Introduction

Down hole drilling is the go-to method when drilling deep into the earth for various purposes. This process involves using a drill with drill bits to create holes in the ground, whether for mining, oil and gas exploration, or geotechnical purposes. Over time, the evolution of drilling technology has significantly improved the efficiency and precision of this process. As a result, quality drill bits have become essential for achieving optimal results in down hole drilling operations. In this field, Tianhe has emerged as a key player in providing innovative solutions for geotechnical drilling.
Understanding Down Hole Drilling
Down hole drilling refers to using a drill and drill bits to create holes in the ground for various industrial purposes such as mining, oil and gas extraction, and geotechnical surveys.
Evolution of Drilling Technology
The evolution of drilling technology has revolutionized down hole drilling by introducing advanced machinery and techniques that have significantly enhanced efficiency and precision.
Importance of Quality Drill Bits
Don't underestimate the importance of a quality drill bit! It can make all the difference in your project. Here's why investing in good drill bits is essential:
- Precision and Clean Cuts: High-quality drill bits deliver clean, accurate holes, reducing the risk of chipping, breaking, or damaging your material.
- Faster Drilling: Made from stronger materials and featuring sharper cutting edges, quality drill bits bite effortlessly through materials, saving you time and effort.
- Increased Durability: Cheap drill bits quickly wear down and become dull. Quality bits resist wear and tear, lasting longer and saving you money in the long run.
- Safety Matters: Dull or weak bits can break or bind during use, posing a safety hazard. Quality drill bits perform consistently and reliably, reducing the risk of accidents.
Spending a little more on quality drill bits ensures a smoother, safer, and more efficient drilling experience. Ditch the cheap options and invest in bits that will get the job done right!
The Role of Tianhe in Geotechnical Drilling
Tianhe has played a pivotal role in geotechnical drilling by providing cutting-edge solutions that have redefined industry standards and contributed to advancements in this field.
Now, you can continue writing from where I left off!
The Basics of Down Hole Drilling
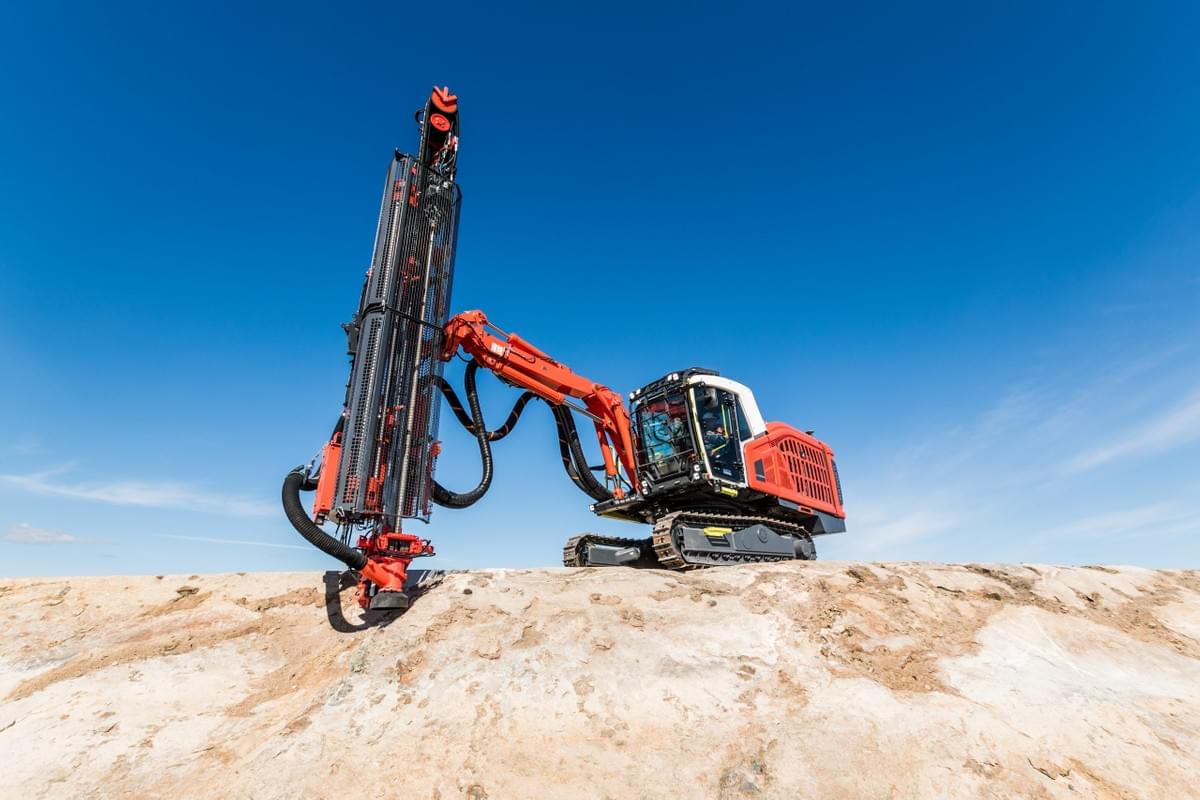
Down hole drilling is crucial in extracting natural resources from the earth's surface. There are various types of drilling methods, including rotary, cable tool, and percussion. Each method has its unique advantages and is used based on the specific geological conditions of the site.
Exploring Different Types of Drilling
There are many ways to drill into the earth, each with its strengths and applications. Here are three common types of drilling methods:
- Rotary Drilling: This method utilizes a rotating drill bit to create boreholes. It's a popular oil and gas exploration choice because it efficiently penetrates hard rock formations.
- Cable Tool Drilling: This technique uses a heavy bit on a cable that repeatedly drops and strikes the ground, breaking up rock.
- Percussion Drilling: This method employs a hammer drill to break through rock with a chisel-like bit that repeatedly strikes the surface.
We can choose the most appropriate technique for a specific project or geological condition by understanding these different drilling methods.
Key Components of a Drilling Operation
Every drilling operation's heart lies in a complex interplay of essential components. These components work together to create a deep, stable hole.
- Drill Rig: This powerful machine serves as the drilling operation's workhorse. It provides the stability and force needed to overcome the resistance of the earth and rotate the drill string.
- Drill String: This long, hollow tube is an extension of the drill rig, carrying drilling fluid and the drill bit down the hole. It's made up of multiple drill pipes screwed together and can reach incredible lengths depending on the depth of the well.
- Drill Bit: A drill bit is a specialized tool that breaks through rock or earth formations. Different geological conditions require different drill bit types, each optimized for specific drilling challenges.
By carefully selecting and operating these components, drilling professionals can achieve efficient and successful drilling operations, reaching depths far below the Earth's surface.
Safety Measures in Drilling Operations
Safety is paramount in any drilling operation to prevent accidents and protect workers' well-being. All personnel involved in down-hole drilling activities should receive proper training on equipment operation and safety protocols. Additionally, regular equipment inspections and adherence to safety guidelines can significantly reduce risks associated with drilling operations.
In addition to proper training and regular equipment inspections, it is essential to establish clear communication channels among all team members involved in drilling operations. Effective communication ensures that everyone is aware of potential hazards and can work together to address any safety concerns promptly. Furthermore, implementing emergency response drills and protocols can help prepare workers for unexpected situations, ultimately minimizing the impact of accidents and ensuring a quick and coordinated response.
Selecting the Right Drill Bits
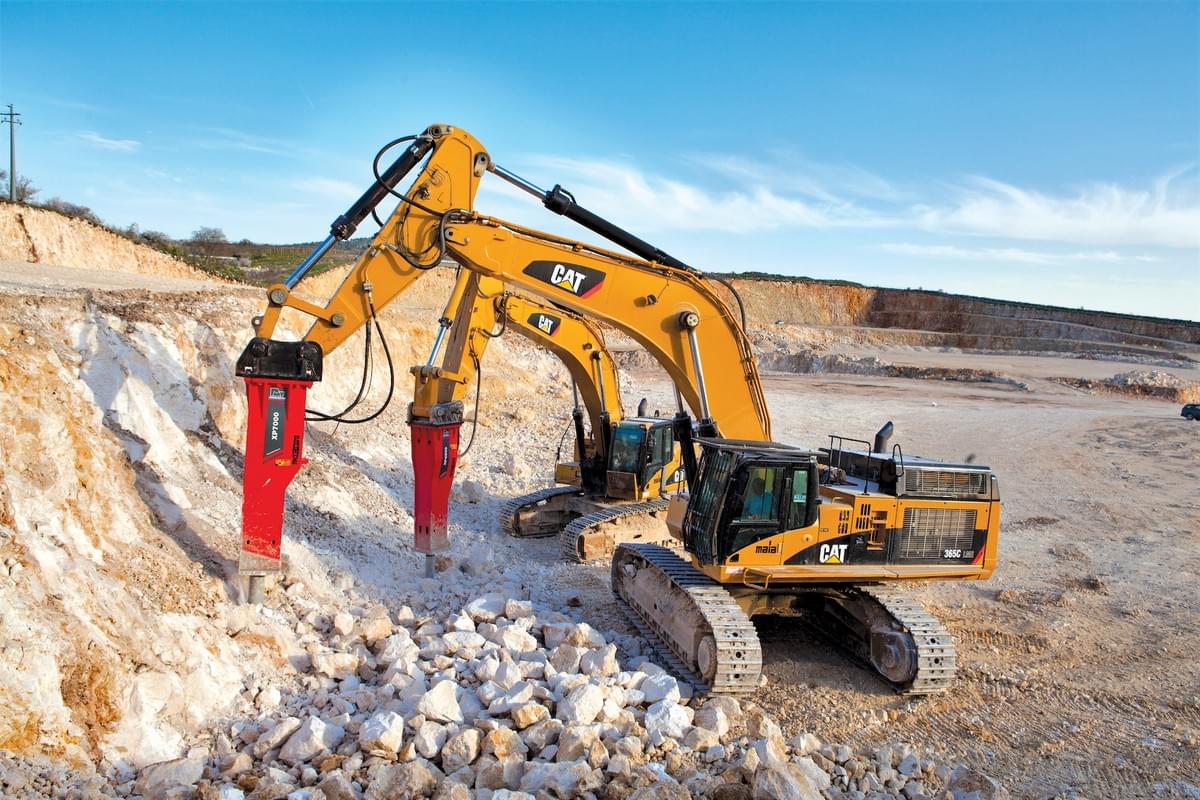
Selecting the right drill bits is crucial for a successful operation when it comes to down hole drilling. Factors to consider in drill bit selection include the type of formation being drilled, the desired drilling speed, and the longevity of the drill bit. It's essential to choose a drill bit that matches the specific requirements of the drilling project to ensure optimal performance and efficiency.
Factors to Consider in Drill Bit Selection
Selecting the right drill bit is crucial for an efficient and successful drilling project. Here are several key factors to consider when choosing a drill bit:
- Material of the Workpiece: The type of material you're drilling into is the most important factor. Soft materials like wood or plastic require different bits than hard materials like concrete or steel.
- Desired Drilling Speed: Do you prioritize a fast drilling rate or a clean, precise hole? Different bits are designed for speed or controlled drilling.
- Drill Bit Durability: Consider the drilling conditions and how long you need the bit to last. More durable bits can handle more challenging materials and will need to be replaced less often.
By considering these factors, you can choose the best drill bit for your specific needs and ensure a smooth and successful drilling project.
Types of Drill Bits for Specific Purposes
Downhole drilling operations require a variety of drill bits to tackle different formations. Each bit type is designed with specific strengths to optimize performance in certain materials. Here are some of the most common types of drill bits and their applications:
- PDC (Polycrystalline Diamond Compact) Bits: Known for their durability and efficient cutting capabilities, PDC bits are ideal for drilling through complex rock formations.
- Roller Cone Bits: More versatile than PDC bits, roller cone bits can be used in various formations, including soft, medium, and complex formations.
Choosing the right drill bit for the job is crucial for efficient and successful drilling operations. By understanding the strengths of each bit type, you can select the best tool for the specific formation you're encountering.
Innovative Drill Bit Technologies
Innovative technologies have significantly improved drill bit performance in down hole drilling operations. Advanced materials such as tungsten carbide and diamond-enhanced inserts have enhanced the durability and wear resistance of modern drill bits. Furthermore, advancements in design and engineering have led to specialized cutters that can effectively handle challenging formations with greater efficiency.
With careful consideration of factors such as formation type, desired speed, and longevity, along with knowledge about different types of drill bits suited for specific purposes and awareness of innovative technologies available in today's market, selecting the right drill bit becomes an essential aspect in achieving successful down hole drilling operations.
Techniques for Efficient Drilling
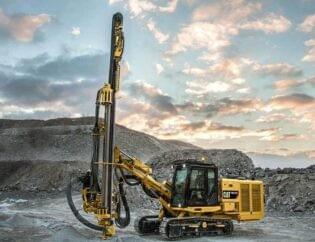
When it comes to efficient drilling, utilizing hammer drill technology can significantly improve the speed and precision of drilling operations. A hammer drill uses a pulsating mechanism to deliver rapid blows to the drill bit, allowing for quicker penetration into rigid materials like concrete and masonry. This technology is essential for down hole drilling in challenging geological formations.
Utilizing Hammer Drill Technology
By incorporating a hammer drill into your drilling operations, you can easily tackle hard surfaces, reducing the time and effort required for each project. The impact force generated by a hammer drill enables the bit to break through tough materials efficiently, making it an indispensable tool for geotechnical drilling in various terrains. With its ability to deliver rapid blows while rotating, a hammer drill ensures that you can achieve precise and effective results in down hole drilling.
Maximizing Production in Drilling Operations
Maximizing production in drilling operations involves optimizing equipment and resources to enhance efficiency and output. By employing advanced technologies such as hammer drills, you can increase the speed and accuracy of drilling processes, leading to higher productivity levels. This saves time and reduces costs associated with prolonged drilling activities, making it a valuable asset for any geotechnical drilling project.
Implementing Advanced Drilling Techniques
Implementing advanced drilling techniques goes beyond traditional methods and equipment; it involves leveraging innovative technologies like hammer drills to achieve superior results. The combination of advanced tools and techniques allows for precise control over the drilling process, ensuring that each project is completed with maximum efficiency and accuracy. By embracing these cutting-edge approaches, you can elevate your down hole drilling operations to new heights of performance and success.
In addition to using innovative technologies like hammer drills, implementing advanced drilling techniques also involves training and upskilling personnel to utilize these tools effectively. By investing in developing your team's skills and knowledge, you can ensure that they can leverage the full potential of advanced equipment, leading to improved productivity and quality of work. This emphasis on human capital as a crucial component of advanced drilling techniques sets your operations apart and positions you for long-term success in the industry.
Maintenance and Upkeep of Drilling Equipment
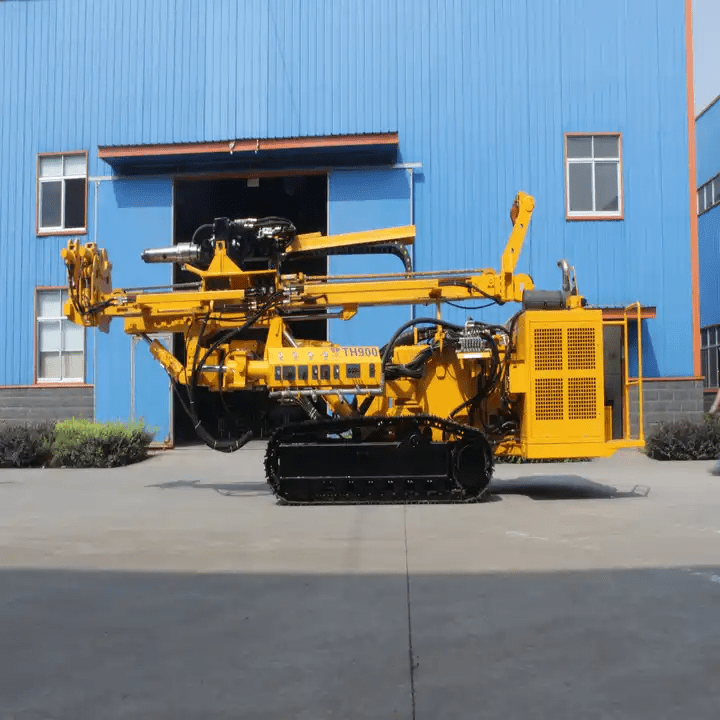
Maintaining your equipment is crucial for optimal performance when it comes to down hole drilling. Regular maintenance of the drill and drill bits ensures they remain in top condition, preventing costly breakdowns and downtime. Proper lubrication, cleaning, and inspection of the drill components are essential best practices for drill maintenance.
Best Practices for Drill Maintenance
A proper maintenance routine is vital for ensuring your drill operates at its best. Here are some key practices to incorporate:
- Schedule Regular Inspections: Proactively check for wear and tear on drill components like belts, chucks, and bits. This allows you to replace parts before they fail and cause downtime.
- Replace Worn Parts: Don't wait for parts to break completely. By replacing worn bits, brushes, and other components at the first sign of wear, you can prevent damage to the drill itself.
- Lubricate Regularly: Friction is the enemy of any machine. Regularly lubricating moving parts according to the manufacturer's instructions reduces wear and tear, extending the life of your drill.
- Inspect Crucial Systems: Don't overlook the drill's hydraulic systems, electrical connections, and overall structural integrity. Schedule regular inspections to identify potential problems before they lead to malfunctions.
By following these practices, you can ensure your drill operates safely and efficiently for years.
Prolonging the Lifespan of Drill Bits
Drill bits are vital to any drilling operation, and extending their lifespan is key to efficiency. Using high-quality drill bits for specific drilling tasks can significantly prolong their lifespan. Proper storage in a dry environment and regular sharpening or reconditioning of dull bits can also help maximize their longevity.
Importance of Regular Equipment Inspections
Regular inspections are an essential part of any drilling operation. Here's how they benefit your business:
- Preventative Maintenance: By catching minor issues before they snowball into major problems, inspections minimize unexpected downtime caused by equipment failure.
- Extended Equipment Lifespan: Regular checks identify and address wear and tear early on, allowing you to extend the lifespan of your valuable equipment. This translates to significant cost savings in the long run.
- Safety and Compliance: Proactive inspections demonstrate a commitment to worker safety and adherence to industry regulations, which is paramount in the drilling industry.
Taking the time for regular equipment inspections is an investment that pays off in terms of safety, efficiency, and cost savings.
Advancements in Down Hole Drilling
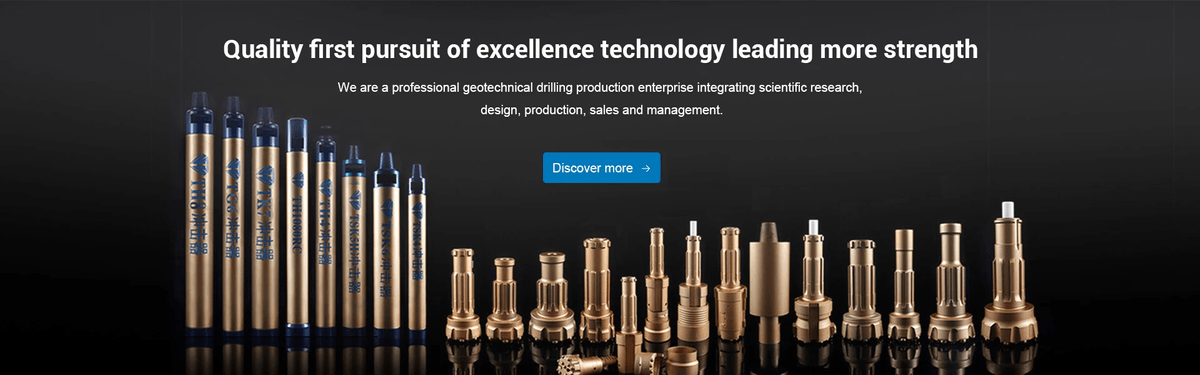
With the rapid advancements in technology, the future of drilling is set to be more efficient and precise than ever before. Innovations such as advanced sensors and real-time data analysis are revolutionizing down hole drilling, allowing for more accurate and effective operations. These technological developments pave the way for increased productivity and reduced downtime in drilling operations.
Future of Drilling Technology
The future of drilling technology is incredibly promising, with ongoing research and development leading to the creation of more durable and efficient drill bits. These advancements will allow deeper and faster drilling, ultimately improving project timelines and reducing costs. Integrating artificial intelligence (AI) into drilling equipment will also enable autonomous decision-making, further enhancing operational efficiency.
Sustainability in Drilling Operations
Sustainability is a key focus in modern drilling operations, with an increasing emphasis on minimizing environmental impact. Sustainable practices include using biodegradable drilling fluids, energy-efficient equipment, and responsible waste management strategies. Companies can reduce their ecological footprint by implementing these sustainable measures while maintaining high productivity levels.
Enhance Productivity with Advanced Drilling Techniques
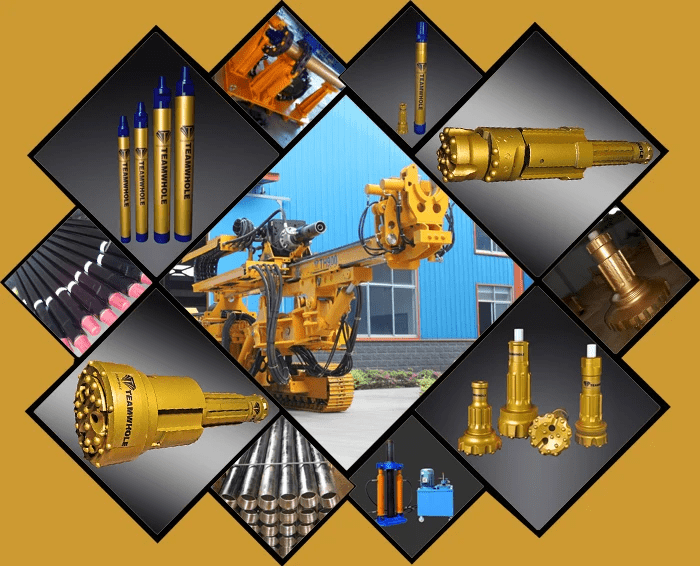
Advanced drilling techniques have significantly enhanced productivity in down hole drilling operations. Companies can maximize production and efficiency by incorporating innovative drill bits and hammer drill technology. Sustainable drilling practices are also crucial for the future, ensuring minimal environmental impact and long-term viability. Tianhe's revolutionary approach to geotechnical drilling is setting new standards in the industry, making it a leader in the field.
Advanced drilling techniques, such as hammer drills and innovative drill bits, have enhanced productivity in downhole drilling operations. These cutting-edge technologies allow faster and more efficient drilling, increasing output and reducing operational costs.
Sustainable Drilling Practices for the Future
As environmental concerns continue to grow, sustainable drilling practices are becoming increasingly crucial for the future of down hole drilling. Companies now focus on minimizing their ecological footprint by implementing eco-friendly drilling methods and adhering to strict regulations to ensure responsible resource extraction.
Tianhe: Revolutionizing Geotechnical Drilling
Tianhe has emerged as a trailblazer in geotechnical drilling, revolutionizing the industry with their innovative approaches and state-of-the-art equipment. Their commitment to sustainability and cutting-edge technologies positions them as a key player in shaping the future of down hole drilling.