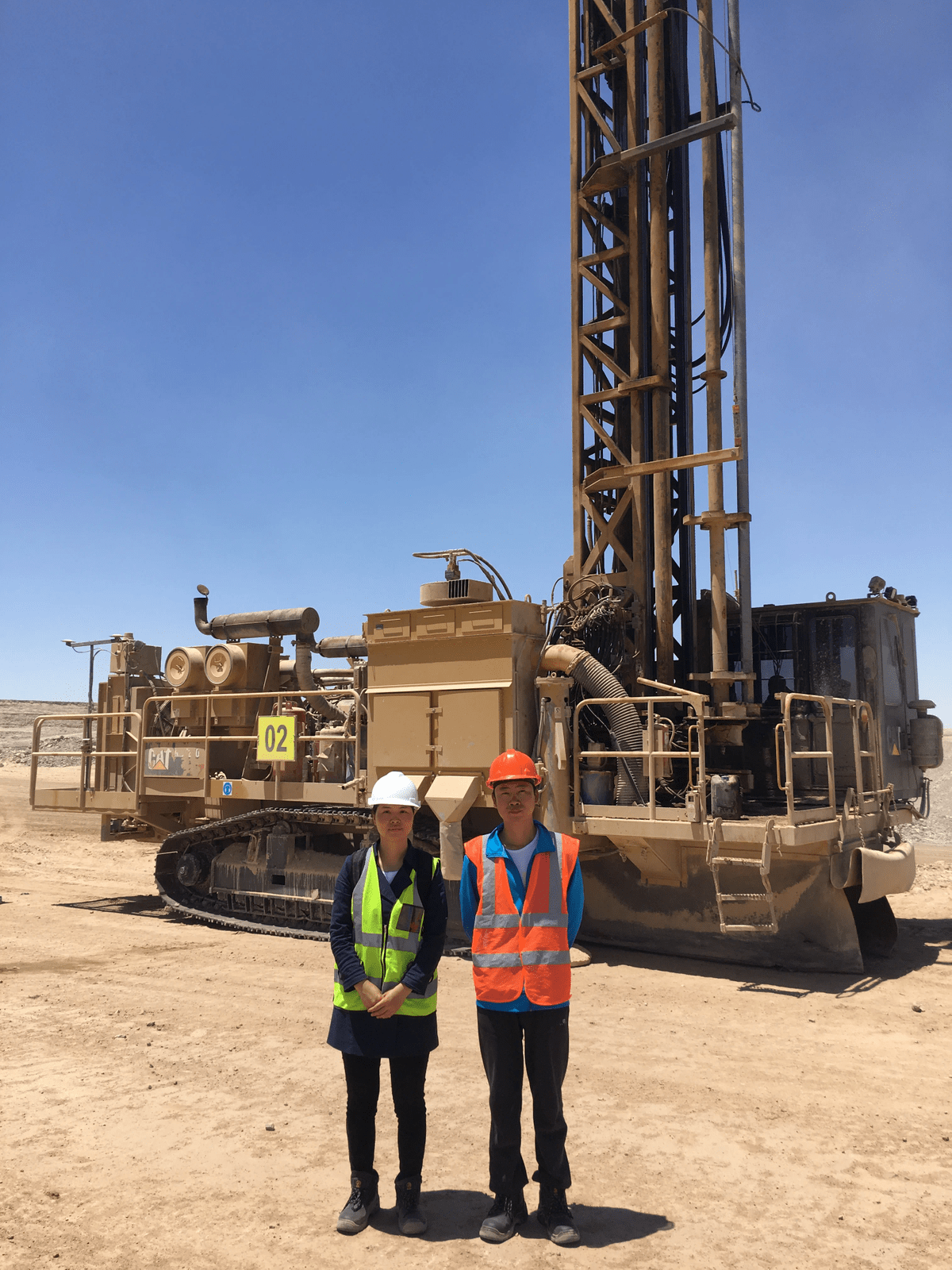
Choosing the right drill bit is crucial for a successful project when drilling through rock. Whether it's PDC, tritone, or diamond drill bits, understanding the rock drill bit types and their applications is essential. Safety and efficiency should always be prioritized when drilling into rock, and keeping up with the latest innovations in rock drill bit technology can lead to improved results.
Selecting the appropriate drill bit for your specific rock drilling project is key to achieving optimal results. Consider factors such as the type of rock formation, drilling depth, and desired speed and efficiency to determine what drill bit to use. Whether it's for mining or construction purposes, choosing the right tool will make a significant difference in your project's success.
Ensuring Safety and Efficiency in Rock Drilling
Drilling into rock poses various challenges that require careful planning and execution to ensure safety and efficiency. It's important to use proper techniques and equipment when drilling through different rock formations. Prioritizing safety measures and implementing efficient drilling practices will contribute to a successful outcome while minimizing risks.
Exploring the Innovations in Rock Drill Bit Technology
Staying updated on the latest advancements in rock drill bit technology can significantly enhance your drilling operations. From improved durability and performance to specialized features designed for specific applications, innovative developments continue to shape the industry. Embracing these innovations can lead to more effective and cost-efficient rock drilling processes.