Introduction
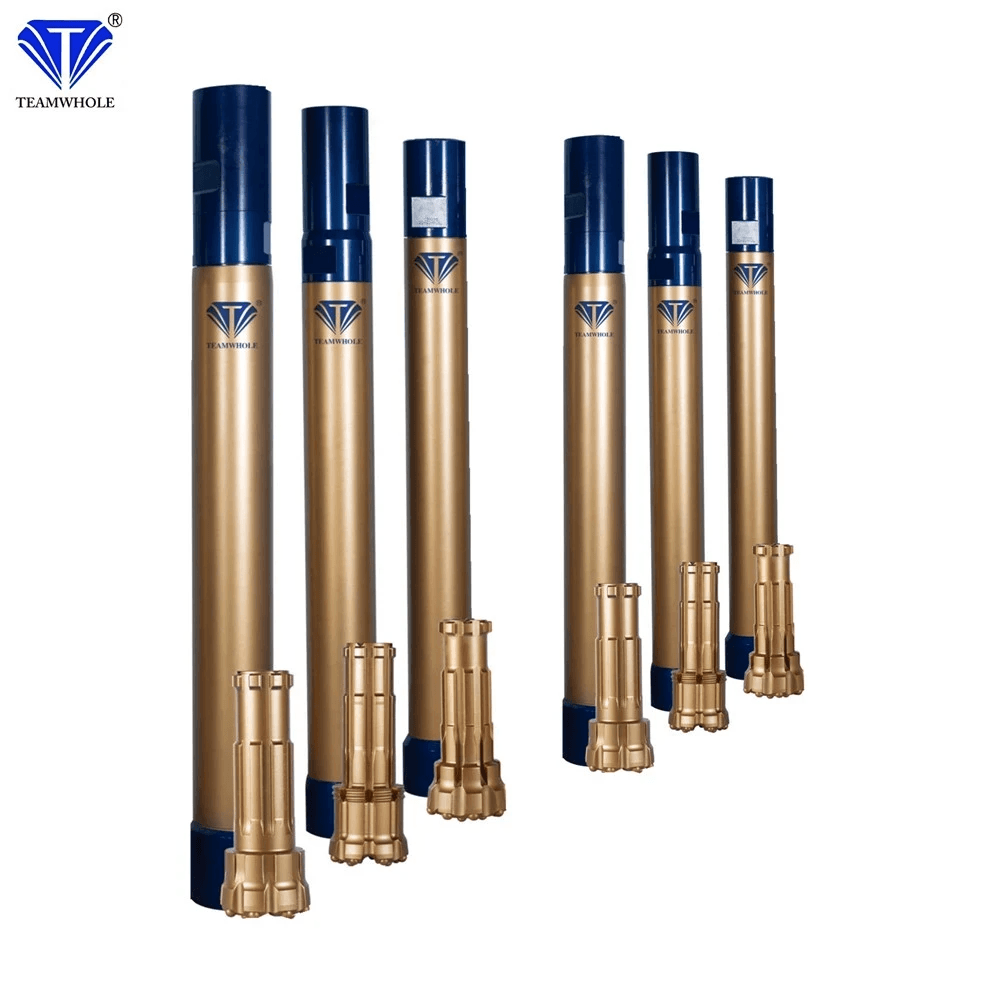
Choosing the right drilling rig bits for drilling operations cannot be overstated. The success of any drilling project hinges on the quality and efficiency of the drill bits used. With so many options on the market, selecting the best drilling rig bits can be daunting. That's where Teamwhole comes in as your go-to source for top-quality drilling rig bits that deliver exceptional performance and durability.
The Importance of Choosing the Right Drilling Rig Bits
Selecting the proper drilling rig bits is crucial for achieving optimal drilling efficiency and productivity. Whether in the oil and gas industry or involved in construction, having the right drill bit can make all the difference in completing your project on time and within budget.
Teamwhole: Your Go-To Source for Quality Drilling Rig Bits
Teamwhole is a leading supplier of high-performance drilling rig bits, including oil well drilling bits, PDC drill bits, and more. Committed to innovation and quality, Teamwhole offers a comprehensive range of drill bit solutions designed to meet the diverse needs of customers across various industries.
Teamwhole's dedication to innovation and quality is evident in their continuous research and development efforts. By staying ahead of industry trends and technological advancements, Teamwhole can offer cutting-edge drilling rig bits that deliver superior performance and durability. This commitment to innovation ensures that customers can rely on Teamwhole for the latest advancements in drilling technology.
Key Factors to Consider When Selecting Drilling Rig Bits
Selecting the right drill bit is crucial for efficient and cost-effective drilling operations. Here are some key factors to consider:
- Formation characteristics: Different rock formations have varying hardness, abrasiveness, and other properties. PDC bits excel in soft formations, while roller cone bits are better suited for hard rock. Choose a bit specifically designed for the formation you'll be drilling through.
- Durability and wear resistance: Drilling puts immense stress on the bit. Consider the material composition and quality to ensure the bit can withstand the drilling conditions without premature failure.
- Cutting structure: The design of the cutting surface significantly impacts performance. PDC bits use industrial diamonds for exceptional wear resistance in soft formations, while roller cone bits use tungsten carbide inserts for hard rock applications.
- Hydraulic design: How the bit channels drilling fluid can affect penetration rate and overall efficiency. Choose a bit with a hydraulic design optimized for your drilling operation.
By carefully considering these factors, you can select the ideal drill bit for your project, maximizing performance and minimizing downtime.
Understanding Different Types of Drilling Rig Bits

PDC Drill Bits: The Cutting Edge of Drilling Technology
Regarding drilling rig bits, PDC (Polycrystalline Diamond Compact) drill bits are at the forefront of cutting-edge technology. These bits feature diamond-enhanced cutting edges that provide superior durability and performance in challenging drilling conditions. PDC drill bits are known for their ability to efficiently drill through hard rock formations, making them a popular choice for oil and gas drilling operations.
PDC drill bits are also prized for their versatility in drilling operations. Their diamond-enhanced cutting edges allow precise and efficient drilling through various formations, from soft to hard rock. This versatility makes PDC drill bits an ideal choice for oil well drilling, where the composition of the rock formations can vary significantly within a single well. Whether shale, limestone, or sandstone, PDC drill bits can handle the job with ease and reliability.
Exploring the Versatility of Oil Well Drilling Bits
Oil well drilling bits come in various types, each designed to meet specific drilling needs. From roller cone bits to fixed cutter bits, oil drilling bits manufacturers offer a range of options to accommodate different geological formations and drilling environments. Understanding the versatility of these drill bit options is crucial for maximizing drilling efficiency and achieving optimal results.
Oil drilling bit manufacturers are constantly innovating to develop new designs and technologies to handle drilling challenges in different terrains. For example, PDC (polycrystalline diamond compact) bits are known for their durability and high penetration rate in hard rock formations, making them ideal for challenging drilling environments. On the other hand, roller cone bits are better suited for softer formations due to their ability to maintain stability and control in these conditions. By understanding the specific characteristics of each type of bit, drillers can make informed decisions about which tool will be most effective for their particular drilling project.
The Role of DTH Hammer Manufacturers in Efficient Drilling
DTH (Down-The-Hole) hammer manufacturers play a critical role in the efficiency and success of drilling operations. DTH hammers are used with drill bits to deliver powerful percussion blows, breaking through rock formations during drilling. Choosing high-quality DTH hammers from reputable manufacturers is essential for ensuring smooth and productive drilling processes.
When selecting drilling rig bits to use in conjunction with DTH hammers, it's important to consider the specific geological conditions of the drilling site. Different rock formations require different types of drill bits, so understanding the composition and density of the rocks being drilled through is crucial for choosing the most effective bits. Additionally, considering the size and depth of the borehole is essential for selecting drill bits that can withstand the necessary force and impact to break through the rock formations effectively.
Factors to Consider When Selecting Drilling Rig Bits
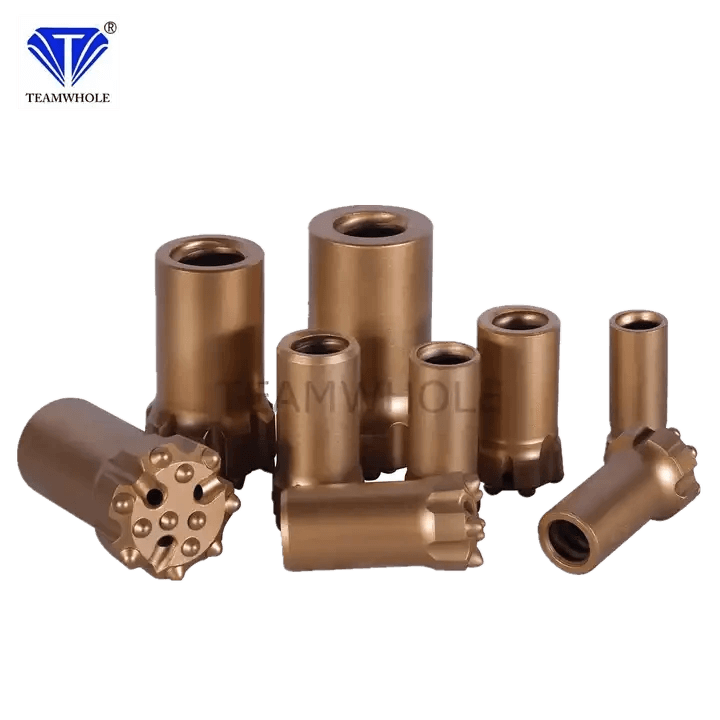
When choosing the right drilling rig bits, durability and wear resistance are crucial factors. Oil drill bits must withstand harsh drilling conditions, so opting for high-quality materials and superior craftsmanship is essential. At Teamwhole, we understand the importance of durability and offer a range of reliable drilling rig bits built to last.
Durability and Wear Resistance of Oil Drill Bits
Our oil well drilling bits are meticulously engineered using advanced materials and cutting-edge technology to ensure exceptional durability and wear resistance. With our commitment to quality, you can trust that our drill bits will hold up under the most demanding drilling conditions, delivering consistent performance and longevity.
Our drill bits have various bit head face designs to maximize drilling efficiency. The right-bit head face design can significantly impact the speed and effectiveness of drilling operations. Our drill bits can achieve maximum efficiency by carefully selecting the appropriate design for specific drilling conditions, reducing downtime, and increasing overall productivity.
Choosing the Right Bit Head Face Design for Maximum Efficiency
The design of the bit head face plays a significant role in determining drilling efficiency. Different formations require specific face designs for optimal performance. At Teamwhole, we offer a variety of bit head face designs tailored to various rock formations, ensuring maximum efficiency and productivity during drilling operations.
When choosing the right bit head face design for maximum efficiency, it's essential to consider the specific rock formations you'll be drilling into. For example, a conical bit head face design is ideal for soft rock formations, while a chisel-shaped face design works best for hard formations. By offering a variety of tailored designs, Teamwhole ensures that drilling operations can achieve maximum efficiency and productivity across a range of geological conditions.
The Importance of High-Quality Alloy Steel in Drilling Rig Bits
High-quality alloy steel is a non-negotiable requirement for manufacturing top-notch drilling rig bits. Here at Teamwhole, we prioritize using premium alloy steel in our products to guarantee the following:
- Superior Strength: Withstand the toughest drilling conditions.
- Unequaled Toughness: Maintain peak performance even when encountering hard rock formations.
- Enhanced Corrosion Resistance: Drill deeper for longer without worrying about wear and tear.
Teamwhole drilling rig bits are built to last, saving you time and money in the long run.
Remember, durability is key! Choose high-quality materials and superior craftsmanship for long-lasting performance. To maximize drilling efficiency, select the right bit head face design for your specific rock formations.
Advancements in Drilling Rig Bit Technology
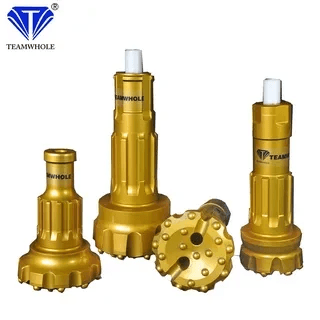
As drilling technology continues evolving, Teamwhole DTH Bits stand out with innovative features that enhance drilling efficiency and performance. With advanced designs and cutting-edge materials, these drilling rig bits are engineered to tackle even the toughest rock formations, making them a top choice for oil drilling operations.
Innovative Features of Teamwhole DTH Bits
Teamwhole DTH Bits deliver superior performance and longevity through several innovative design features:
- Precision-engineered nozzles: Optimize flushing and cooling during drilling, resulting in improved penetration rates and longer bit life.
- Advanced design: Minimizes vibration and resistance, allowing smoother operation and reducing wear on the bit and hammer.
- Advanced heat-treatment processes: Enhance durability and strength, ensuring consistent performance in various drilling conditions.
Teamwhole DTH Bits are a reliable, cost-effective solution that keeps your drilling operations running smoothly.
The Impact of Advanced Heat Treatment on Bit Performance
The heat-treatment process manufacturing Teamwhole DTH Bits enhances their performance and durability. By subjecting the bits to precise heat-treatment methods, their strength and resistance to wear are significantly increased, ensuring consistent performance even in challenging drilling conditions.
By carefully controlling the heat-treatment process, Teamwhole DTH Bits can achieve a uniform and fine-grained microstructure, essential for maximizing strength and wear resistance. This allows the bits to maintain their cutting edge for extended periods, reducing the need for frequent replacements and ultimately lowering drilling costs. The precise heat-treatment methods also contribute to reducing the risk of premature failure, ensuring that the bits can withstand the extreme forces and temperatures encountered during drilling operations.
How Different Carbide Shapes Tackle Various Rock Formations
Teamwhole DTH Bits utilize a range of carbide shapes tailored to specific rock formations, allowing efficient drilling across diverse geological environments. Whether it's hard abrasive formations or softer sedimentary rocks, these carbide shapes are designed to deliver optimal cutting efficiency and longevity.
Teamwhole DTH Bits are designed to tackle various rock formations with precision and efficiency. The carbide shapes are strategically chosen to match the specific characteristics of each type of rock, ensuring that the drilling process is smooth and effective. This attention to detail allows drilling operations to be carried out seamlessly across different geological environments without compromising performance or durability.
By incorporating these innovative features into their DTH bits, Teamwhole continues to set new standards for drilling rig bit technology, providing oil drill bit manufacturers with reliable solutions for maximizing drilling performance while ensuring cost efficiency.
The Future of Efficient Drilling: Choose the Best Drill Bit
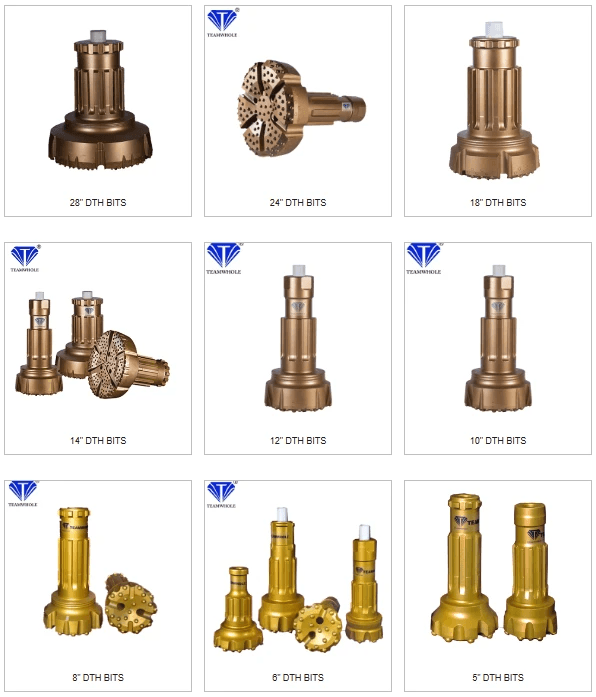
Regarding enhancing drilling efficiency, Teamwhole DTH Bits are the way to go. With their innovative features and advanced heat treatment, these drilling rig bits are designed to maximize performance and durability in various drilling conditions. You can ensure that your future drilling operations will be efficient and successful by choosing the right drilling rig bits, such as PDC drill bits or oil well drilling bits.
Enhancing Drilling Efficiency with Teamwhole DTH Bits
Teamwhole DTH Bits are at the forefront of drilling rig bit technology, offering innovative features that improve drilling efficiency and performance. Their advanced heat-treatment process ensures durability and wear resistance, making them a reliable choice for any drilling operation. With their high-quality alloy steel construction and versatile design options, Teamwhole DTH Bits are the key to enhancing drilling efficiency.
Teamwhole DTH Bits are designed to deliver maximum performance in various drilling conditions, from soft soil to hard rock. Their innovative design features ensure optimal energy transfer, resulting in faster and more efficient drilling. This means less time spent on each borehole and ultimately lower operational costs for drilling projects. With Teamwhole DTH Bits, you can trust that your drilling rig will operate at peak performance, no matter its challenges.
Maximizing Performance with the Right Drilling Rig Bits
Choosing the right drilling rig drill bit is crucial for maximizing performance in any drilling operation. Whether it's PDC drill bits or oil well drilling bits, selecting high-quality products from reputable oil drill bit manufacturers is essential for achieving optimal results. By prioritizing durability, wear resistance, and efficient design features, you can ensure that your drilling rig bits will deliver maximum performance in challenging rock formations. Additionally, considering the specific geological conditions of the drilling site and customizing the drill bit design accordingly can further enhance efficiency and productivity. This tailored approach allows for a more precise and effective drilling process, ultimately improving overall performance.
As technological advancements continue to shape the future of efficient drilling, selecting the best drill bit is more important than ever. With a focus on durability, wear resistance, and innovative design features from top oil drill bits manufacturers like Teamwhole and DTH hammer manufacturers, you can stay ahead of the curve in achieving efficient and successful drilling operations.