Introduction
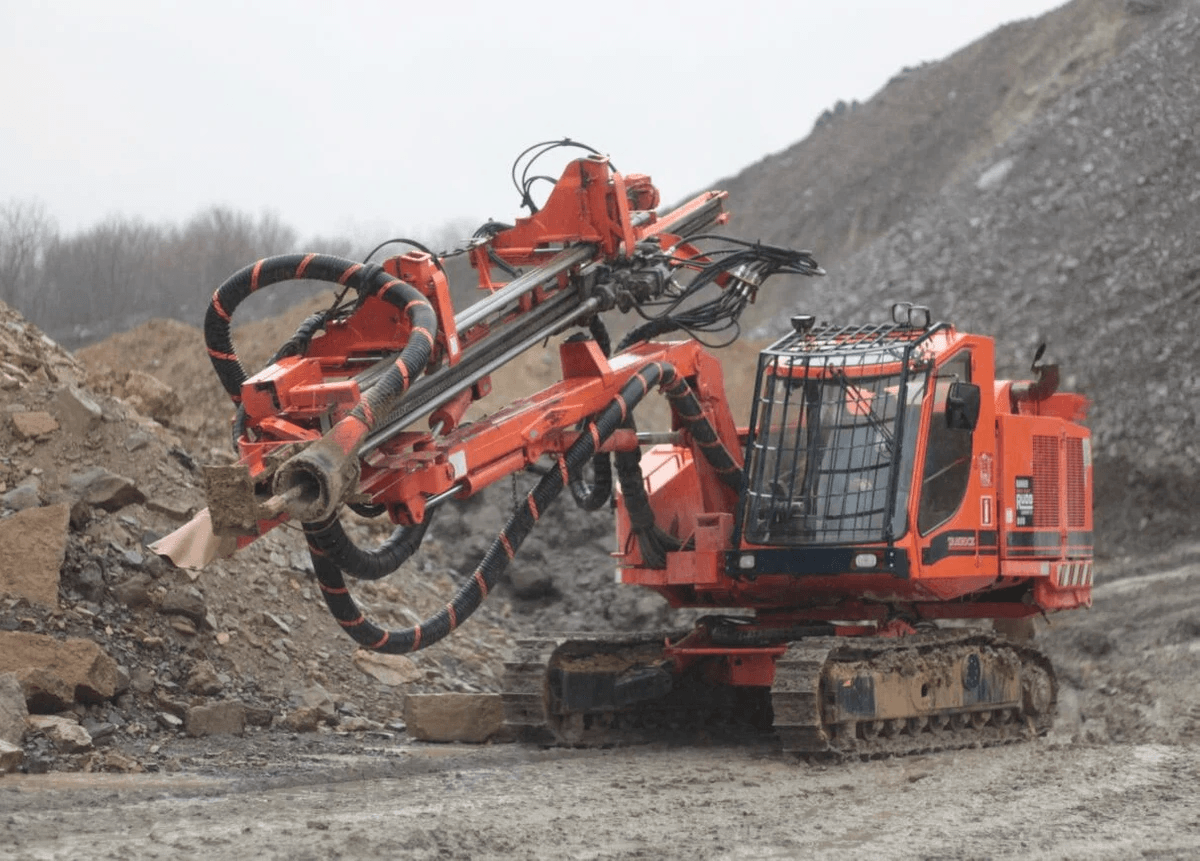
When it comes to water well drilling tools, quality is key. From DTH hammer manufacturers to drilling rig drill bits, every component plays a crucial role in the success of a drilling operation. Understanding the importance of using top-notch equipment and exploring the world of oil and gas drill bit manufacturers is essential for achieving optimal results.
Understanding Water Well Drilling Tools
Water well drilling tools encompass various equipment, including DTH hammers, drill bits, and drilling rigs. These tools are designed to penetrate the earth's surface and access underground water sources for various applications such as irrigation, residential water supply, and commercial use. Quality is paramount when choosing the right equipment for water well drilling. Opting for reputable DTH hammer manufacturers ensures that the tools are durable, efficient, and reliable, ultimately leading to successful and cost-effective drilling operations.
Importance of Using Quality DTH Hammer Manufacturers
Choosing reputable DTH hammer manufacturers is critical for ensuring the durability and performance of drilling operations. High-quality hammers are constructed with precision engineering and advanced materials to withstand the rigors of deep well drilling while delivering maximum impact force and energy transfer. Additionally, reputable manufacturers often provide comprehensive customer support, including technical assistance and replacement parts, to ensure their products perform optimally. By investing in quality DTH hammer manufacturers, drilling operations can minimize downtime and maintenance costs, ultimately increasing productivity and profitability.
Exploring the World of Drilling Rig Drill Bits
Drilling rig bits are essential components that directly impact the efficiency and effectiveness of water well drilling. Oil drilling bits manufacturers offer diverse products tailored to different geological conditions, ensuring optimal penetration rates and durability in challenging environments. These drill bits come in various designs, including roller cone bits, fixed cutter bits, and diamond core bits, each designed for specific drilling needs. The materials used in manufacturing these drill bits also play a crucial role in their performance, with tungsten carbide being a popular choice for its hardness and resistance to wear and tear.
The Basics of Water Well Drilling Tools
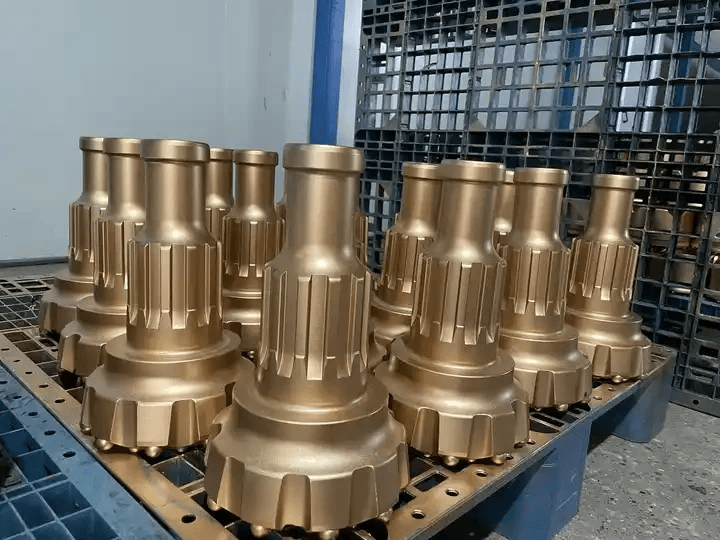
Core Components of Drilling
Rig Bits
Regarding water well drilling tools, the core components of drilling rig bits are crucial for successful operations. These include the bit body, cutting structure, and bit shank, all designed to withstand demanding drilling conditions into various rock formations.
The bit body is typically made of high-strength steel to ensure durability and resistance to wear and tear. This component houses the cutting structure and supports the entire drilling operation. The design of the bit body is crucial in determining the efficiency and effectiveness of the drilling process, as it directly impacts the stability and performance of the drilling rig.
Key Features of Oil Drilling Bits
Oil drilling bits are indispensable tools in the oil and gas industry. Their performance significantly impacts the overall success of drilling operations. To ensure optimal efficiency and longevity, several key features should be considered:
- Durability: Can withstand extreme pressures and temperatures encountered in deep-sea and other challenging environments.
- Precision Engineering: Guarantees accurate navigation through diverse rock formations.
- Advanced Cutting Technology: Enables faster penetration and reduces equipment wear.
Combining these factors is essential for maximizing the performance of oil drilling bits and minimizing downtime.
Operators can enhance drilling efficiency and reduce operational costs by selecting bits with these characteristics.
Exploring the Functionality of Oil and Gas Drill Bit Manufacturers
Understanding the functionality of oil and gas drill bit manufacturers is essential for selecting the right tools for your drilling needs. These manufacturers utilize cutting-edge technology and materials to produce high-performance bits that can withstand the rigors of oil and gas exploration. When exploring drill bit manufacturers, it's important to consider their reliability and durability track record in various drilling conditions. Additionally, look for manufacturers that offer customization options to tailor the drill bits to specific project requirements, ensuring optimal performance and efficiency.
DTH Hammer Manufacturers: What to Look For
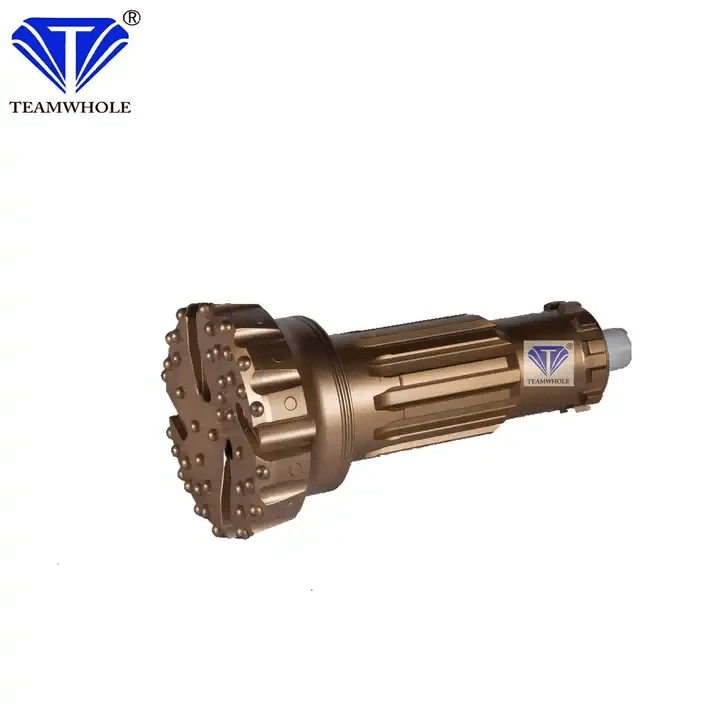
When searching for DTH hammer manufacturers, it's crucial to prioritize quality materials and construction. The durability and reliability of the tools largely depend on the choice of materials used and the precision of construction. High-grade steel and meticulous engineering ensure that the DTH hammers can withstand the harsh conditions of drilling operations, providing long-lasting performance.
Quality Materials and Construction
Investing in DTH hammer manufacturers that prioritize quality materials and construction is essential for ensuring the efficiency and longevity of water well drilling tools. High-quality steel alloys, advanced forging techniques, and stringent quality control measures contribute to producing durable, high-performance DTH hammers that can withstand the rigors of drilling in various geological formations.
Advanced heat-treatment processes are also crucial for enhancing the durability and performance of DTH hammers. Manufacturers can improve the material's hardness, strength, and resistance to wear and corrosion by subjecting the steel components to specific heating and cooling cycles. This results in DTH hammers that maintain their sharpness and efficiency over prolonged periods of use, reducing the frequency of replacements and downtime for water well drilling operations.
Importance of Advanced H
eat Treatment
Advanced heat-treatment processes are crucial for enhancing the performance of DTH hammers. By meticulously controlling temperatures, these processes optimize the metallurgical properties of hammer components, resulting in superior strength, hardness, and wear resistance. This translates to:
- Extended tool lifespan: Heat-treated hammers endure longer, reducing replacement costs.
- Improved durability: Enhanced toughness enables hammers to withstand demanding drilling conditions.
- Increased productivity: Less downtime due to tool failures leads to faster project completion.
- Cost savings: Reliable tools contribute to overall operational efficiency and reduced expenses.
Incorporating advanced heat-treatment processes into DTH hammer manufacturing is essential for maximizing tool performance and minimizing operational costs in water well drilling.
Teamwhole: A Leader in DTH Hammer Manufacturing
Teamwhole is a leading manufacturer of DTH hammers, renowned for its unwavering commitment to excellence. The company's focus on precision engineering and rigorous quality control results in top-tier DTH hammers that excel in water well drilling applications.
Teamwhole's superior products are a result of several key factors:
- Meticulous Material Selection: Only the highest quality materials are used in manufacturing.
- Advanced Heat Treatment: State-of-the-art heat treatment processes optimize hammer performance and durability.
- Precision Engineering: Cutting-edge manufacturing techniques ensure unmatched accuracy and precision.
By investing in Teamwhole DTH hammers, water well drilling professionals can confidently tackle even the most challenging projects.
Choosing the Right Drilling Rig Drill Bit
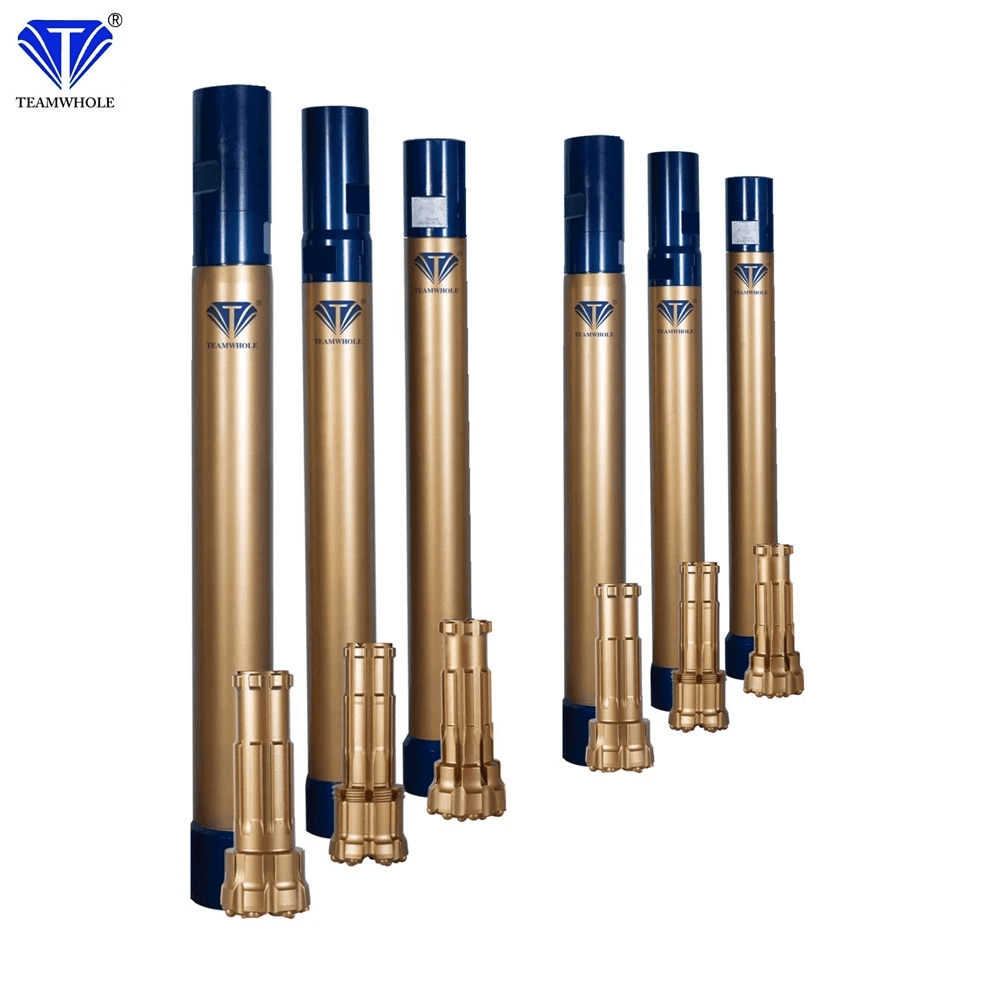
Understanding the bit head face designs is crucial when choosing the right drilling rig drill bit. Different face designs, such as flat, conical, and chisel-shaped, are suited for specific drilling conditions and offer unique advantages in different rock formations.
The importance of different carbide shapes cannot be overstated when selecting a drilling rig drill bit. Carbide shapes like spherical, ballistic, and parabolic play a significant role in determining the bit's cutting efficiency and durability, making it essential to choose the right shape for the job.
The impact of rock formations on bit selection is undeniable. Different formations require different types of bits to achieve optimal drilling performance. For instance, soft rock formations may call for a different type of bit than hard rock formations, highlighting the need for careful consideration when choosing a drilling rig drill bit.
The type of drilling rig drill bit you choose can also impact your operations' overall cost and efficiency. Using the wrong bit for a specific rock formation can lead to increased wear and tear on the equipment, resulting in higher maintenance costs and longer drilling times. By carefully analyzing the rock formations and selecting the appropriate drill bit, you can minimize these risks and ensure a smoother, more cost-effective drilling process.
Now that we've explored the importance of understanding bit head face designs and carbide shapes and considering rock formations in bit selection, it's clear that choosing the right drilling rig drill bit requires careful analysis and expertise. Considering these factors, you can ensure efficient and successful water well drilling operations.
Benefits of Using Quality Oil Drilling Bits
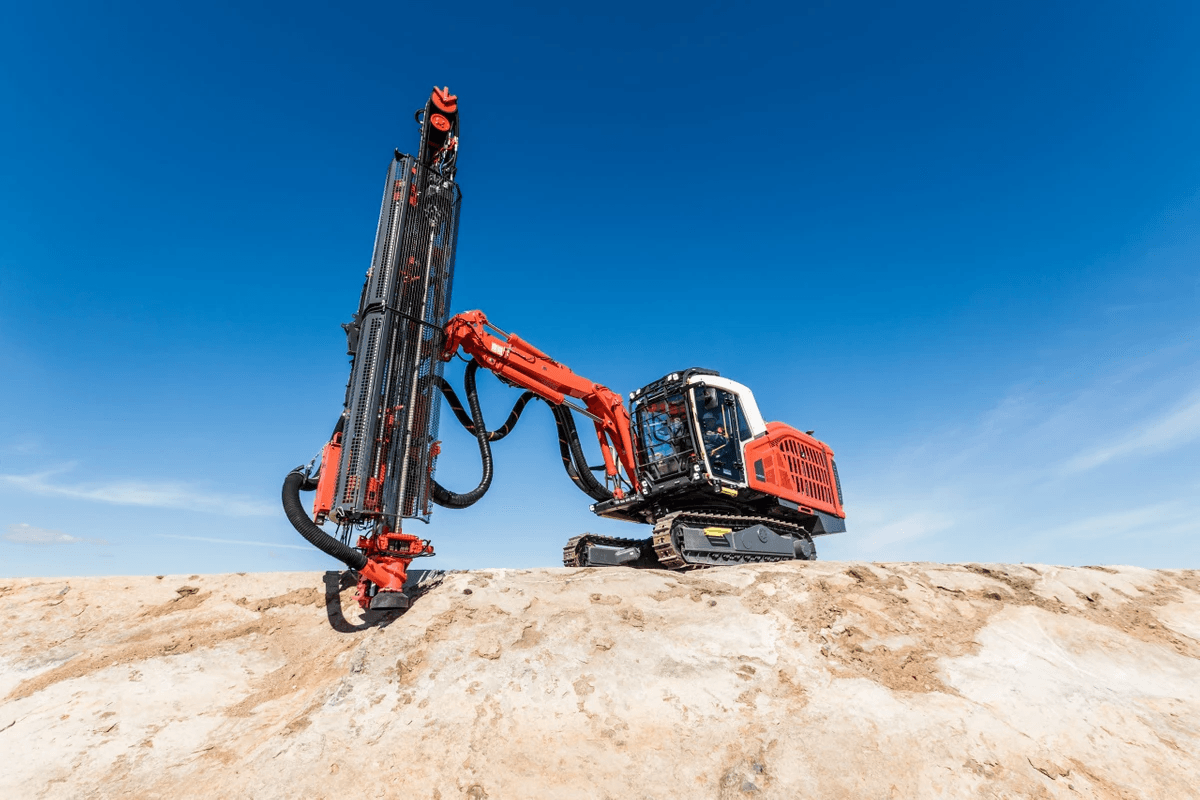
Regarding oil drilling, the importance of using quality oil drilling bits cannot be overstated. These bits offer extreme protection against wear and fatigue, ensuring they can withstand the harsh drilling conditions deep into the earth. This means they can last longer and perform more efficiently, ultimately saving time and money in the long run.
In addition to their durability, quality oil drilling bits offer versatility in tackling different challenges encountered during drilling operations. Whether navigating through hard rock formations or dealing with abrasive materials, these bits are designed to handle a wide range of conditions easily. This versatility makes them a valuable asset for any drilling project, providing reliability and performance when it matters most.
Teamwhole's diverse line of DTH bits exemplifies the benefits of using quality oil drilling bits. With a focus on precision engineering and advanced materials, Teamwhole offers a range of bits tailored to meet the specific needs of different drilling applications. From standard designs to custom solutions, their commitment to quality ensures that their bits deliver exceptional performance in any situation.
Teamwhole's commitment to quality extends beyond the design of its oil drilling bits. It also prioritizes durability and longevity, ensuring its products can withstand the harsh conditions of drilling operations. This means less frequent replacements and maintenance, saving drilling companies time and money. By choosing Teamwhole's quality bits, drillers can trust that they are making a long-term investment in their equipment.
With extreme protection against wear and fatigue, versatility in tackling different challenges, and a diverse line of DTH bits from Teamwhole, it's clear that using quality oil drilling bits is essential for ensuring successful and efficient drilling operations. By investing in top-notch equipment, drillers can confidently tackle any project while maximizing productivity and minimizing downtime.
Ensure Longevity and Efficiency in Water Well Drilling
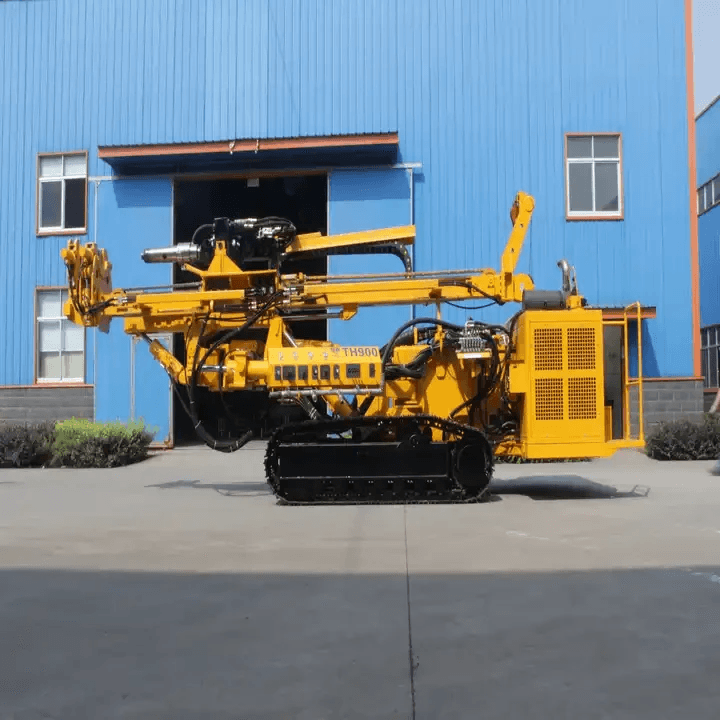
Water well drilling tools play a crucial role in ensuring the longevity and efficiency of drilling operations. By using quality DTH hammer manufacturers and choosing the right drilling rig drill bit, drillers can make informed decisions that lead to successful outcomes. Embracing innovation in drilling technology is essential for staying ahead in the industry.
Choosing high-quality water well drilling tools is essential for ensuring longevity and efficiency in drilling operations. DTH hammer manufacturers like Teamwhole offer durable and reliable products that withstand the toughest conditions and provide long-lasting performance. Investing in top-notch drilling rig bits from reputable oil drill bits manufacturers ensures smooth and efficient drilling processes.
Making Informed Decisions in Tool Selection
Selecting the right tools for water well drilling requires careful consideration of various factors. Exploring the world of oil and gas drill bit manufacturers is crucial to finding products that meet specific project requirements. Understanding the impact of different rock formations on bit selection is vital for making informed decisions when choosing oil well drilling bits.
Embracing Innovation in Drilling Technology
Innovation is key in driving advancements in water well drilling tools, DTH hammer manufacturing, and oil drill bits production. By embracing cutting-edge technologies and materials, manufacturers can develop more efficient and versatile products that cater to evolving industry needs. Staying updated with the latest innovations ensures that drillers can tackle challenges effectively.
By staying ahead of the curve in drilling technology, manufacturers can also improve safety measures for workers on-site. Innovations in drilling tools and equipment can lead to the development of more ergonomic designs and automated features, reducing the physical strain on workers and minimizing the risk of accidents. Additionally, advanced technologies such as real-time monitoring and data analytics can provide valuable insights into drilling operations, allowing for proactive maintenance and hazard prevention.