Introduction
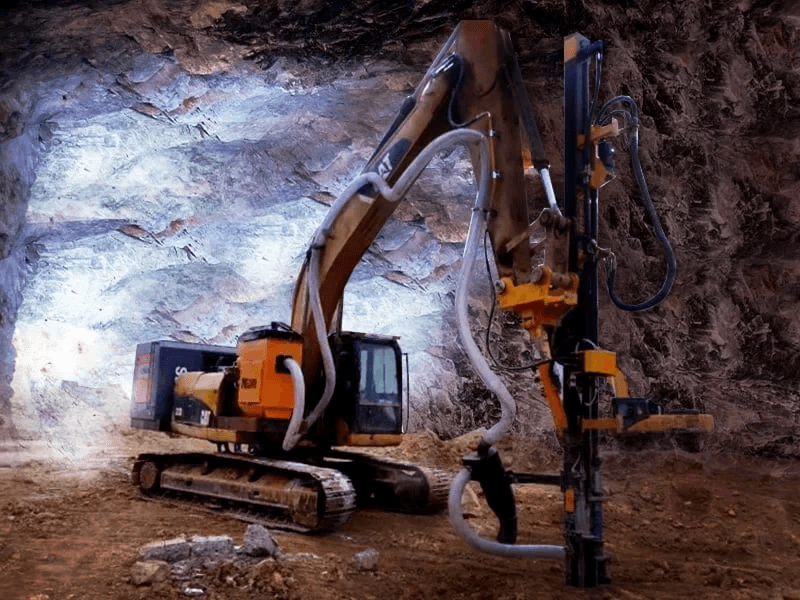
When mining, having the right drilling equipment is crucial for success. Every piece of gear, from drill rigs to down-hole drills, plays a vital role in the extraction process. Efficient drilling is the backbone of any mining operation, ensuring that valuable resources are extracted safely and effectively. And when it comes to top-notch mining drilling equipment, Teamwhole stands out as a leader in providing high-quality and reliable gear for miners around the globe.
Understanding Mining Drilling Equipment
Understanding the intricacies of mining drilling equipment is essential for anyone involved. Each type, from rotary drills to blast hole drills, specifically extracts valuable minerals from the earth. The right equipment can make all the difference in productivity and safety at a mining site.
Importance of Efficient Drilling in Mining
Efficient drilling is the backbone of successful mining operations. Here's how it contributes:
- Boosted Productivity: Faster and more efficient drilling translates to quicker access to valuable resources, significantly increasing overall mining output.
- Enhanced Accuracy: Technological advancements allow precise drilling, minimizing wasted time and resources in unproductive areas.
- Reduced Costs: Efficient drilling operations decrease fuel consumption, equipment wear, and labor costs, improving cost-effectiveness.
- Deeper Reaches: Modern technology allows miners to access previously unreachable resources, expanding possibilities and maximizing resource extraction.
By prioritizing efficient drilling, mining companies can achieve greater productivity, reduce costs, and unlock the full potential of their resources.
Teamwhole: A Leader in Mining Drilling Equipment
Teamwhole has earned its reputation as a leader in providing top-quality mining drills and rig equipment for miners worldwide. Committed to innovation and reliability, Teamwhole offers a range of products catering to modern mining operations' diverse needs.
Types of Mining Drills
When it comes to mining drilling equipment, there are several types of drills that miners rely on for efficient and effective drilling. Rotary drills are commonly used for large-scale mining operations, as they can easily bore through hard rock. Blasthole drills are essential for creating holes for explosives in surface mining, while vertical drills are used for underground mining to reach mineral deposits at different depths.
Rotary Drills
Rotary drills are a vital component of any miner's drilling rig equipment. These powerful machines use a rotating motion to bore into the earth, making them ideal for penetrating tough rock formations. They come in various sizes and configurations, allowing miners to choose the best option.
Rotary drills are powerful and versatile, allowing miners to use different types of drill bits to suit their specific needs. This flexibility is crucial when dealing with varying rock formations and ground conditions, allowing miners to adapt their drilling approach as necessary. Additionally, the ability to easily change out drill bits minimizes downtime, keeping operations running smoothly and efficiently.
Blasthole Drills
Blasthole drills play a crucial role in surface mining operations by creating holes that will later be filled with explosives. These specialized drills are designed to efficiently and accurately drill precise holes at the desired depth and angle, ensuring the success of blasting operations.
Blasthole drills are equipped with advanced technology and features that allow for precise drilling in various rock and soil types. These drills are also designed to withstand the harsh conditions of mining operations, ensuring durability and reliability in the field. Additionally, blast hole drills are operated by highly skilled professionals who undergo extensive training to operate the machinery safely and efficiently.
Vertical Drills
Vertical drills are essential for underground mining, where miners must access mineral deposits at different depths. These versatile drills can create shafts or boreholes vertically into the earth, providing access to valuable resources deep beneath the surface.
Stay tuned as we delve deeper into the components of a drilling rig and explore the fascinating world of down-hole drills!
Components of a Drilling Rig
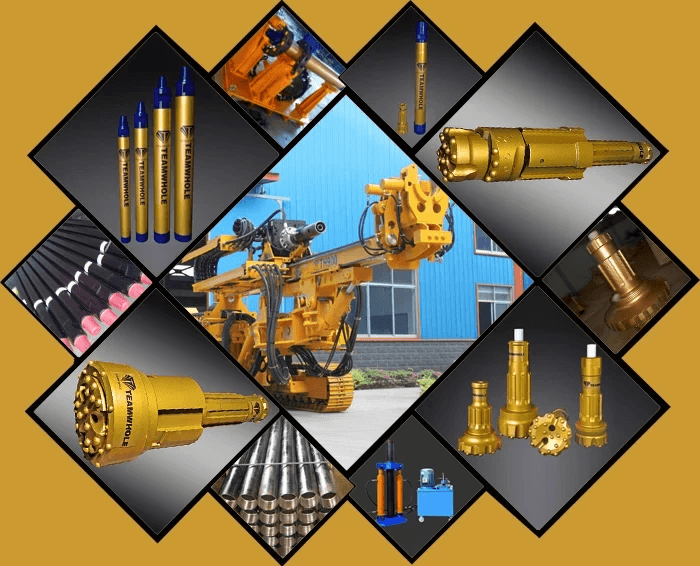
The drilling rig is the heart of the operation when it comes to mining drilling equipment. The drill bit is the cutting tool attached to the end of the drill stem and is responsible for breaking through rock formations. The drill stem is an extended, tubular component that connects the drill bit to the hoisting equipment, allowing for vertical movement during drilling operations.
Drill Bit
The drill bit for mining is a crucial component of any drilling rig. It comes in various sizes and materials, depending on the rock formation being drilled. Tungsten carbide bits are commonly used for their durability and ability to withstand high-impact conditions in mining operations.
Drill bits are designed to cut through different rock formations, including soft, medium, and hard rocks. The size and shape of the drill bit can vary to accommodate the specific needs of each drilling project. In addition to tungsten carbide bits, diamond drill bits are also used for their superior cutting ability and longevity in challenging mining conditions.
Drill Stem
The drill stem is a series of connected pipes that transmit power to the drill bit while allowing for vertical movement during drilling. These pipes are typically made of steel and come in various lengths and diameters to accommodate different depths and types of mining drills.
The drill stem is a crucial component of any drilling operation, providing the necessary power to the drill bit while allowing for vertical movement. These pipes are designed to withstand the high pressures and forces encountered during drilling, making them typically made of durable steel. In addition to their strength, drill stems come in various lengths and diameters, allowing customization to accommodate different depths and types of mining drills.
Hoisting Equipment
Hoisting equipment is responsible for lifting and lowering the drill string into the borehole during miner drilling operations. This includes winches, pulleys, and cables designed to handle heavy loads while maintaining precise control over depth and speed.
Now that we've covered the essential components of a drilling rig, let's examine downhole drills and their significance in mining operations.
Down Hole Drills
Down Hole Drill Components
Downhole drills consist of several key components, including the drill bit, drill stem, and drilling fluid system. The drill bit is crucial for cutting through rock formations, while the drill stem provides the necessary length and strength to reach deep into the earth. The drilling fluid system helps to cool and lubricate the drill bit and carry rock cuttings to the surface.
Downhole drills are essential for various industries, including oil and gas exploration, mining, and geothermal energy production. The drill bit is designed to withstand high temperatures and pressures while cutting through various rock formations effectively. Additionally, the drill stem is carefully engineered to provide the necessary length and strength to reach deep into the earth's crust, allowing for efficient resource extraction. The drilling fluid system plays a critical role in maintaining the integrity of the drilling process by cooling and lubricating the drill bit, ensuring smooth operations.
Function of Down Hole Drills
The primary function of downhole drills is to create boreholes in the earth for various mining operations. These drills are designed to penetrate hard rock formations efficiently and effectively, allowing miners to access valuable mineral deposits deep underground. By using downhole drills, miners can extract resources precisely and minimize environmental impact.
Benefits of Using Down Hole Drills
Down-the-hole (DTH) drills are a game-changer for mining operations, offering numerous advantages:
- Increased Efficiency: DTH drills excel at fast and accurate drilling, reducing downtime and significantly boosting productivity.
- Enhanced Control and Safety: They provide superior control over borehole direction and depth, improving worker safety and maximizing resource recovery.
- Environmental Benefits: Compared to traditional methods, DTH drills minimize environmental impact. Precise drilling reduces waste and the need for land clearing, contributing to sustainable mining practices.
By incorporating DTH drills, mining operations can achieve greater efficiency, improve safety, and operate more sustainably, making them a vital tool for the modern mining industry.
Choosing the Right Drill Bit for Mining
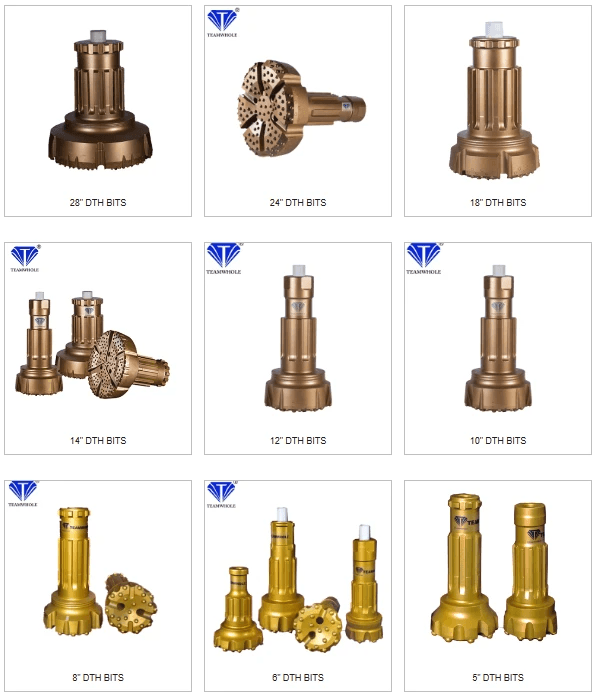
When it comes to choosing the right drill bit for mining, several factors must be considered. The type of rock formation you will be drilling into, the depth of the hole, and the desired hole diameter are all important considerations. Teamwhole understands these factors and offers a wide range of DTH bits to meet miners' specific needs.
Factors to Consider
The hardness and abrasiveness of the rock formation will determine the type of drill bit needed for efficient drilling. Additionally, considering the required depth and diameter of the hole is crucial in selecting the right drill bit. Teamwhole considers all these factors when designing their range of DTH bits, ensuring that miners have access to high-quality equipment that meets their specific requirements.
Teamwhole's Range of DTH Bits
Teamwhole's range of DTH bits includes various designs and sizes to accommodate different drilling needs. Whether drilling in soft or hard rock formations or shallow or deep holes, Teamwhole has a selection of drill bits that offer durability and efficiency. Miners can rely on Teamwhole's expertise to provide reliable drilling equipment.
Teamwhole's range of DTH bits is designed to provide optimal performance in various drilling conditions. From the most challenging rock formations to softer materials, our drill bits are engineered to deliver consistent results with minimal wear and tear. This means that miners can confidently rely on our equipment to tackle any drilling challenge, knowing that they have the right tools for the job.
Matching the Drill Bit to the Rock Formation
Matching the drill bit to the specific rock formation is essential for successful mining operations. DTH bits are designed for different rock types, ensuring optimal performance and longevity. With Teamwhole's expertise in mining drilling equipment, miners can trust that they will find a suitable drill bit that matches their specific rock formations. Additionally, understanding the geological composition of the rock formations can help determine the best drilling technique and equipment to use, further enhancing efficiency and productivity in mining operations. By considering hardness, abrasiveness, and rock porosity, miners can make informed decisions when selecting the appropriate drill bit for their specific needs.
Maintenance of Drilling Rig Equipment
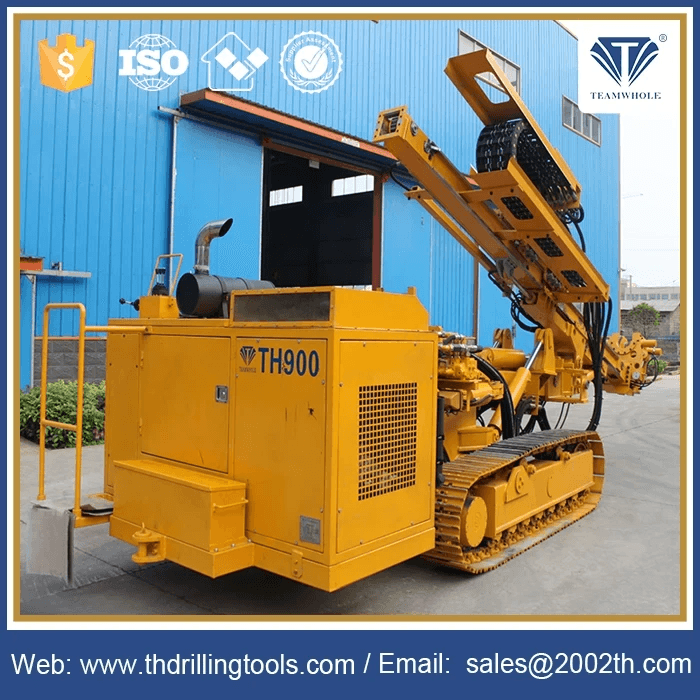
Importance of Regular Maintenance
Effective maintenance is essential for keeping mining drilling equipment running smoothly. Here's why a regular maintenance program is crucial:
- Prevent Breakdowns: Regular inspections and servicing help identify and address minor issues before they escalate into major breakdowns, minimizing costly repairs and downtime.
- Maximize Performance: Properly maintained equipment operates at peak efficiency, ensuring consistent drilling depth, speed, and accuracy.
- Extend Equipment Lifespan: By proactively addressing wear and tear, you can significantly extend the life of your drilling equipment, reducing replacement costs and maximizing your investment.
- Enhance Safety: Regular maintenance helps to identify and address potential safety hazards associated with worn-out parts or malfunctioning equipment, creating a safer work environment for miners.
- Boost Profitability: By minimizing downtime, maximizing performance, and extending equipment life, a well-maintained drilling fleet translates to increased productivity and profitability for your mining operation.
Prioritizing regular maintenance of your mining drilling equipment offers many benefits, ensuring safety, efficiency, and, ultimately, a more profitable mining operation.
Common Maintenance Practices
Standard maintenance practices for drilling rigs include inspecting and replacing worn drill bits, lubricating moving parts, checking hydraulic systems for leaks, and monitoring the overall condition of the rig. These practices help to identify potential issues early on and address them before they escalate into major problems.
Teamwhole's Maintenance Support
Teamwhole understands the importance of maintaining drilling rig equipment and offers comprehensive maintenance support to miners. From providing regular servicing to offering technical assistance, Teamwhole ensures that its client's equipment operates at peak efficiency.
The Future of Mining Drills
Mining drilling equipment has come a long way, and the future looks promising with continued technological advancements. Innovations in mining drill technology are revolutionizing the industry, making drilling rigs more efficient and safer for miners. Choosing the right equipment for your mining operation is crucial to ensuring maximum productivity and safety.
The future of mining drills is bright, with ongoing developments focused on increasing drilling speed, accuracy, and safety. As technology continues to evolve, we expect to see more automated and remote-controlled drilling rigs that minimize human intervention while maximizing efficiency.
Innovations in Mining Drill Technology
Innovations in mining drill technology have led to the development of advanced features such as real-time monitoring systems, data analytics capabilities, and self-adjusting drilling parameters. These innovations improve drilling efficiency and enhance safety by providing miners with valuable insights into ground conditions.
Choosing the Right Equipment for Your Mining Operation
Selecting the proper mining drills and drilling rig equipment is vital for optimizing productivity and minimizing downtime. Factors such as the type of rock formation, depth of drilling, and environmental considerations should all be considered when choosing equipment for your mining operation.
With Teamwhole's expertise in manufacturing high-quality mining and down-hole drills, you can trust that you're getting top-of-the-line equipment designed to meet your needs. As you look towards the future of your mining operation, stay informed about innovations in mining drill technology that could further improve your efficiency and safety.