Introduction
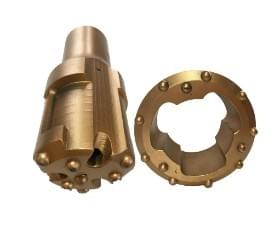
When it comes to down-the-hole drilling tools, DTH hammers are essential for efficient operations in mining and construction. Understanding the common malfunctions, troubleshooting techniques, and regular maintenance is crucial for ensuring seamless drilling processes.
Common DTH Hammer Malfunctions
Common issues with down-the-hole hammers include air leaks, stuck drill bits, and excessive wear on internal components. These malfunctions can lead to costly downtime and reduced productivity if not addressed promptly. To troubleshoot air leaks, carefully inspect all connections and seals for any signs of damage or wear. Stuck drill bits may require disassembly of the hammer to remove any debris or obstructions. Additionally, regular maintenance and monitoring of internal components can help prevent excessive wear and extend the lifespan of the DTH hammer.
Troubleshooting Techniques
Troubleshooting DTH hammer malfunctions involves inspecting the drill rig components, checking air compressor connections, and identifying signs of unusual noise or vibration during drilling operations.
Regular maintenance is essential for ensuring the smooth operation of DTH hammers and drill rigs. By conducting routine inspections and servicing, potential issues can be identified and resolved before they escalate into major malfunctions. This proactive approach not only minimizes downtime but also helps to extend the lifespan of equipment, ultimately saving time and money in the long run.
Importance of Regular Maintenance
Regular maintenance of down-the-hole hammers is vital for preventing malfunctions and prolonging their lifespan. By regularly inspecting and cleaning the hammer, you can identify any potential issues before they become major problems. This proactive approach not only saves time and money on repairs but also ensures that your equipment is always ready for optimal performance when you need it.
Understanding DTH Hammer Operation
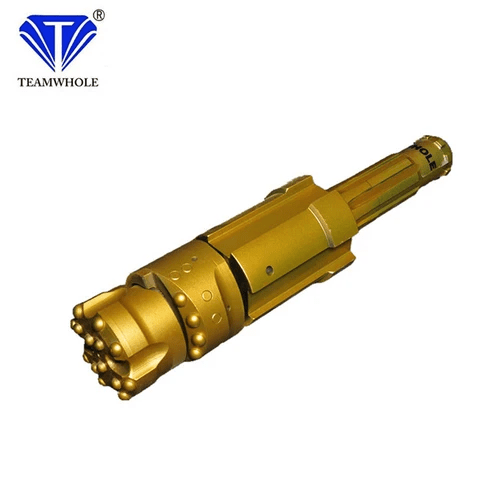
When it comes to drilling, understanding the difference between rotary and DTH drilling is crucial. Rotary drilling involves a drill bit that rotates, creating a hole in the ground. On the other hand, DTH drilling uses a hammer to break the rock, making it more efficient for hard rock formations.
Difference Between Rotary and DTH Drilling
The main difference lies in the way the drilling process is carried out. With rotary drilling, the drill bit rotates while being pushed into the ground, creating a hole through sheer force. In contrast, DTH drilling uses a hammer to pound on the rock continuously, breaking it down into smaller pieces that can be easily removed from the hole.
How Does a DTH Hammer Drill Work?
A DTH hammer drill works by using compressed air to drive a piston inside the hammer assembly. This piston strikes against the back of a drill bit attached to it, creating rapid impacts that effectively break up hard rock formations. The broken rock is then blown out of the hole by the air pressure generated during this process.
Why Does DTH Hammer Malfunction
DTH hammers may malfunction due to various reasons such as inadequate maintenance, worn-out parts, or incorrect usage of equipment. Lack of proper lubrication and regular replacement of worn parts can lead to decreased efficiency and potential breakdowns during operation.
Identifying Malfunction Signs
Unusual Noise and Vibration
One of the signs that indicate a DTH hammer malfunction is the presence of unusual noise and vibration during drilling operations. These could be caused by worn-out or damaged components within the hammer, leading to inefficient drilling and potential safety hazards.
Another indication of a DTH hammer malfunction is fluctuating pressure levels during drilling. Inconsistent pressure can be a result of internal leaks or blockages within the hammer, causing disruptions in the drilling process and potentially damaging the equipment. Monitoring pressure levels closely can help identify these issues early on and prevent costly downtime or repairs.
Fluctuating Pressure Levels
Another indicator of a malfunctioning DTH hammer is fluctuating pressure levels during drilling. Inconsistent air pressure can affect the hammer's performance, leading to uneven drilling depths and poor penetration rates. It is important to monitor pressure levels closely to identify any irregularities.
DTH Drill Machine Crawler Rock Drill Rig for Mining
When using a DTH drill machine crawler rock drill rig for mining, it is crucial to be vigilant for signs of malfunction in the DTH hammer. The efficiency and productivity of mining operations rely heavily on the proper functioning of down-the-hole drilling tools, making it essential to address any issues promptly.
As a vital component of the DTH drill machine crawler rock drill rig, the DTH hammer plays a crucial role in the efficiency and success of mining operations. Therefore, it is imperative to conduct regular inspections and maintenance to ensure that the hammer is functioning optimally. This includes checking for wear and tear, proper lubrication, and monitoring for any unusual sounds or vibrations during operation.
Troubleshooting Steps
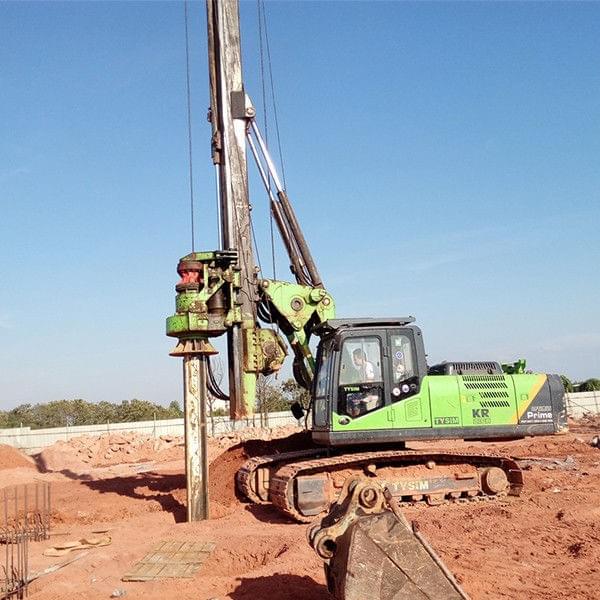
When dealing with DTH hammer malfunctions, it's crucial to follow specific troubleshooting steps to identify and rectify the issues. Inspecting drill rig components is the first step in this process, as worn out or damaged parts can lead to malfunctions. By checking the air compressor connections, you can ensure that the necessary air pressure is being delivered to the DTH hammer for efficient operation. Additionally, understanding the DTH drilling machine price can help in assessing whether any cost-effective upgrades or replacements are required.
Inspecting Drill Rig Components
Inspecting drill rig components involves carefully examining all parts of the rig to identify any signs of wear and tear that could lead to DTH hammer malfunctions. This includes checking the condition of the drill bit, hammer, and other essential components for any signs of damage or deterioration. By conducting regular inspections, you can proactively address any potential issues before they escalate into major malfunctions. Additionally, it is crucial to inspect the hydraulic system for leaks or pressure irregularities, as these can significantly impact the performance and safety of the drill rig. Ensuring that all hydraulic connections are secure and functioning properly is essential for optimal drilling operations.
Checking Air Compressor Connections
The air compressor plays a crucial role in providing the necessary air pressure for DTH hammer drilling operations. Checking the air compressor connections ensures that there are no leaks or blockages that could disrupt the flow of compressed air to the DTH hammer. Any issues with these connections can result in fluctuating pressure levels and impact the overall efficiency of drilling operations.
The connections of the air compressor should be thoroughly checked on a regular basis to ensure optimal performance and prevent any potential issues that could arise during drilling operations. By conducting routine inspections, any leaks or blockages can be promptly identified and addressed, minimizing the risk of disruptions in the flow of compressed air to the DTH hammer. This proactive approach not only helps maintain consistent pressure levels but also contributes to the overall efficiency and productivity of the drilling process.
DTH Drilling Machine Price
Understanding the DTH drilling machine price is essential for making informed decisions about equipment maintenance and upgrades. By evaluating the cost of new components or machinery, businesses can determine whether investing in newer technology is more cost-effective than continually repairing older equipment. This assessment also helps in budgeting for preventive maintenance measures to avoid unexpected downtime due to equipment malfunctions.
Preventive Maintenance Tips
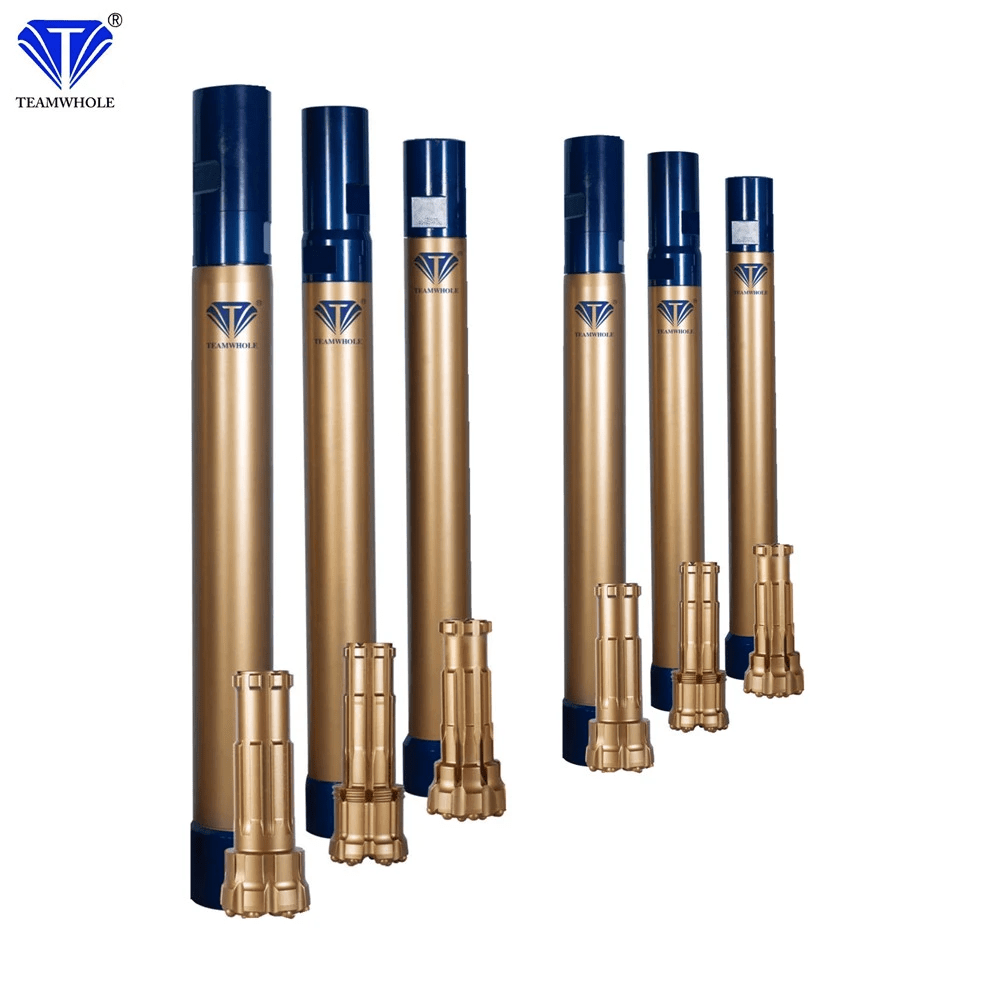
Proper Lubrication Practices
To ensure the smooth operation of down-the-hole drilling tools, proper lubrication is essential. Regularly greasing the DTH hammer and other components helps reduce friction and wear, extending their lifespan and minimizing the risk of malfunction.
In addition to regular greasing, it is important to conduct thorough inspections of the down-the-hole drilling tools to identify any worn or damaged parts. This proactive approach allows for the timely replacement of components that are showing signs of wear, preventing potential breakdowns and downtime. By staying ahead of maintenance needs, you can ensure that your drilling operations continue to run smoothly and efficiently.
Regular Replacement of Worn Parts
Down the hole hammers are subjected to high levels of stress during drilling operations, causing parts to wear out over time. It's crucial to regularly inspect and replace worn components such as drill bits, pistons, and seals to maintain optimal performance and prevent unexpected breakdowns.
Regular maintenance of down the hole hammers is essential to ensure their longevity and efficiency. By keeping a close eye on the wear and tear of components such as drill bits, pistons, and seals, you can avoid costly downtime due to unexpected breakdowns. Additionally, scheduling routine inspections and replacements can help you stay ahead of potential issues, saving you time and money in the long run.
TEAMWHOLE's Efficient DTH Hammers
When it comes to preventive maintenance, choosing high-quality equipment is key. TEAMWHOLE offers a range of efficient DTH hammers designed for durability and reliability. With advanced features and robust construction, these hammers minimize the likelihood of malfunctions, ensuring smooth drilling operations.
Choosing high-quality equipment is just the first step in preventive maintenance. Regular inspections and cleaning are also crucial to ensure that the equipment continues to operate at its best. TEAMWHOLE not only provides durable DTH hammers but also offers comprehensive maintenance guidelines to help users keep their equipment in top condition. By following these guidelines, users can extend the lifespan of their hammers and minimize the need for costly repairs.
Conclusion
DTH hammer drilling is a crucial technique in mining operations, but it's not without its challenges. Understanding the importance of timely troubleshooting is key to maintaining efficient operations. Down-the-hole hammers play a vital role in mining, and their proper functioning is essential for productivity.
Importance of Timely Troubleshooting
Regular maintenance and prompt troubleshooting can prevent costly downtime in mining operations. By identifying and addressing DTH hammer malfunctions early on, companies can avoid delays and keep their drilling processes running smoothly. Timely troubleshooting also helps to extend the lifespan of DTH hammers, reducing the need for frequent replacements and saving on maintenance costs. Additionally, addressing issues promptly can improve overall safety at mining sites, as malfunctioning equipment can pose a risk to workers and the surrounding environment. Taking a proactive approach to troubleshooting demonstrates a commitment to efficiency and responsible mining practices.
Down-the-Hole Hammers in Mining
Down-the-hole drilling tools, such as DTH hammers, are indispensable in the mining industry. These powerful tools enable efficient rock drilling and excavation, making them essential for various mining applications. With their ability to deliver high-impact energy directly to the drill bit, DTH hammers ensure faster penetration rates and lower energy consumption, resulting in cost-effective operations. Additionally, their versatility allows for use in a wide range of geological conditions, from soft to extremely hard rock formations, making them a go-to choice for mining companies worldwide.
DTH Hammer Drilling for Efficient Operations
DTH hammer drilling offers a reliable and efficient method for penetrating hard rock formations during mining operations. Understanding the difference between rotary and DTH drilling techniques is crucial for selecting the most suitable approach for specific geological conditions.
DTH hammer drilling is known for its ability to provide faster penetration rates and lower energy consumption compared to rotary drilling. This makes it a cost-effective and time-efficient option for mining operations, especially in challenging geological conditions. By utilizing high-pressure air to power the hammer, DTH drilling can deliver consistent and precise results, making it a preferred choice for projects where accuracy is paramount.