Introduction
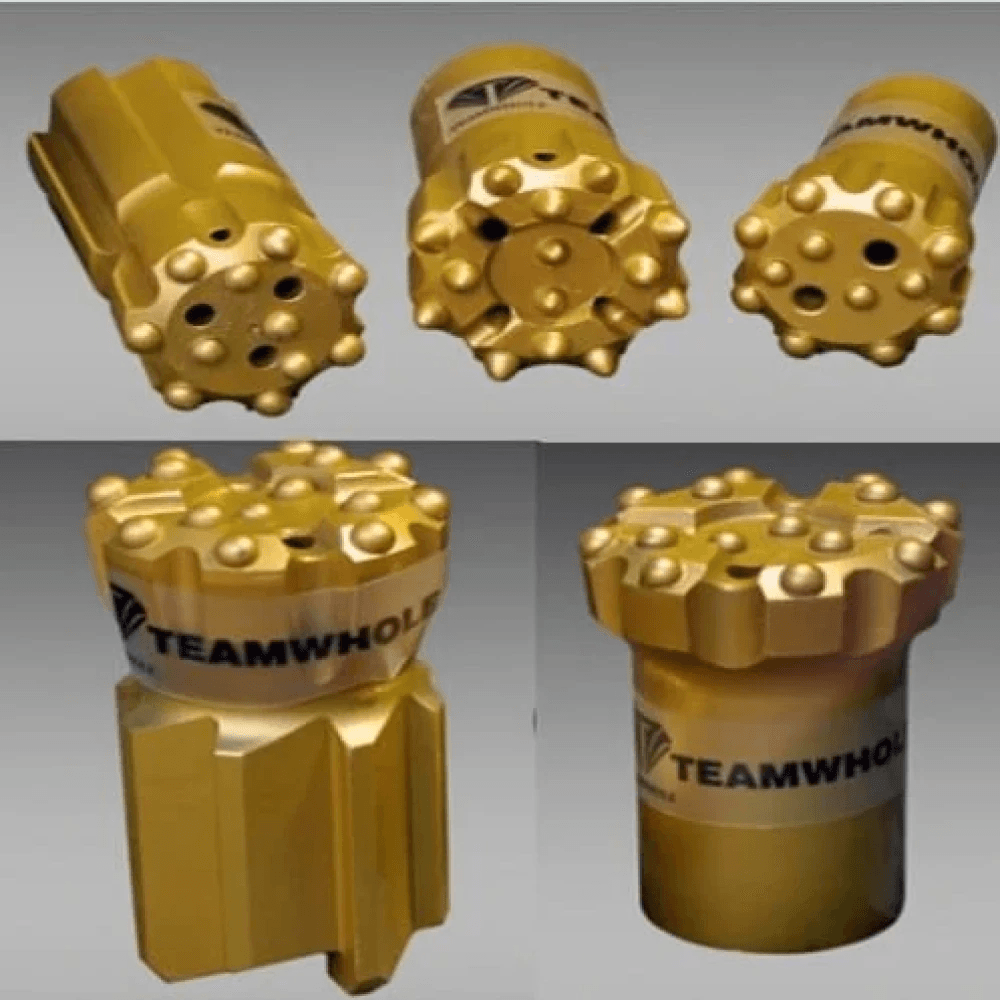
Are you ready to delve into the world of drilling button bits? These small but mighty tools are essential for any rock drilling project, and understanding their basics is crucial for success. From choosing the right button bit to exploring the common types used in rock drilling, this comprehensive guide will cover it all.
Understanding the Basics of Drilling Button Bits
Drilling button bits are essential tools for efficiently breaking through rock formations. These specialized bits utilize small, hardened buttons that create an impactful force as they rotate, effectively disintegrating the rock. Understanding how they operate is crucial to maximizing their performance.
- Button design: The shape and composition of the buttons significantly impact drilling efficiency.
- Bit body: The bit's structure, including its skirt and shank, influences its stability and durability.
- Rock formation: Different rock types require specific button bit configurations for optimal results.
By understanding these key factors, you can select the right button bit for your drilling project and achieve optimal results.
The Importance of Choosing the Right Button Bit
Selecting the appropriate button bit for your drilling project can make all the difference in speed, accuracy, and overall success. Different rock formations require different types of button bits, so knowing how to choose the right one is crucial for achieving optimal results.
Common Types of Button Bits for Rock Drilling
From DTH button bits to various button shank types, a wide range of options are available for rock drilling applications. Each type has its unique features and benefits, making it essential to understand which one best suits your specific project needs.
The Anatomy of a Drilling Button Bit
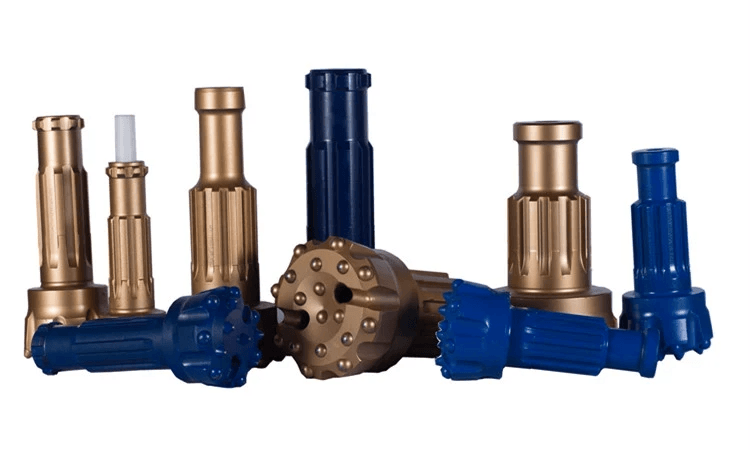
Understanding the Components of a Button Bit
When understanding the components of a drilling button bit, it's essential to recognize that these bits comprise several key parts. The most important component is the button, which is typically made from tungsten carbide and responsible for breaking and crushing the rock. The bit body, also known as the head, houses the buttons and provides support during drilling operations. Additionally, the shank connects the button bit to the drill rod, allowing for efficient power transmission and rotation.
Different Types of Button Shank for Various Drilling Applications
Button bits come in various shank types to accommodate different drilling applications. The most common shank types include DTH (Down-The-Hole) and thread shanks. DTH button bits are ideal for deep-hole drilling and are designed to withstand high-impact energy, making them suitable for hard rock formations. On the other hand, thread button bits are more versatile and can be used in a wide range of drilling conditions, offering excellent performance in soft and hard rock formations.
DTH button bits are specifically designed for deep-hole drilling, making them ideal for applications such as mining and quarrying. These bits can withstand high-impact energy, allowing them to penetrate hard rock formations with ease. In contrast, thread button bits offer versatility. They can be used in various drilling conditions, making them suitable for construction and civil engineering projects where the rock formations may vary from soft to hard. This makes them a popular choice for contractors who need a reliable and adaptable solution for their drilling needs.
How DTH Button Bits Differ from Thread Button Bits
One notable difference between DTH and thread button bits lies in their design and application. DTH button bits feature multiple buttons arranged in clusters on their face, allowing for efficient rock penetration and removal. These bits are commonly used with hammer drills to achieve high penetration rates in challenging geological conditions. In contrast, thread button bits have individual buttons spaced across their face, providing consistent performance across various rock formations without compromising durability or efficiency.
While DTH button bits are known for their ability to efficiently penetrate challenging rock formations, thread button bits offer consistent performance across various rock types without sacrificing durability or efficiency. This distinction makes it crucial for project managers and drilling professionals to carefully consider the specific geological conditions of their worksite when selecting the appropriate button bit for their project. By understanding the unique capabilities of each type of button bit, they can ensure optimal drilling performance and cost-effectiveness.
Choosing the Right Button Bit for Your Project
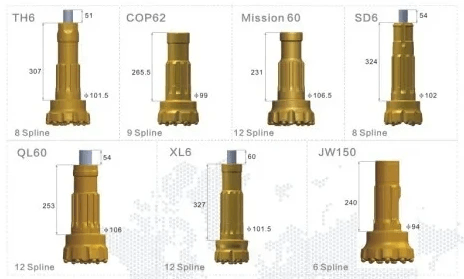
When selecting a drilling button bit, several factors must be considered to ensure optimal performance. The type of rock formation you will be drilling into, the depth of the hole, and the required drilling speed are all important considerations. Additionally, the size and power of your drilling rig will also play a role in determining the right button bit for your project.
Factors to Consider When Selecting a Button Drill Bit
Selecting the right button bit for your drilling project is crucial for optimal efficiency and performance. The key to selecting the appropriate bit lies in understanding the specific characteristics of the rock formation.
- Rock Hardness and Abrasiveness: Determines the button bit’s size, durability, and configuration. Harder formations require larger, more durable buttons for efficient penetration.
- Button Size and Shape: Impacts penetration rates and overall drilling performance. Larger, more durable buttons are ideal for hard formations, while smaller, closely spaced buttons are better suited for softer rocks.
- Button Placement: Influences the bit’s ability to break through the rock. Proper button placement optimizes drilling performance.
By carefully considering these factors, you can choose the button bit that best suits your drilling needs and achieve optimal results.
Matching the Button Bit to the Rock Formation
Matching your button bit to the specific characteristics of the rock formation is crucial for success in any drilling project. For example, if you are working with highly abrasive rock, a button bit with carbide inserts may be necessary to withstand wear and tear. Understanding these geological factors is key to selecting the right button bit.
Matching your button bit to the specific characteristics of the rock formation is crucial for success in any drilling project. For example, if you are working with highly abrasive rock, a button bit with carbide inserts may be necessary to withstand wear and tear. Understanding these geological factors is key to selecting the right button bit. Additionally, considering the hardness and density of the rock formation will help determine the type of button bit that can efficiently penetrate the surface without excessive force or damage.
The Impact of Button Bit Design on Drilling Performance
The design of a button drill bit can significantly impact its performance during rock drilling operations. Factors such as flushing capability, face design, and gauge protection all influence how efficiently a button bit can penetrate different formations. It's important to carefully evaluate these design elements when choosing a button bit for your project.
Proper Maintenance and Care for Button Bits
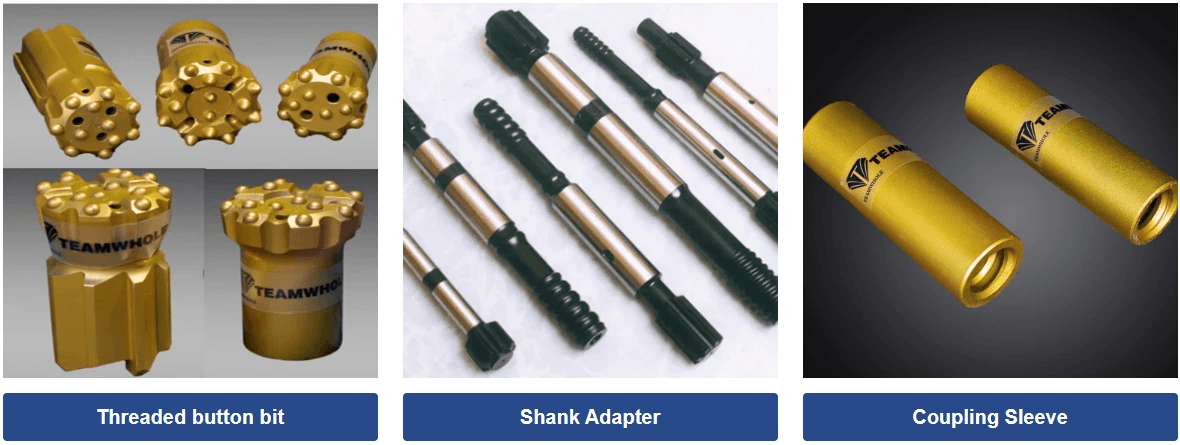
Extending the Lifespan of Your Button Bits
Proper maintenance and care are crucial to extending the lifespan of your drilling button bits. Regularly inspecting and cleaning the button bits after each use can prevent premature wear and tear. Investing in high-quality button bits from reputable suppliers can contribute to their longevity.
Best Practices for Cleaning and Storing Button Bits
Proper care of your button bits is crucial for their longevity and performance. To ensure optimal results, follow these steps:
- Clean thoroughly: Remove debris and buildup from the buttons and shank using a specialized cleaning solution.
- Store correctly: Place button bits in a dry, cool environment to prevent damage and corrosion.
- Inspect regularly: Check for signs of wear, such as chipping, cracking, or dullness in the buttons and any deformation of the shank.
- Keep records: Maintain detailed records of button bit condition to track performance and plan replacements.
By following these guidelines, you can significantly extend the life of your button bits and minimize downtime.
Recognizing Signs of Wear and Tear in Button Bits
Regularly inspecting your button bits for signs of wear and tear is crucial for maintaining optimal drilling performance. Look out for dull or chipped buttons and any damage to the shank or body of the bit. Identifying these issues early can help prevent costly downtime and ensure efficient rock drilling operations.
Remember that proper maintenance and care are essential for maximizing the lifespan and performance of your drilling button bits. By following best practices for cleaning, storing, and recognizing signs of wear and tear, you can ensure that your button bits remain in top condition for all your rock drilling projects.
Maximizing Efficiency with the Right Button Bit
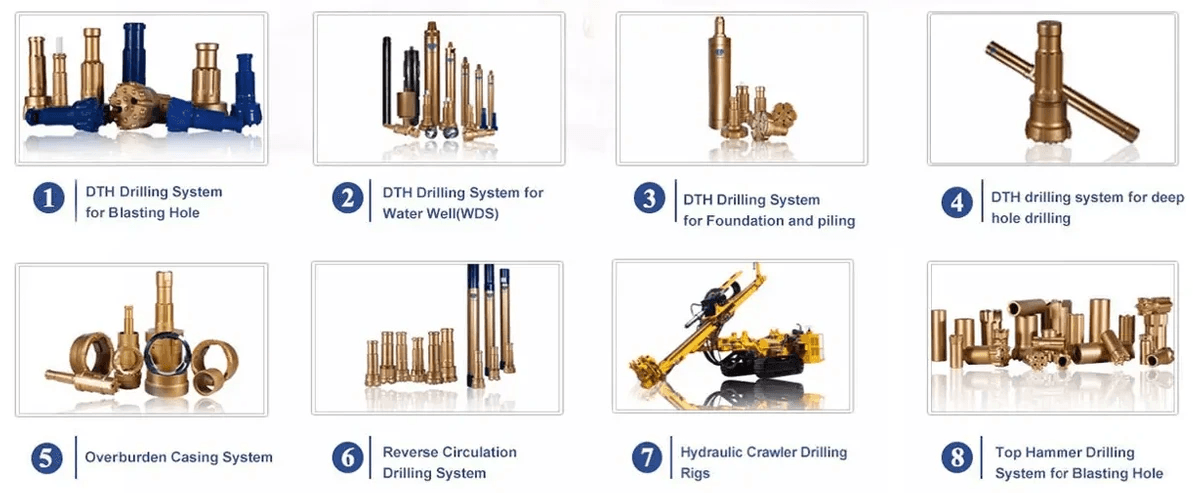
Improving Drilling Speed and Accuracy with the Right Button Bit
Regarding rock drilling, the right button bit can make all the difference in drilling speed and accuracy. By choosing a button bit that matches the hardness of the rock formation, you can significantly reduce drilling time and ensure precise hole placement. The design of the button bit also plays a crucial role in improving drilling efficiency, so it's essential to select one specifically tailored to your drilling needs.
One of the key factors to consider when selecting the right button bit is the material it is made of. Advanced materials such as tungsten carbide are known for their durability and resistance to wear, making them ideal for drilling in tough rock formations. By leveraging these advanced materials in button-bit design, you can ensure that your drilling equipment can withstand the rigors of rock drilling, leading to improved efficiency and longevity. These materials can also contribute to better penetration rates and increased productivity, ultimately saving time and costs on drilling operations.
Leveraging Advanced Technology in Button Bit Design
With technological advancements, button-bit design has evolved to enhance drilling performance. Modern button bits are engineered to deliver superior penetration rates and longer lifespans, from innovative carbide grades to optimized flute designs. By leveraging these technological advancements, drillers can achieve higher productivity and cost savings on their projects. TEAMWHOLE's thread button bit stands out in the market due to its cutting-edge design that maximizes energy transfer for faster drilling and reduced wear on the bit. Using advanced materials and manufacturing techniques ensures that TEAMWHOLE's button bits offer exceptional durability and resistance to abrasion, resulting in extended operational life and minimized downtime for maintenance.
How TEAMWHOLE's Thread Button Bit Stands Out in the Market
TEAMWHOLE's thread button bits are designed with precision engineering and high-quality materials to provide unmatched performance in rock drilling applications. With a wide range of thread types and carbide shapes, TEAMWHOLE's button bits offer versatility and reliability for various drilling conditions. Their commitment to continuous improvement sets them apart as leaders in the industry.
By understanding the importance of choosing the right button bit and leveraging advanced technology in design, drillers can maximize efficiency and achieve optimal results in their rock drilling projects. Whether improving speed and accuracy or investing in high-quality thread button bits like those offered by TEAMWHOLE, making informed decisions is key to success in rock drilling.
The Future of Innovation in Button Bit Technology
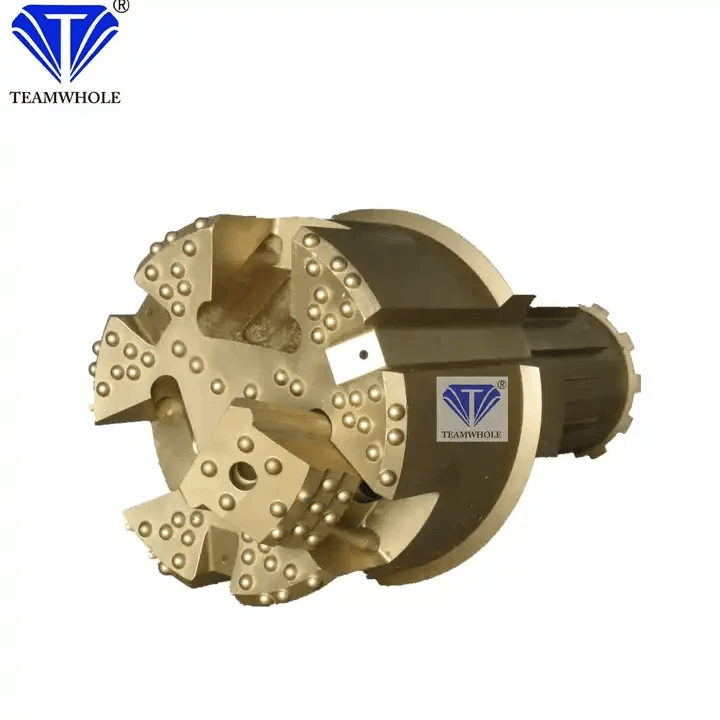
In conclusion, understanding the importance of choosing the right drilling button bit is crucial for the success of any rock drilling project. By considering factors such as rock formation, drilling application, and button-bit design, you can ensure the longevity and performance of your button bits.
Ensuring
the Longevity and Performance of Your Button Bits
Proper maintenance and care are essential for extending the lifespan of your button bits. Regular cleaning and storage practices can help prevent wear and tear, ultimately maximizing their efficiency and performance throughout their usage.
Making Informed Decisions When Investing in Button Bits
When investing in button bits for rock drilling, it's important to consider factors such as rock formation, drilling application, and technological advancements in button-bit design. Making informed decisions based on these considerations can increase efficiency and cost-effectiveness in your drilling projects.
Considering the rock formation is crucial when investing in button bits, as different rock types require different bit designs and materials for optimal drilling performance. For example, softer rock formations may benefit from button bits with larger, more widely spaced buttons, while harder formations may require smaller buttons with a higher density. By considering the specific geological conditions of your drilling site, you can select the most suitable button bits to maximize efficiency and minimize wear and tear.
As technology continues to advance, so does innovation in button-bit technology. With ongoing developments in materials, design, and manufacturing processes, the future holds promising improvements in button bit performance and longevity for rock drilling applications. One area of potential advancement lies in the use of advanced materials such as composites and ceramics, which offer increased durability and resistance to wear. Additionally, advancements in design may lead to more efficient cutting structures and improved fluid dynamics, resulting in better penetration rates and overall drilling performance. Furthermore, advancements in manufacturing processes, such as 3D printing and advanced machining techniques, may allow for more precise and consistent production of button bits, leading to improved quality and performance.