Introduction
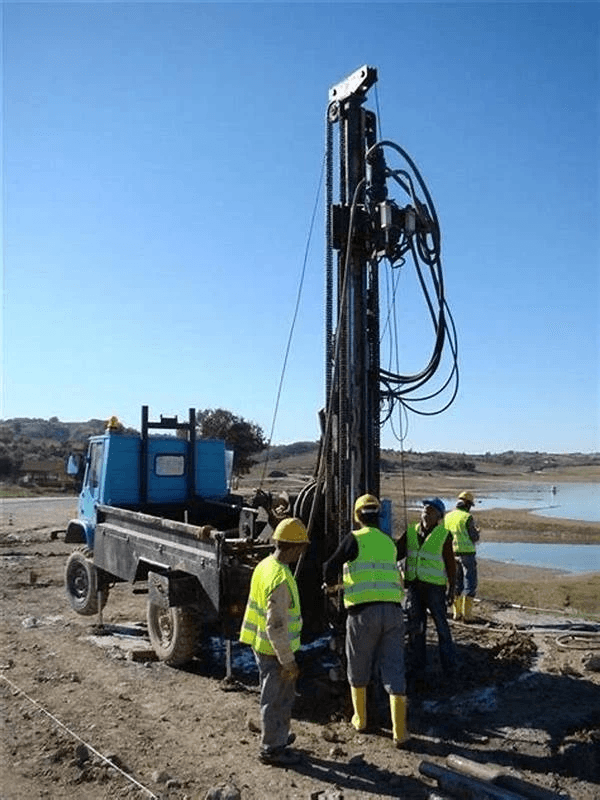
When it comes to drilling in tough and challenging environments, the use of Down-the-Hole (DTH) Hammers has become increasingly popular. These powerful tools are essential for rotary percussive drilling, providing efficient and reliable results in various industries. From mining applications to water well drilling and foundation construction, DTH Hammers have proven to be indispensable for their versatility and effectiveness.
Understanding the Functionality
DTH Hammers, also known as Down the Hole Hammers, are specialized tools used for down-the-hole drilling. They work by delivering powerful blows to the drill bit, enabling it to break through tough rock formations with ease. This unique functionality sets them apart from other drilling tools like Top Hammer systems, making them ideal for deep hole drilling in challenging terrains.
Key Features of Drilling Hammers
One of the key features of DTH Hammers is their ability to provide efficient and precise drilling performance even in hard rock formations. They are designed with durable components that can withstand high impact forces, ensuring long-lasting reliability. Additionally, these hammers come in various sizes and designs to accommodate different project requirements.
Advantages of Using Drilling Hammers
The advantages of using DTH Hammers are numerous. They offer increased efficiency by delivering faster penetration rates and reduced downtime during drilling operations. Their versatility allows them to be used in various conditions, making them suitable for a wide range of applications such as mining, water well drilling, and foundation construction.
What is a Drilling Hammer?
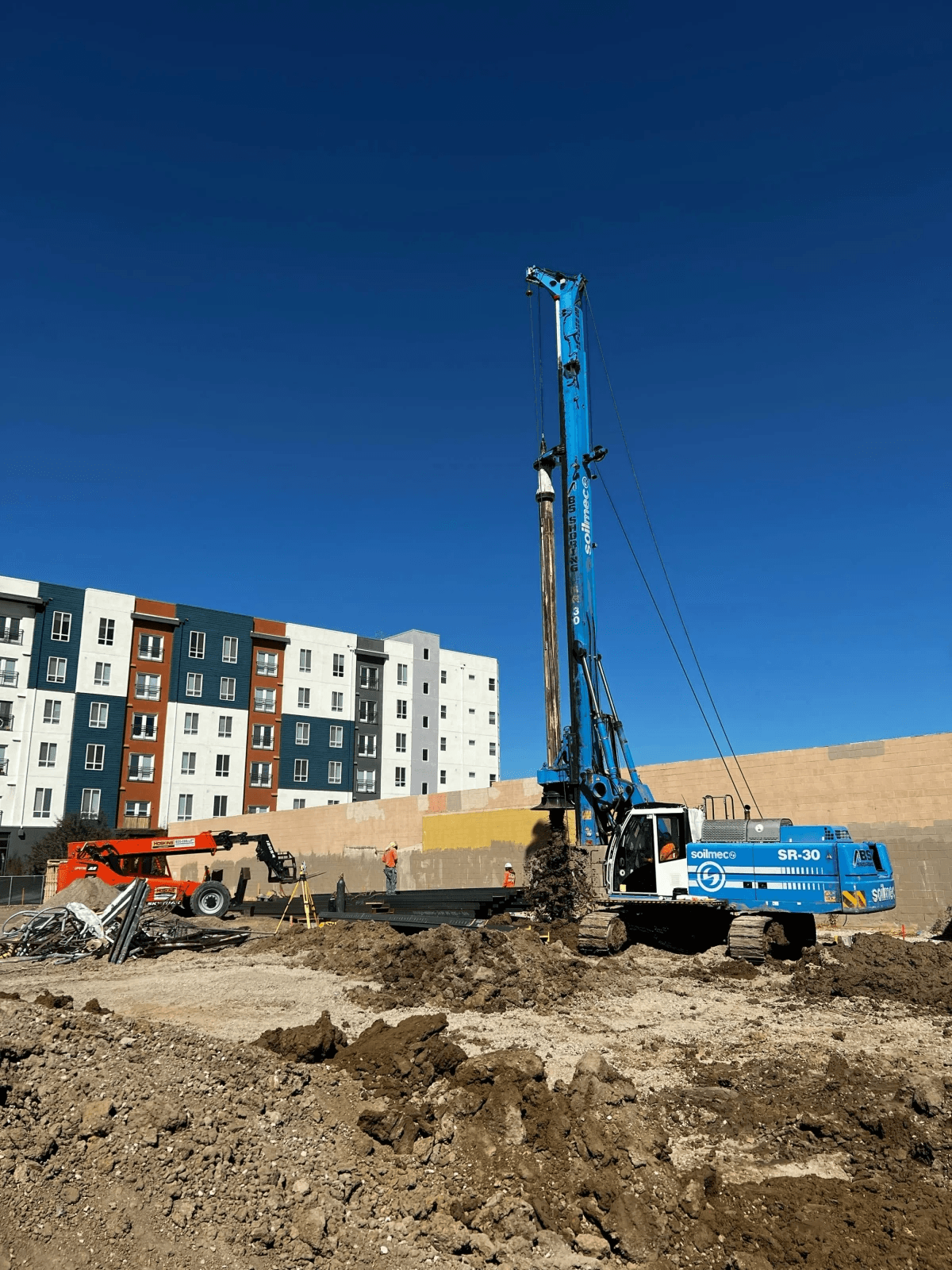
Drilling hammers, also known as Down-the-Hole (DTH) Hammers, are essential tools used in rotary percussive drilling. Their main purpose is to provide powerful and efficient drilling capabilities in various industries such as mining, construction, and water well drilling. DTH Hammers are specifically designed for down-the-hole drilling, where the hammer is located behind the drill bit.
Definition and Purpose
A drilling hammer is used for down-the-hole drilling, where it delivers powerful blows to the drill bit while maintaining constant pressure on the rock surface. This allows for faster and more efficient drilling compared to traditional methods. DTH Hammers are crucial in achieving deeper boreholes and higher penetration rates in hard rock formations.
A drilling hammer is designed to withstand the intense pressure and force required for down-the-hole drilling, making it an essential tool for mining and construction industries. Its ability to deliver powerful blows to the drill bit while maintaining constant pressure on the rock surface ensures precise and effective drilling operations. By using DTH Hammers, operators can achieve greater accuracy and speed in creating boreholes, resulting in significant time and cost savings for large-scale projects.
Types of Drilling Hammers
There are two main types of DTH Hammers: Top Hammer and Down the Hole Drilling. Top Hammer drills use a percussive mechanism located above the drill bit, suitable for smaller diameter holes and softer rock formations. On the other hand, Down-the-Hole Hammers provide direct impact at the bottom of the hole, making them ideal for larger diameter holes and harder rock formations.
In addition to the percussive mechanism, both types of DTH Hammers also consist of a drill bit, drill pipe, and a drilling fluid system. The drill bit is the cutting tool attached to the bottom of the drill string and is responsible for creating the hole. The drill pipe is a hollow tube that serves as a conduit for the drilling fluid and provides a means for transferring energy from the surface to the drill bit. The drilling fluid system, also known as drilling mud, helps to cool and lubricate the drill bit, carry rock cuttings to the surface, and provide stability to the borehole walls.
Core components of a Drilling Hammer
The core components of a Drilling Hammer include the piston, valve system, drill bit, and external casing. The piston delivers high-velocity blows to the drill bit through compressed air or hydraulic power. The valve system controls air flow to optimize impact energy transfer while minimizing energy loss. The drill bit is designed with tungsten carbide buttons or inserts to withstand high-impact forces and abrasion during drilling operations.
The external casing of the Drilling Hammer provides protection and support for the internal components, ensuring durability and longevity. Made of high-strength materials such as steel or aluminum, the casing is designed to withstand the intense forces and vibrations generated during drilling operations. Additionally, the external casing also helps to contain any debris or particles that may be dislodged during drilling, maintaining a clean and safe work environment for operators.
Use Cases
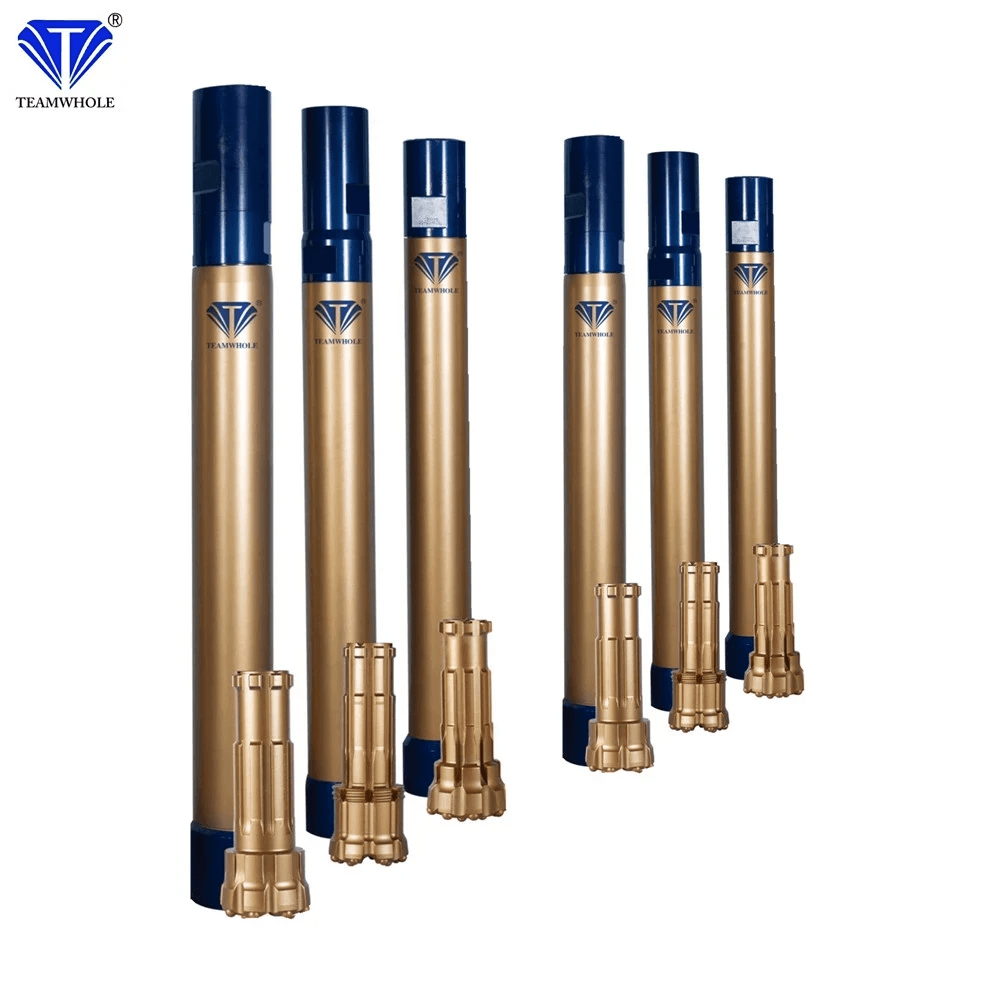
Drilling hammers are widely used in various industries for their efficiency and versatility. In mining applications, drilling hammers are used for down-the-hole drilling, where the hammer is fitted with a drill bit to penetrate hard rock formations. This method, also known as rotary percussive drilling, is essential for extracting minerals and ores from deep within the earth.
Mining Applications
Drilling hammers play a crucial role in the extraction of minerals and ores through down-the-hole (DTH) drilling. This method involves using a Down the Hole Hammer fitted with a drill bit to create boreholes in hard rock formations. The high impact force generated by the hammer allows for efficient penetration, making it an indispensable tool in mining operations.
In addition to mining operations, drilling hammers are also essential in water well drilling. The high impact force of the hammer allows for efficient penetration through hard rock formations, making it ideal for creating boreholes in search of water sources. Down the Hole Hammer fitted with a drill bit is commonly used in water well drilling to reach deep into the earth and access clean and reliable water sources for communities and industries.
Water Well Drilling
In water well drilling, DTH hammers are utilized to create boreholes for accessing underground water reservoirs. The hammer's ability to deliver powerful impacts at high frequency enables it to effectively penetrate various types of geological formations, ensuring the successful construction of water wells in different terrains.
In addition to their effectiveness in penetrating geological formations, DTH hammers also offer the advantage of minimal deviation during drilling. This precision is crucial in water well drilling, as it ensures that the boreholes are accurately positioned to access underground water reservoirs. Furthermore, the use of DTH hammers results in faster drilling times, allowing for efficient construction of water wells in various terrains without compromising on quality.
Foundation Construction
When it comes to foundation construction, DTH hammers are employed to create boreholes for installing support structures such as piles and caissons. The precision and power of these tools allow for accurate and efficient drilling even in challenging soil conditions, making them indispensable in laying strong foundations for buildings and infrastructure projects.
In addition to their precision and power, DTH hammers are also known for their versatility in handling various types of soil conditions. Whether it's hard rock, soft soil, or even fractured formations, these tools can adapt to the challenges of different terrains, ensuring that the foundation construction process remains efficient and reliable. This adaptability makes DTH hammers a top choice for construction projects where the ground conditions may vary across the site.
Advantages of Using Drilling Hammers
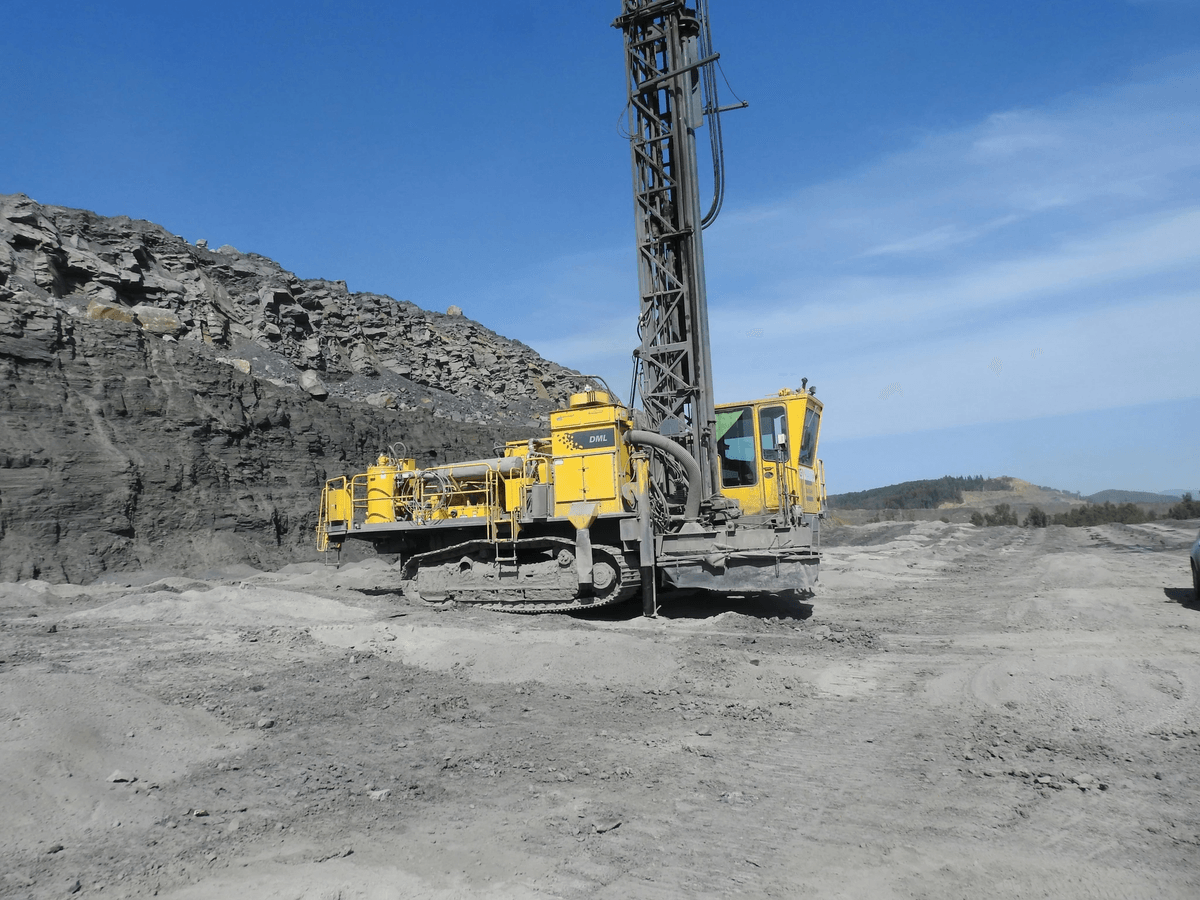
A drilling hammer is used for rotary percussive drilling (down-the-hole hammer) and is known for its efficiency, versatility, and cost-effectiveness. Down the Hole (DTH) Hammers are essential tools in the drilling industry, offering numerous advantages over traditional drill bits.
Increased Efficiency
One of the key advantages of using a drilling hammer is its increased efficiency in comparison to other drilling tools. The Down-the-hole hammer delivers powerful blows to the drill bit, resulting in faster and more effective penetration into hard rock formations. This increased efficiency translates to reduced project timelines and costs, making it a highly sought-after tool for various industries.
In addition to its increased efficiency, the drilling hammer also offers versatility in various conditions. Whether it's hard rock formations or softer soil, the Down-the-hole hammer is designed to deliver powerful blows that can adapt to different drilling environments. This means that regardless of the project requirements, this tool can be relied upon to provide consistent and effective performance, making it a valuable asset for industries such as construction, mining, and geothermal energy.
Versatility in Various Conditions
Drilling hammers are designed to be versatile in various conditions, making them suitable for a wide range of applications such as mining, water well drilling, and foundation construction. Whether it's hard or soft rock formations, the Down-the-hole hammer can adapt to different geological conditions with ease, providing consistent performance across different projects.
In addition to its adaptability to different geological conditions, drilling hammers also offer cost-effectiveness in various applications. With their ability to deliver consistent performance across different projects, these hammers can help reduce downtime and maintenance costs, ultimately saving time and money for operators. This cost-effective feature makes them a valuable asset for businesses looking to optimize their drilling operations without compromising on quality.
Cost-Effectiveness
In addition to their efficiency and versatility, DTH Hammers offer cost-effectiveness due to their ability to complete projects in a shorter timeframe. This results in reduced labor costs and overall project expenses. Furthermore, their durability ensures minimal downtime for maintenance or replacement, further contributing to cost savings for companies utilizing these tools.
Additionally, the cost-effectiveness of DTH Hammers is further enhanced by their ability to operate in various types of geological formations, reducing the need for specialized equipment or tools. This versatility allows companies to streamline their operations and reduce the overall investment required for specific projects. By minimizing the need for additional resources, companies can maximize their cost savings and improve their bottom line.
Conclusion
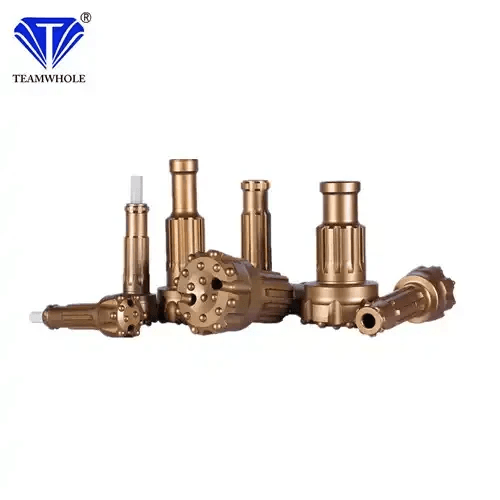
When it comes to the importance of drilling hammers in various industries, their versatility and efficiency cannot be overstated. Whether it's for mining applications, water well drilling, or foundation construction, drilling hammers play a crucial role in getting the job done quickly and effectively. As industries continue to evolve, future innovations in drilling hammers are likely to focus on improving efficiency and durability to meet the demands of different projects.
Importance in Various Industries
Drilling hammers are used across a wide range of industries due to their ability to efficiently break through tough surfaces. From mining operations that require precision drilling to construction projects that demand speed and power, these tools are indispensable. Their versatility also makes them essential for water well drilling, where accuracy is paramount.
Drilling hammers have also found a crucial role in the oil and gas industry, where they are used to extract resources from deep beneath the earth's surface. The precision and power of these tools make them ideal for accessing hard-to-reach deposits, contributing to the efficient extraction of these valuable resources. Additionally, drilling hammers are utilized in geotechnical engineering to obtain soil samples for analysis, providing vital information for construction projects and infrastructure development.
Future Innovations in Drilling Hammers
As technology continues to advance, future innovations in drilling hammers will likely focus on enhancing their durability and precision. This could involve improvements in materials used for construction and advancements in engineering design to ensure they can withstand even the toughest conditions. Additionally, there may be a focus on incorporating smart technology into drilling hammers, allowing for real-time monitoring of performance and predictive maintenance to prevent breakdowns. Furthermore, advancements in ergonomics may lead to more user-friendly designs that reduce operator fatigue and improve overall productivity on the job site.
Choosing the Right Drilling Hammer for Your Project
When it comes to selecting the right drilling hammer for your project, it's important to consider factors such as the type of material you'll be working with and the specific requirements of your project. Understanding the differences between drill bits vs down-the-hole hammers and top hammer vs down-the-hole drilling will help you make an informed decision that ensures optimal results.
After considering the type of material and specific project requirements, it's also essential to factor in the size and depth of the holes you'll be drilling. This will help determine whether a top hammer or down-the-hole drilling method is more suitable for your project. Additionally, understanding the differences between drill bits and down-the-hole hammers will enable you to select the most appropriate tool for achieving precise and efficient results. By taking these factors into account, you can ensure that your drilling hammer choice aligns perfectly with the unique needs of your project.
Remember, whether you're dealing with Down-the-Hole (DTH) Hammers or Rotary percussive drilling (down-the-hole hammer), choosing the right tool for the job is crucial for achieving success in your project.