Introduction
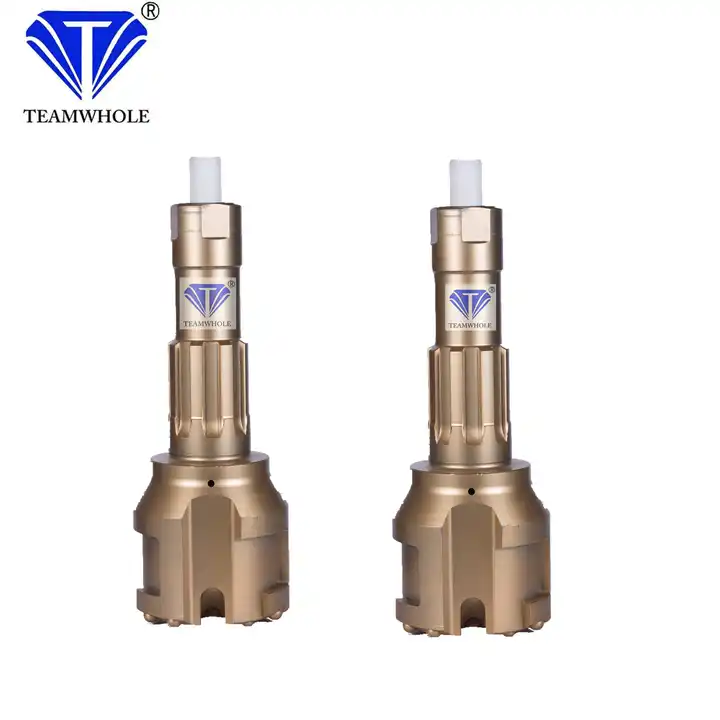
When it comes to down-the-hole drilling, the efficiency of the DTH hammer plays a crucial role in determining the success of a project. Understanding the intricacies of DTH hammer performance is essential for achieving optimal results and minimizing downtime. The benefits of maximizing DTH hammer efficiency are far-reaching, impacting both productivity and cost-effectiveness.
Down-the-Hole Hammer: A Powerhouse of Drilling Efficiency
The Down-The-Hole (DTH) hammer is a remarkable tool used in drilling applications and is known for its efficiency and effectiveness in penetrating hard rock formations. This efficiency comes from the unique design and operating principle of the DTH hammer, which directly impacts the drill bit with high-frequency, high-energy percussive blows, similar to a pneumatic hammer but located at the drill bit end. Here's a closer look at the factors that contribute to the efficiency of the DTH hammer:
1. High Penetration Rate
DTH hammers are capable of achieving high penetration rates, especially in hard rock formations. This is due to the percussive action that breaks the rock directly under the drill bit, as opposed to rotary drilling methods that grind away at the rock. The direct application of energy means less energy is lost, translating to faster drilling speeds.
2. Energy Efficiency
The energy transfer in a DTH hammer is more direct and efficient than in top hammer drilling systems. In top hammer systems, energy must travel through the drill string to reach the bit, losing effectiveness over distance. Because the DTH hammer is located right behind the drill bit, energy loss is minimized, making it particularly effective for deep hole drilling.
3. Reduced Overburden Drilling Costs
DTH drilling can significantly reduce the cost of drilling in overburdened (soft) formations. The efficiency and speed of DTH drilling mean that fewer drill bits and less fuel are used, leading to lower overall project costs.
4. Versatility Across Rock Types
DTH hammers can efficiently drill through a wide range of rock types and hardness levels. Their design allows for adjustments in air pressure and hammer size, making them adaptable to different drilling conditions and requirements. This versatility reduces the need for multiple types of drilling equipment on a project.
5. Longer Drill Bit Life
The design of DTH drills allows for a more consistent application of force to the drill bit, which can result in a longer life for the drill bits compared to other drilling methods. This is because the percussive action minimizes the bit's exposure to excessive heat and wear, common causes of bit failure.
6. Lower Maintenance Costs
DTH hammers have relatively simple designs with fewer moving parts compared to rotary drills, which can lead to lower maintenance costs and downtime. The robustness and simplicity of the design make them more durable and reliable in harsh drilling environments.
7. Capability for Deep Hole Drilling
The efficiency of energy transfer in DTH drilling makes it ideal for deep hole applications. As the hammer operates directly at the bottom of the hole, there is no loss of performance with increased depth, unlike top hammer drills, where performance can significantly decrease as depth increases.
The Importance of DTH Hammer Efficiency
The efficiency of Down-The-Hole (DTH) hammers is of paramount importance in drilling operations across various industries, including mining, construction, water well drilling, and oil and gas exploration. The effectiveness of DTH hammers directly influences the cost, speed, and success of drilling projects. Here are several reasons why DTH hammer efficiency is critical:
1. Cost-Effectiveness
Efficient DTH hammers reduce the cost per meter of drilling. High penetration rates mean faster drilling, which in turn lowers fuel and labor costs. Additionally, efficient hammers that wear down more slowly reduce the need for frequent replacements, further driving down project costs.
2. Increased Productivity
Efficiency translates directly to increased productivity. Faster drilling speeds allow for more holes to be drilled in a shorter amount of time, which is crucial for meeting project deadlines and improving overall project throughput.
3. Energy Efficiency
An efficient DTH hammer utilizes compressed air or hydraulic power more effectively, leading to lower energy consumption. In operations where energy costs can be significant, improving the efficiency of the DTH hammer can have a substantial impact on overall energy expenditure.
4. Environmental Impact
Lower energy consumption not only reduces costs but also diminishes the environmental footprint of drilling operations. Efficient use of power and resources contributes to more sustainable drilling practices, which is increasingly important in industries under pressure to minimize environmental impacts.
5. Operational Flexibility
Efficient DTH hammers are capable of performing well across a range of conditions and rock types. This versatility ensures that drilling operations can proceed smoothly even when faced with unexpected geological formations, thereby minimizing delays and adjustments in the drilling process.
6. Deep Drilling Capability
The efficiency of DTH hammers is particularly important for deep hole drilling projects. Their ability to maintain high penetration rates at greater depths, where top hammer efficiency significantly drops, makes them indispensable for deep drilling applications.
7. Reduced Wear and Tear
Efficient DTH hammer designs are optimized to reduce the wear and tear on both the hammer and the drill bit, extending the lifespan of the drilling equipment. This not only saves money on replacements but also decreases downtime associated with equipment maintenance and replacement.
8. Safety
Efficient and reliable DTH hammer operations contribute to safer drilling environments. By reducing the likelihood of equipment failure and minimizing the need for maintenance and replacements, there's less risk of accidents and injuries associated with equipment handling and breakdowns.
Benefits of Optimal DTH Hammer Performance
Optimal performance from a DTH hammer results in faster penetration rates, improved hole straightness, reduced fuel consumption, and decreased overall drilling costs. These benefits make it essential for achieving successful geotechnical drilling projects.
Furthermore, optimal DTH hammer performance also leads to reduced downtime and maintenance costs, as the equipment operates more efficiently and experiences less wear and tear. This means that drilling operations can continue uninterrupted for longer periods, increasing productivity and project timelines. Additionally, the improved hole straightness achieved with optimal DTH hammer performance reduces the need for costly corrective measures, such as re-drilling or deviation control techniques.
What is DTH Hammer?
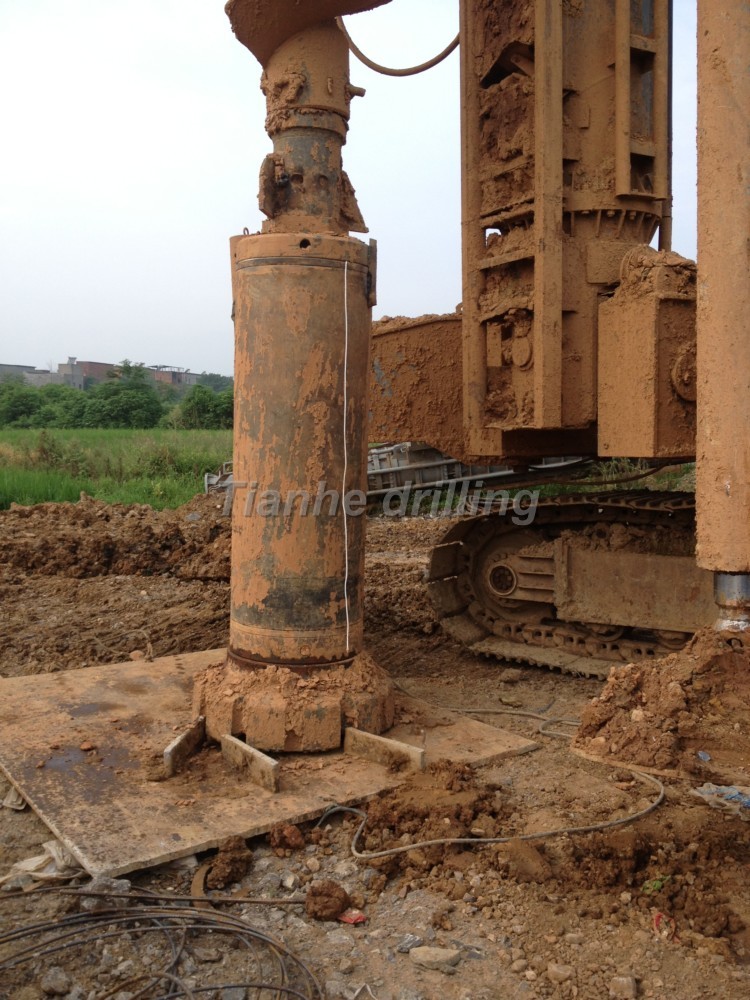
How DTH Hammer Works
A Down the Hole (DTH) hammer is a percussion system that delivers powerful blows to the drill bit, enabling efficient drilling through hard rock formations. The DTH hammer operates by using compressed air to rapidly strike the drill bit, creating boreholes for various applications such as mining, construction, and geotechnical exploration.
The DTH hammer consists of several key components, including the hammer itself, the drill bit, and the drill pipe. The hammer is designed to withstand the high-impact forces generated during drilling, while the drill bit is specially engineered to penetrate hard rock formations effectively. The drill pipe serves as a conduit for compressed air to reach the hammer and provide the necessary power for drilling.
Components of DTH Hammer
The main components of a DTH hammer include:
- hammer body
- piston
- bit sub
- drill bit
The hammer body houses the piston and provides a chamber for the compressed air to drive the piston downwards onto the drill bit. The bit sub connects the drill bit to the rest of the hammer assembly and ensures proper alignment during drilling operations.
The drill bit itself is a crucial component of the DTH hammer, as it is the part that makes contact with the rock or other material being drilled. The design and material of the drill bit can greatly impact drilling efficiency and effectiveness, making it an important consideration in selecting a DTH hammer for a particular application.
Different types of drill bits are available to suit various drilling needs, such as button bits for hard rock drilling or DTH hammer bits for softer formations.
Applications of DTH Hammer
DTH hammers are widely used in down-the-hole drilling operations for water well drilling, geotechnical investigations, mining exploration, and quarrying activities. Their ability to efficiently penetrate hard rock formations makes them indispensable tools in various industries where traditional drilling methods may not be effective.
Tianhe's expertise in manufacturing high-quality DTH hammers and bits has revolutionized down-the-hole drilling practices around the world. With their commitment to research, design, production, sales, and management of geotechnical drilling equipment, Tianhe continues to lead the industry in enhancing drilling efficiency and productivity.
Factors Affecting DTH Hammer Efficiency
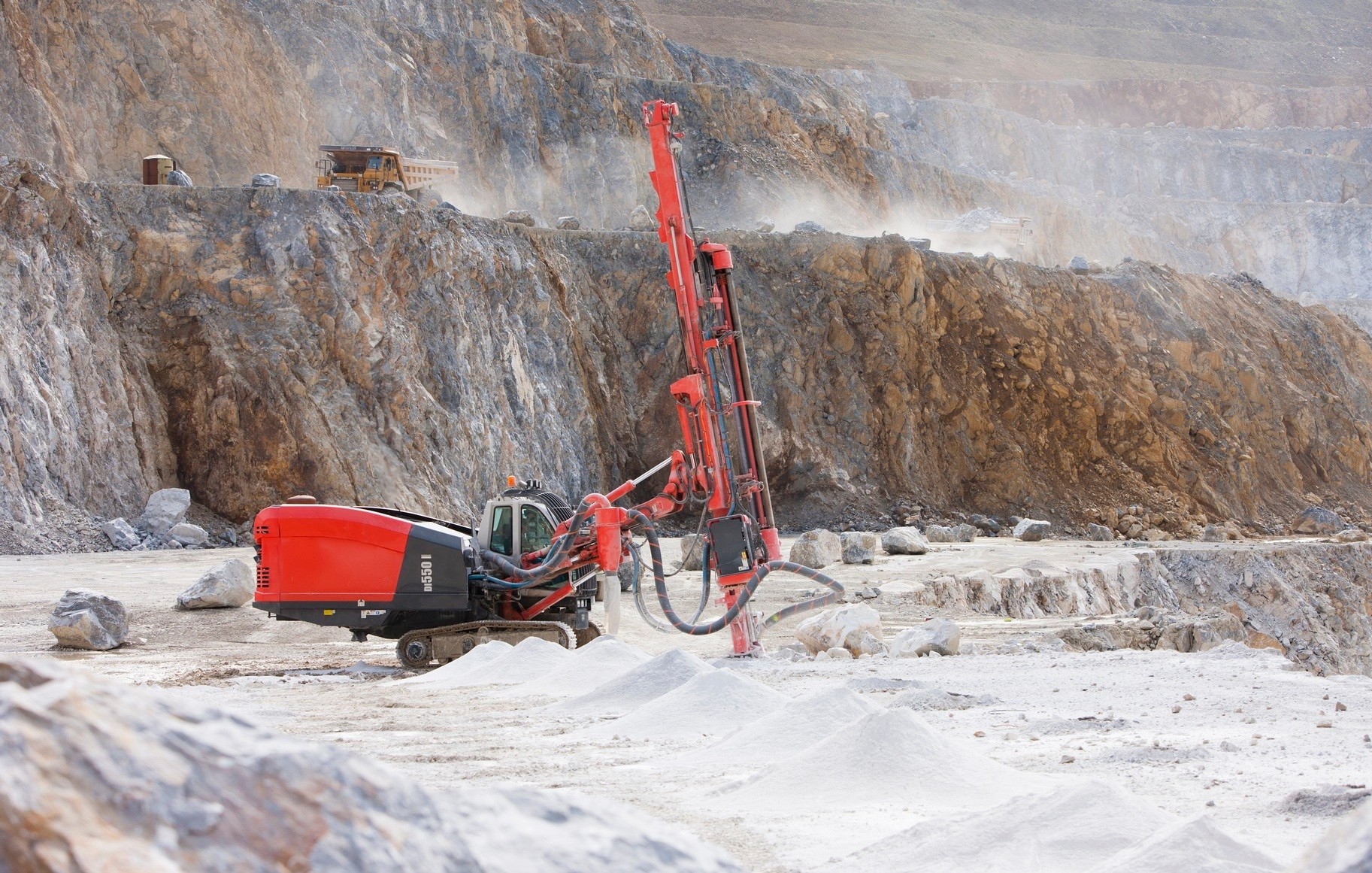
1. Impact of Drill Rig Power
The efficiency of a DTH hammer is greatly impacted by the power of the drill rig it is attached to. A higher-powered rig can provide the necessary force to drive the hammer through tough rock formations, resulting in faster and more effective drilling. It is essential to ensure that the drill rig's power matches the requirements of the DTH hammer being used to maximize efficiency.
In addition to the power of the drill rig, the type and size of the drill bit used also play a crucial role in the efficiency of drilling operations. Choosing the right drill bit for the specific rock formations being encountered can make a significant difference in both speed and effectiveness. A properly selected drill bit will minimize wear and tear on the DTH hammer, reducing maintenance and downtime. It is important to carefully consider the geological conditions and select the appropriate drill bit to maximize drilling efficiency.
2. Proper Drill Bit Selection
Selecting the right drill bit for a DTH hammer is crucial for achieving optimal performance. Different rock formations require different types of bits, and using the wrong bit can lead to decreased drilling efficiency and increased wear on both the bit and the hammer. Proper selection of DTH hammer bits based on geological conditions can significantly improve drilling productivity.
Choosing the right drill bit for a DTH hammer is not just about the type of rock formations but also about the operating parameters. Factors such as the air pressure, rotation speed, and flushing medium all play a crucial role in determining the effectiveness of the drill bit.
It's important to consider these operating parameters when selecting a bit to ensure that it can withstand the specific conditions it will be subjected to during drilling. Neglecting these factors can result in premature wear and tear on the bit, leading to increased maintenance costs and downtime.
Influence of Operating Parameters
The operating parameters, such as air pressure, rotation speed, and flushing medium, have a significant impact on the efficiency of a DTH hammer during down-the-hole drilling operations. It is important to carefully adjust these parameters based on geological conditions to ensure that the hammer operates at its peak performance, resulting in faster penetration rates and reduced operational costs.
Now that we've discussed how factors like drill rig power, proper drill bit selection, and operating parameters affect DTH hammer efficiency, let's explore ways to improve this efficiency even further.
Improving DTH Hammer Efficiency
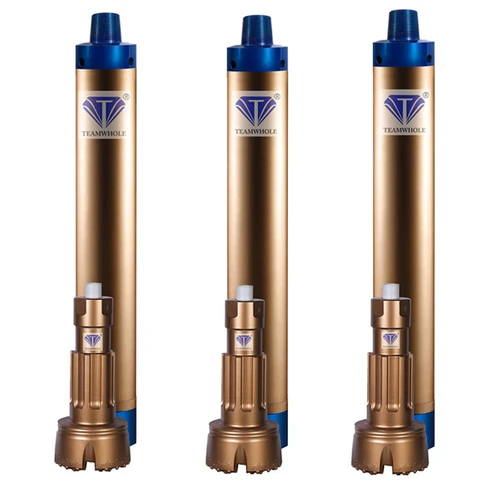
When it comes to improving DTH hammer efficiency, maintenance best practices play a crucial role. Regularly inspecting and servicing the DTH hammer can prevent unexpected breakdowns and ensure optimal performance. By keeping the hammer clean and well-lubricated, you can extend its lifespan and maintain its productivity for down-the-hole drilling operations.
Maintenance Best Practices
Implementing maintenance best practices for your DTH hammer involves:
- Check for wear and tear on components, such as the piston, bit shank, and chuck.
- Replace worn-out parts promptly to avoid compromising drilling efficiency.
- Follow manufacturer-recommended maintenance schedules and procedures is essential for maximizing the lifespan of your DTH hammer.
- Regularly inspect the air cycle in your DTH hammer to ensure proper lubrication and cooling.
Neglecting this aspect of maintenance can lead to overheating and premature wear of internal components. By staying on top of air cycle maintenance, you can prevent costly repairs and downtime.
Utilizing Advanced DTH Hammer Bits
Another key factor in improving DTH hammer efficiency is utilizing advanced DTH hammer bits. Investing in high-quality, durable bits designed for specific rock formations can significantly enhance drilling performance and reduce overall operational costs. With Tianhe's range of innovative DTH hammer bits, you can achieve superior penetration rates and extended bit life for various drilling applications.
Furthermore, Tianhe's advanced DTH hammer bits are engineered to minimize vibration and noise during drilling, creating a more comfortable and safer working environment for operators. This not only improves productivity but also reduces the risk of fatigue-related errors, ultimately contributing to a more efficient and reliable drilling operation. By prioritizing operator well-being, Tianhe's DTH hammer bits set a new standard for performance and safety in the industry.
Tianhe's Role in Enhancing Efficiency
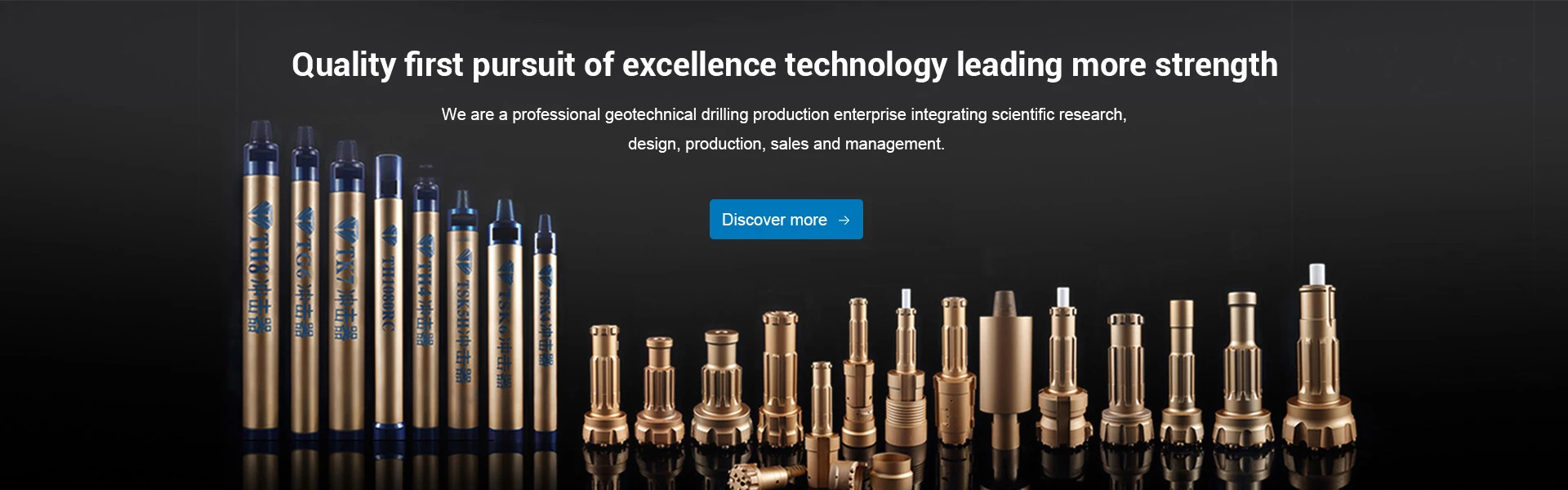
Tianhe plays a pivotal role in enhancing efficiency by providing state-of-the-art DTH hammers and bits that are engineered for maximum productivity. With a focus on research, design, production, sales, and management of geotechnical drilling equipment, Tianhe ensures that its products meet the highest standards of quality and performance. By leveraging Tianhe's expertise in down-the-hole drilling technology, you can elevate your drilling operations to new levels of efficiency.
Remember that maintaining your equipment is essential to achieving optimal performance with your DTH hammers!
Maximizing Down the Hole Drilling Productivity
Minimizing Downtime with Efficient DTH Hammers
When it comes to down-the-hole drilling, minimizing downtime is crucial for maintaining productivity. Efficient DTH hammers, such as those offered by Tianhe, are designed to withstand the rigors of drilling, reducing the need for frequent maintenance and repairs. This means less time spent on downtime and more time focused on getting the job done.
Achieving Cost-Effective Drilling Operations
Cost-effectiveness is a top priority in any drilling operation, and choosing the right equipment can make all the difference. With high-quality DTH hammer bits from Tianhe, you can achieve cost-effective drilling operations by maximizing efficiency and minimizing waste. By investing in reliable equipment, you can reduce overall operational costs and improve your bottom line.
Advantages of Tianhe's DTH Hammer Bits
Tianhe's DTH hammer bits offer a range of advantages that contribute to maximizing down-the-hole drilling productivity. These include superior durability, optimized performance, and compatibility with various drilling conditions. With their innovative design and advanced materials, Tianhe's DTH hammer bits are engineered to deliver exceptional results in demanding drilling applications.
With Tianhe's expertise in geotechnical drilling technology and commitment to quality, you can trust that their products will help you achieve optimal efficiency and productivity in your down-the-hole drilling projects.
Enhancing Drilling Efficiency with DTH Hammer
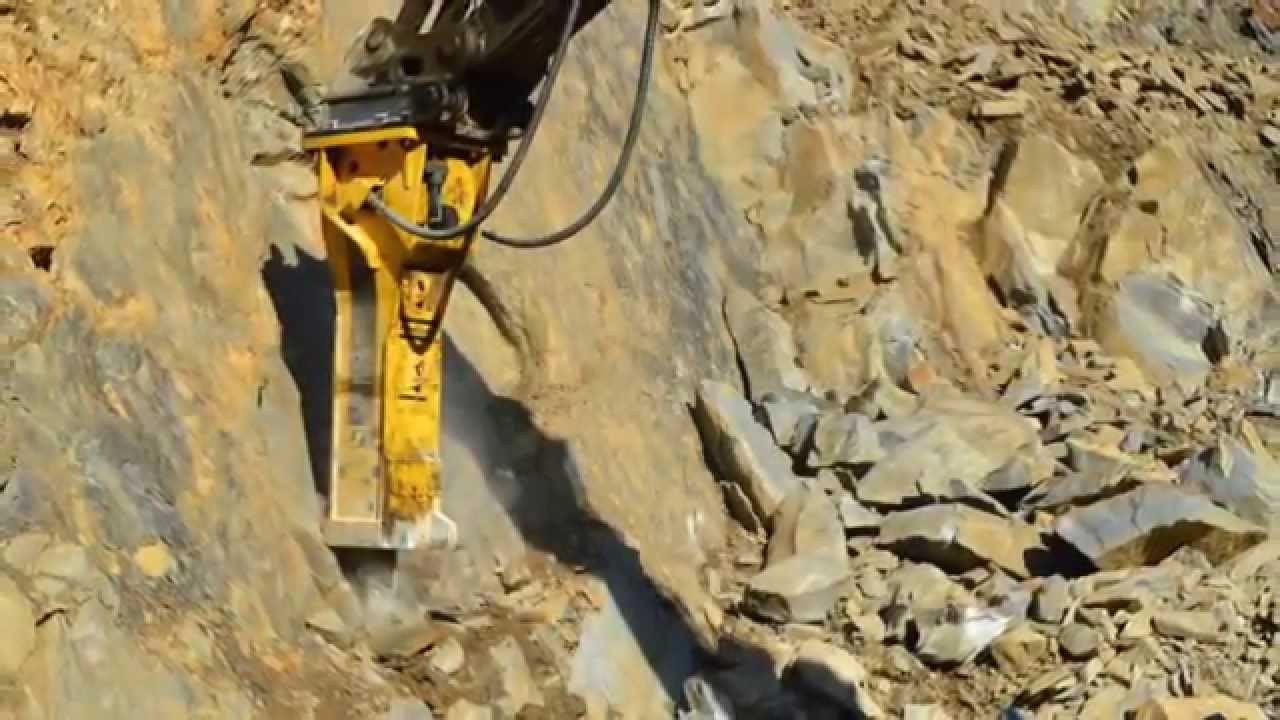
DTH hammer technology has revolutionized down-the-hole drilling, offering enhanced efficiency and productivity for various drilling projects. With the right DTH hammer and bits, such as those offered by Tianhe, drilling operations can be optimized to achieve cost-effective and time-saving results.
By utilizing advanced DTH hammer technology, drillers can significantly enhance drilling efficiency and productivity. The use of high-quality DTH hammer bits and proper maintenance practices can minimize downtime and maximize the performance of the equipment, ultimately leading to successful drilling operations.
Choosing the Right DTH Hammer for Your Project
Selecting the appropriate DTH hammer for a specific project is crucial in achieving optimal results. Factors such as drill rig power, operating parameters, and drill bit selection should be carefully considered to ensure that the chosen DTH hammer is best suited for the job at hand. Tianhe offers a range of reliable DTH hammers to cater to diverse drilling needs.
The Future of DTH Hammer Technology
As technology continues to advance, so does the innovation in DTH hammer technology. With ongoing research and development efforts from industry leaders like Tianhe, we can expect further improvements in the efficiency, durability, and overall performance of down-the-hole hammers. The future holds promising advancements in this essential drilling equipment.
In conclusion, choosing the right DTH hammer and bits is paramount in maximizing down-the-hole drilling productivity. With Tianhe's expertise in geotechnical drilling equipment manufacturing, drillers can look forward to continued advancements that will further enhance their drilling operations for years to come.